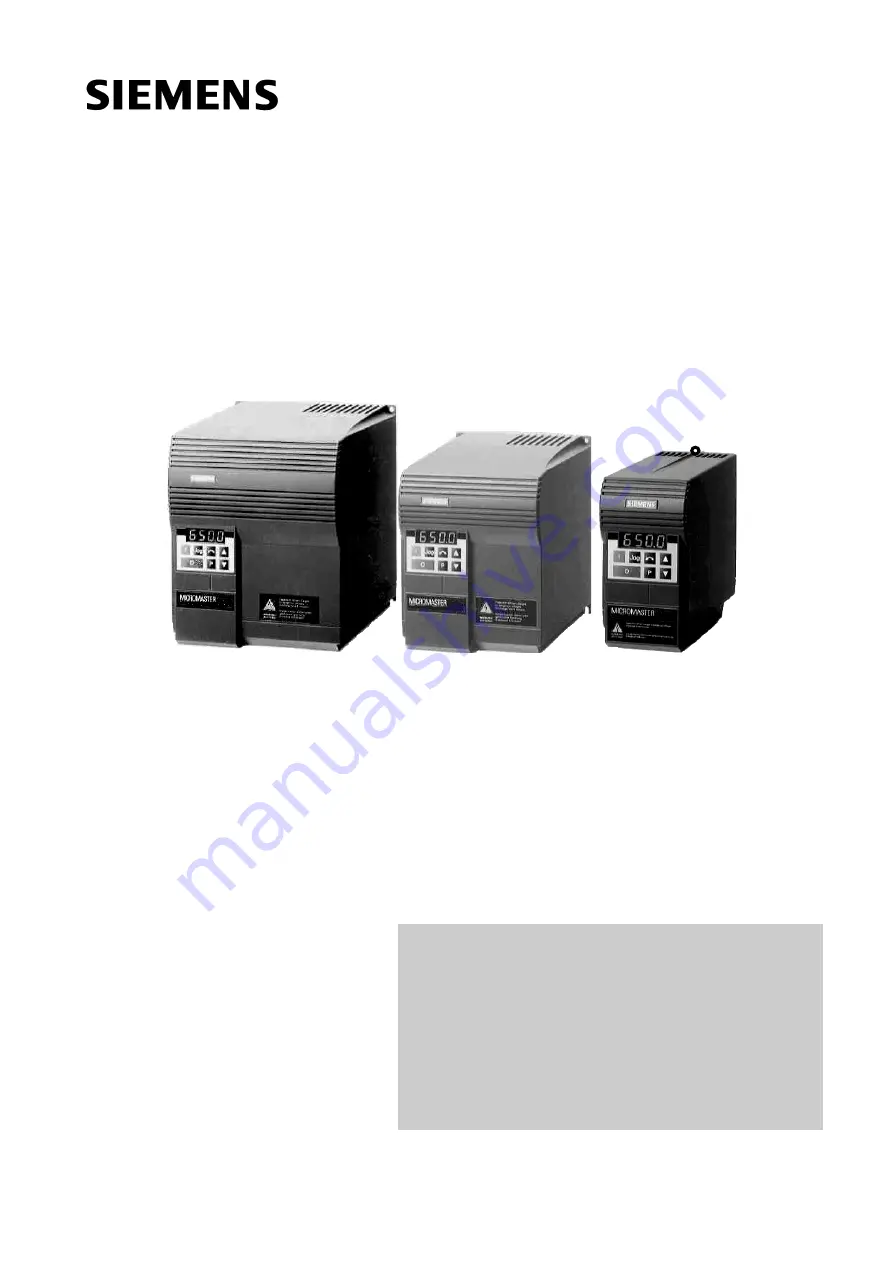
© Siemens plc 1999
G85139-H1750-U049-C1
19/08/99
Contents
SAFETY INSTRUCTIONS..................................................... 3
1. OVERVIEW....................................................................... 4
2. INSTALLATION.............................................................. 10
3. FRONT PANEL CONTROLS & BASIC OPERATION ... 18
4. OPERATING MODES..................................................... 21
5. SYSTEM PARAMETERS ............................................... 24
6. FAULT CODES............................................................... 39
7. SPECIFICATIONS .......................................................... 40
8. SUPPLEMENTARY INFORMATION ............................. 43
MICROMASTER
Operating Instructions