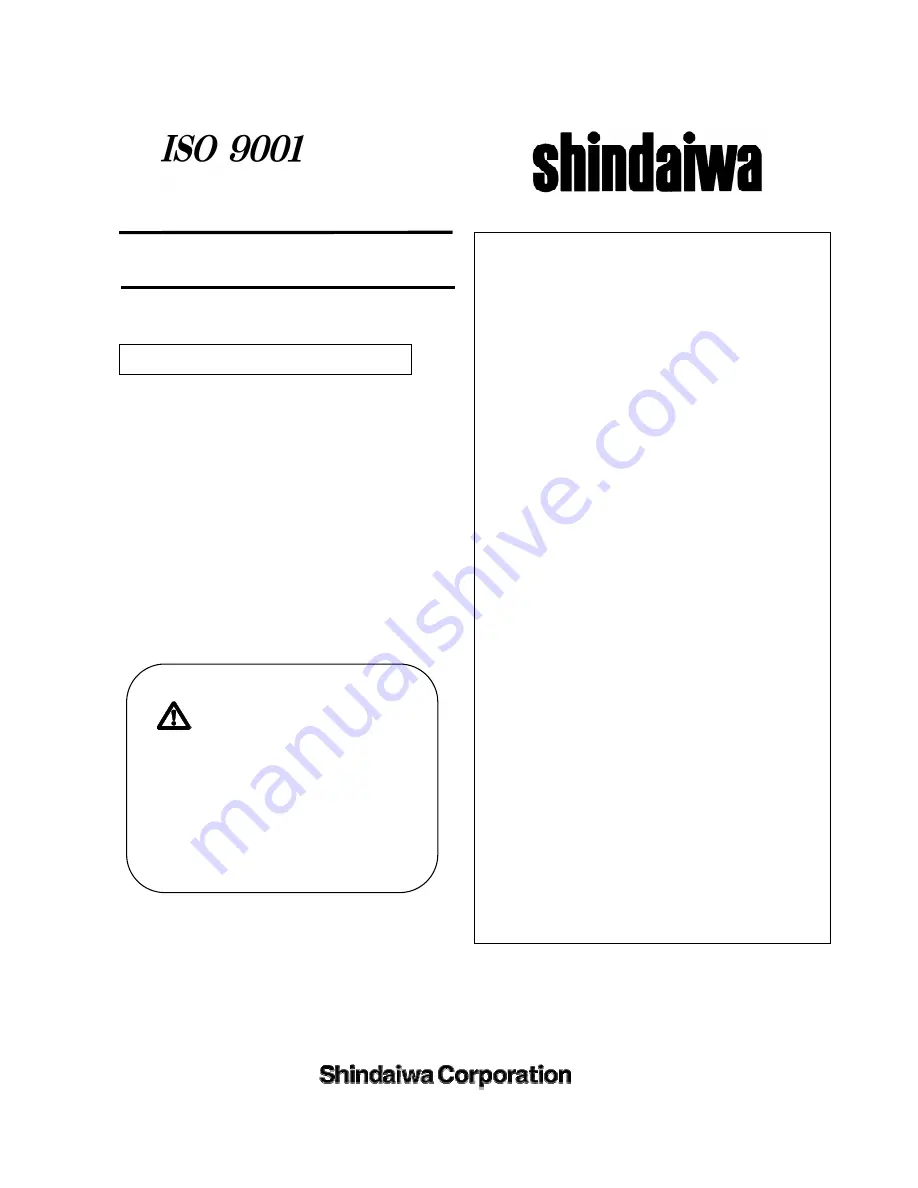
Caution
Do not operate the generator/
welder, or any other appliance,
before you have read and
understand the instructions for use
and keep near for readily use
OWNER’S MANUAL
GENERATOR / WELDER
DGW310DMC
DGW310MC
Sound Proof
Vertical, Water-Cooled
4-Cycle Diesel Engine
Table of Contents
1. Safety Guidelines ···················································
2
2. Specifications ·························································
6
3. Use ···········································································
7
4. Parts ········································································
7
5. Incorporated ···························································
10
5-1
.
Eco Welding
10
5-2
.
Display
10
5-3
.
Frequency Change
10
5-4
.
Monitor Lamp
10
5-5
.
Remote Control (Option)
12
5-6
.
Earth Leakage Relay/Grounding
13
5-7
.
Slow-Down Feature
15
6. Initialization & Pre-check ·······································
16
6-1
.
Checking Engine Oil
16
6-2
.
Checking Coolant/Water
17
6-3
.
Checking Fuel
18
6-4
.
Leakage Check for the above
18
6-5
.
Checking Battery
19
7. Operation ································································
20
7-1
.
Start
20
7-2
.
Stop
22
8. Welding Operation ··················································
22
8-1
.
Selection – Welding Cable
22
8-2
.
Polarity
23
8-3
.
Connection – Welding Cable
23
8-4
.
Welding
24
9
.
.
.
.
Generator Operation ·············································
26
9.1
.
Output Range
26
9-2
.
Output Limitation
27
9-3
.
Operation
28
10
.
.
.
.
Simultaneous Use – Weld & Generate ··············
30
11
.
.
.
.
Checking & Maintenance ····································
31
12
.
.
.
.
Long-term Storage ··············································
36
13
.
.
.
.
Trouble Shooting ················································
37
14. Warranty Sheet (Type B) ········································39
CERTIFIED
Summary of Contents for DGW310DMC
Page 2: ......
Page 41: ...39 Warranty Sheet Type B ...
Page 42: ...2006 10 MEMO Shindaiwa Corporation Hiroshima Japan ...