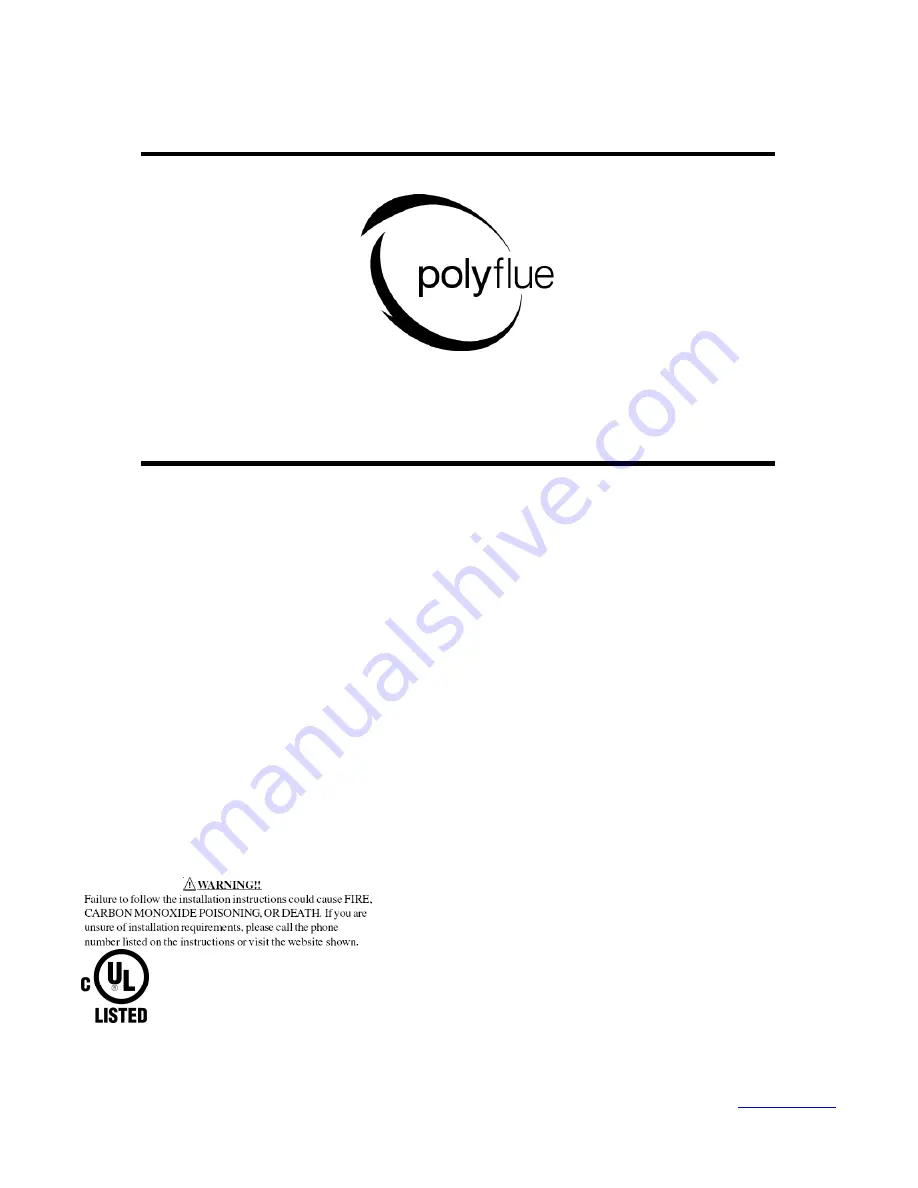
1
Installation and Maintenance Instructions
™
Single Wall Rigid & Flexible Polypropylene
Type BH Vent Class IIc 230
°
F/110
°
C Max Flue Temp
For Venting Residential & Commercial
Category II & IV Gas Burning Appliances
2”- 4”(
60-100mm) Diameter Vent For Positive, Neutral and Negative
Pressures up to 15” w.c. (3733 Pa)
Important: Do NOT install this product until you have read and fully understand these installation
instructions. Failure to comply with these instructions may result in injury or damage to property. An
improper installation will void any stated warranty.
Follow these instructions exactly as written.
Examine all components for possible shipping damage prior to installation.
Proper joint assembly is essential for a safe installation. Check integrity of joints upon
completion of assembly.
This venting system must be supported in accordance with these instructions.
Check for restricted vent movement through the walls, ceilings and roof penetrations. This
venting system must be free to expand and contract.
Do not mix Polyflue with pipe from different manufacturers.
5030 Corporate Exchange Blvd
Grand Rapids, MI 49512
Call 800-992-8368
Fax 877-393-4145
www.Polyflue.com
Tested and Listed to ULC S636
(Standard for
Type BH Gas Venting Systems)
& ULC S635
(Standard for Lining Systems for Existing Masonry
or Factory-Built Chimneys and Vents)
By Underwriters Laboratories, Inc.
File MH 16161
p/n 834500
7-20-16
Summary of Contents for Polyflue BH
Page 16: ...16 NOTES ...