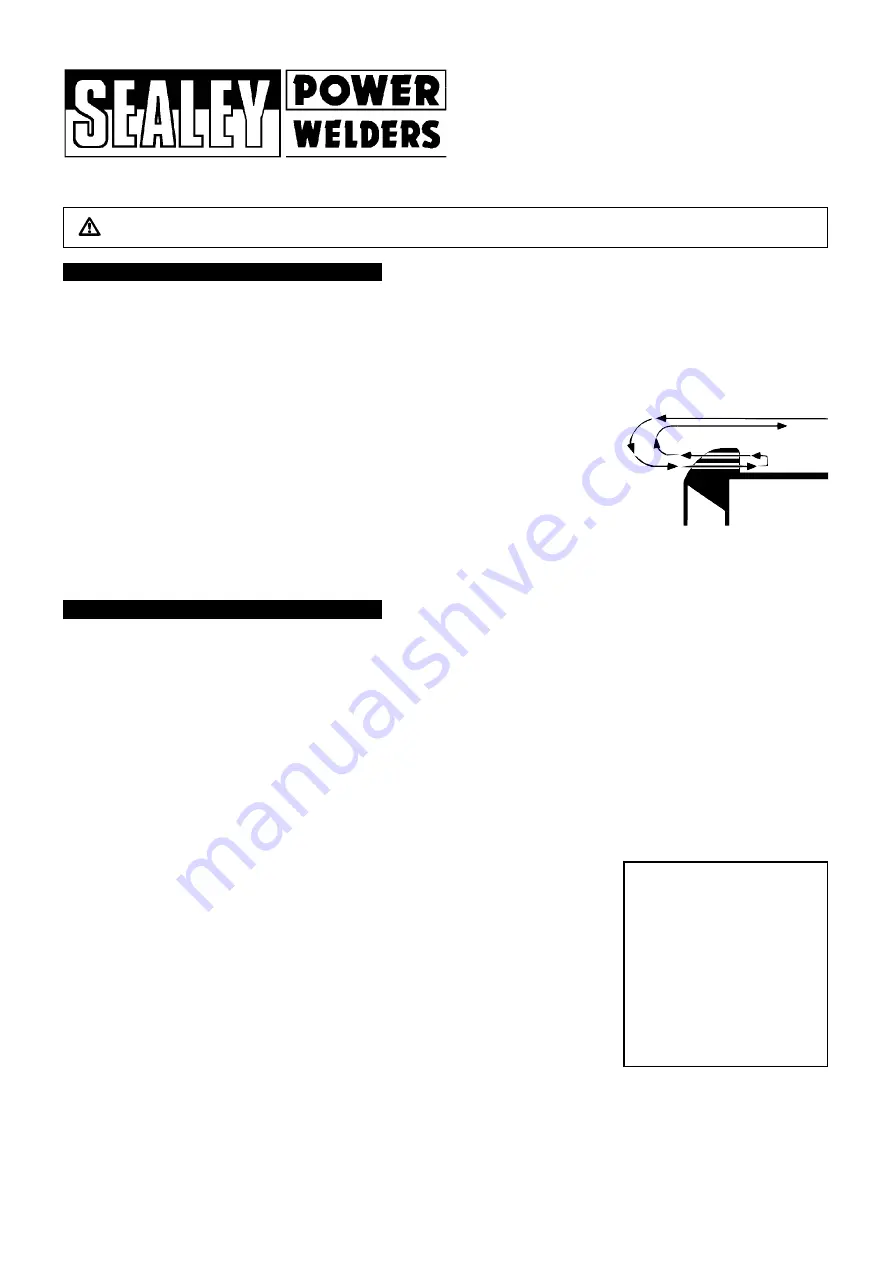
INSTRUCTIONS FOR:
P L A S M A C U T T E R
M
o d e l :
P P 4 0 .
Thank you for purchasing a Sealey
plasma cutter
. Manufactured to a high standard this product will, if used according to these instructions and properly maintained,
give you years of trouble free performance.
IMPORTANT
:
BEFORE USING THIS PRODUCT, PLEASE READ THE INSTRUCTIONS CAREFULLY. MAKE CAREFUL NOTE OF SAFETY INSTRUCTIONS,
WARNINGS AND CAUTIONS. THIS PRODUCT SHOULD ONLY BE USED FOR ITS INTENDED PURPOSE. FAILURE TO DO SO MAY CAUSE DAMAGE
OR PERSONAL INJURY, AND WILL INVALIDATE THE WARRANTY. RETAIN THESE INSTRUCTIONS FOR FUTURE USE.
2. SAFETY INSTRUCTIONS
MW100, MW140, MW165 - 0051 - (1) - 010399
2.1. ELECTRICAL SAFETY.
p
p
p
WARNING!
Electrical installation of the plasma cutting unit must only be carried out by a qualified
electrician. Make sure that power supply cable is correctly connected to Earth Plate. It is the users responsibility to read, understand
and comply with the following:
You must check all electrical equipment and appliances to ensure they are safe before using. You must inspect power supply leads, plugs and all
electrical connections for wear and damage. You must ensure the risk of electric shock is minimised by the installation of appropriate safety
devices. An RCCB (Residual Current Circuit Breaker) should be incorporated in the main distribution board. We also recommend that an RCD
(Residual Current Device) is used with all electrical products. It is particularly important to use an RCD together with portable products that are
plugged into an electrical supply not protected by an RCCB. If in doubt consult a professional electrician. You may obtain a Residual Current
Device by contacting your Sealey dealer.
You must
also read and understand the following instructions concerning electrical safety.
2.1.1. The
Electricity At Work Act 1989
requires all portable electrical appliances, if used on a business premises, to be tested by
a qualified Electrician at least once a year by using a Portable Appliance Tester (PAT).
2.1.2. The
Health & Safety at Work Act 1974
makes owners of electrical appliances responsible for the safe condition of the appliance,
and safety of the appliance operator.
If in any doubt about electrical safety, contact a qualified electrician.
2.1.3. Ensure the insulation on all cables and the product itself is safe before connecting to the mains power
supply. See 2.1.1. & 2.1.2. above and use a Portable Appliance Tester (PAT).
2.1.4. Ensure that cables are always protected against short circuit and overload.
2.1.5. Regularly inspect power supply, leads, plugs and all electrical connections for wear and damage,
especially power connections, to ensure that none are loose.
2.1.6.
Important:
Ensure the voltage marked on the product is the same as the electrical power supply
to be used, and check that plugs are fitted with the correct capacity fuse. A 13Amp plug may require
a fuse smaller than 13Amps for certain products (
subject to 2.1.11. below
)
see fuse rating at right.
2.1.7. DO NOT pull or carry the powered appliance by its power supply lead. Products such as
welders must not be pulled or carried by their output cables.
2.1.8. DO NOT pull power plugs from sockets by the power cable.
2.1.9. DO NOT use worn or damage leads, plugs or connections. Immediately replace or have repaired by
a qualified Electrician.
2.1.10. DO NOT use this product with a cable extension reel
.
2.1.11.
This product will require MORE than a 13Amp electrical supply, so no plug will be fitted. You must contact a qualified Electrician to
ensure a 30 Amp fused supply is available. We recommend you discuss the installation of a industrial round pin plug & socket with
your electrician.
FUSE RATING
TO GAIN MAXIMUM
OUTPUT THE PLASMA
CUTTER MUST BE
CONNECT TO A
30
Amp FUSED
ELECTRICAL SUPPLY
The PP40 is an inverter power supply fitted with a plasma cutter control circuitry. Features include a 4 LED
information panel including torch-under voltage, air fault, general fault (thermostat, over/under voltage, over
current) and power on. The plasma inverta is suitable for cutting steel, stainless, aluminium and brass. Unit
includes integrated air filter and regulator unit with panel mounted pressure gauge.
The plasma cutting system is operated by connecting the positive (+) clamp from the machine to the workpiece. The torch is positioned about 3mm
above the surface of metal area to be cut. When the torch trigger is depressed a very high temperature produces a combined electrical arc, and
fast flowing air to generate a plasma (
a very hot gas
) jet. The plasma transfers the electric arc to the metal workpiece which is melted by the heat
jet at the point of contact. The torch is moved along cutting line until work is complete, and the workpiece is cut or divided accordingly.
Duty cycle . . . . . . . . . . . . . . . . . . . .35% @ 40 A
Air requirements . . . . . . . . . . . . . . . . .120 ltr/min
Air pressure . . . . . . . . . . . . . . . . . . . . .55-70 psi
Power Efficiency . . . . . . . . . . . . . . . . . . .5.2 Kva
Mains Voltage . . . . . . . . . . . . . . . . . .230V - 1 ph
Insulation class . . . . . . . . . . . . . . . . . . . . . . . . .H
Electrical protection . . . . . . . . . . . . . . . . .Class 1
Weight . . . . . . . . . . . . . . . . . . . . . . . . . . . .14 Kg
INPUT
Absorbed current . . . . . . . . . . . . . . . 15.4A 32.5
Power factor . . . . . . . . . . . . .(cosphi) 0.65 - 0.72
Delayed fuses . . . . . . . . . . . . . . . . . . . . . . . .20A
OUTPUT
No load Voltage . . . . . . . . . . . . . . . . . . . . .370V
Rated cutting Voltage . . . . . . . . . . . . . . . .86-96V
Rated cutting current . . . . . . . . . . . . . . . .15-40A
PLASMA TORCH
Gas . . . . . . . . . . . . . . . . . . .DRY compressed air
Air pressure . . . . . . . . . . . . . . . . . . . . . .55-70psi
Cooling flow rate . . . . . . . . . . . . . . . . .120 lt/min
Striking system . . . . . . . . . . . . . .HF & Pilot Arc
cutting current . . . . . . . . . . . . . . . . . . .15 by 40A
Max cutting thickness . . . . . . . . . . . . . . . .12 mm
1. INTRODUCTION & SPECIFICATIONS
p
p
WARNING! Reminder, the electrical installation of the plasma cutting unit must only be carried out by a qualified electrician.
Make sure that power supply cable is correctly connected to Earth Plate.