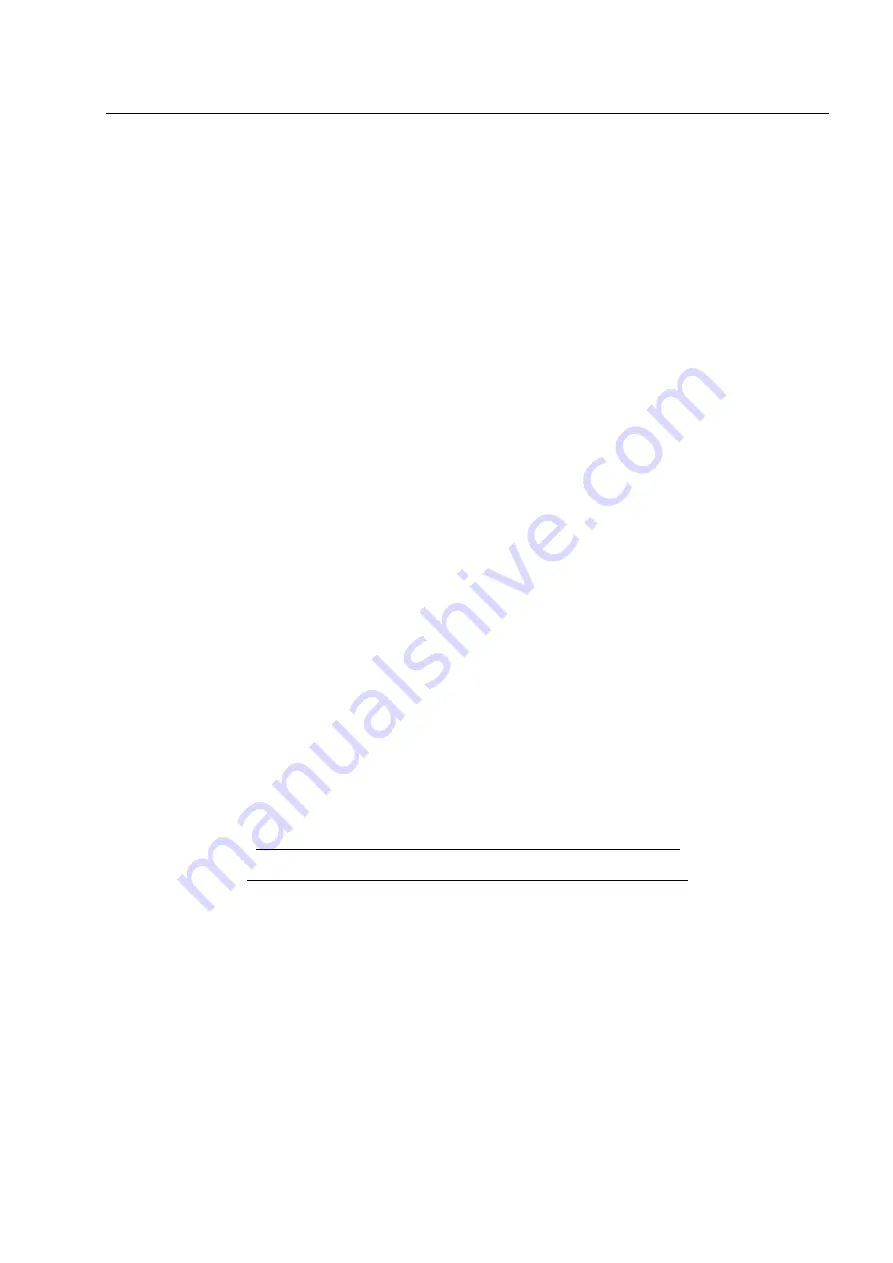
SCHEMPP-HIRTH FLUGZEUGBAU GmbH, KIRCHHEIM/TECK
P r e l i m i n a r y
F L I G H T M A N U A L
for Powered Sailplane
Variant:
V e n t u s – 3 M
Edition:
P e r f o r m a n c e
Serial-No.:
0 5 3 M P
Registr. No.:
O H – 1 0 3 1
Date of issue:
M a r c h
2 0 1 9
Pages as indicated by „appr.“ Are EASA approved by
„Type Certificate EASA.A.627“ vom 00. Monat 0000.
This powered sailplane is to be operated in compliance with information and limitations
contained herein.
Approval of translation has been done by best knowledge and judgement. In any case the
original text in German language is authorative.