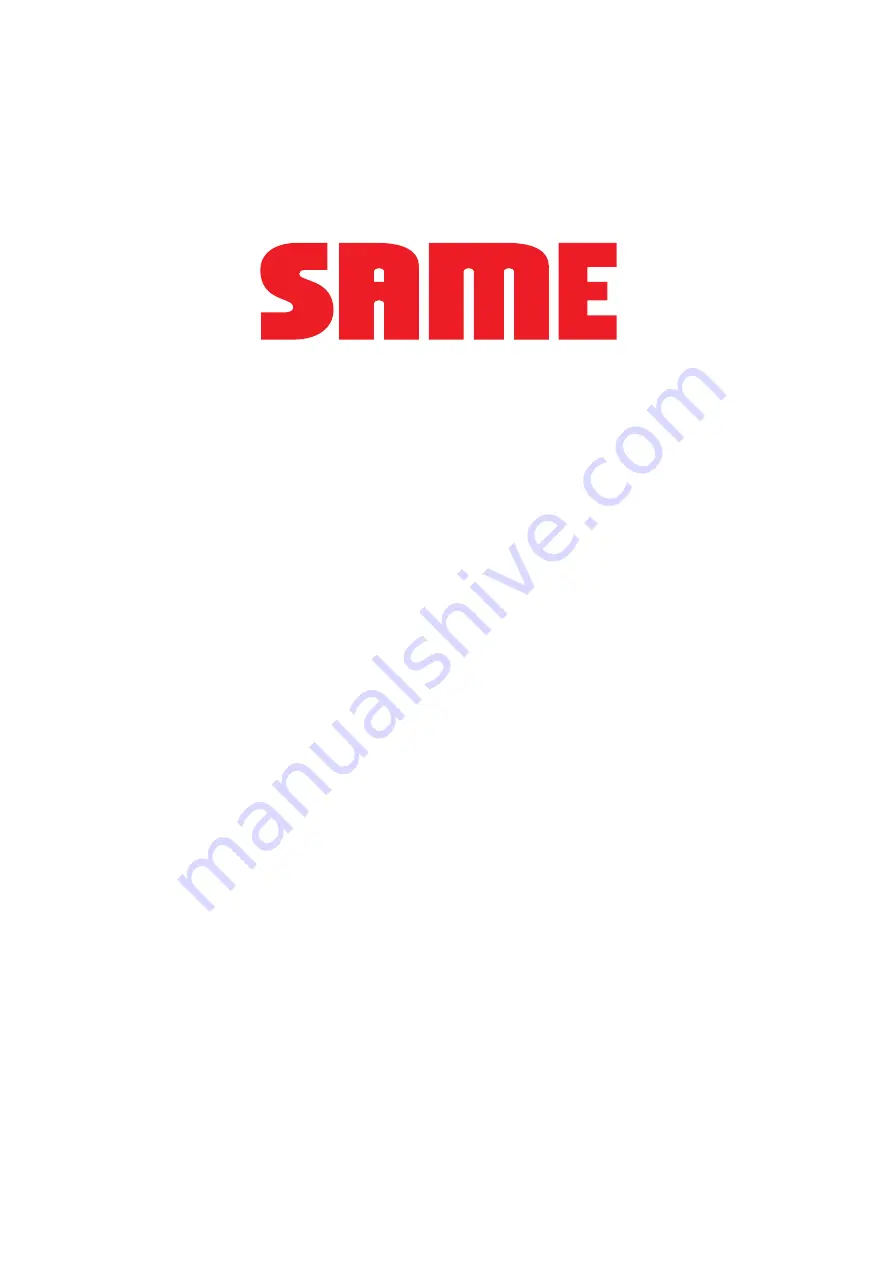
1
WORKSHOP MANUAL
Head offices:
V.le Ing. F. Cassani, 15
24047 Treviglio (BG)
Tel. 0363/4211
www.same-tractors.com
RUBIN 160
RUBIN 180
RUBIN 200
1
WORKSHOP MANUAL
Head offices:
V.le Ing. F. Cassani, 15
24047 Treviglio (BG)
Tel. 0363/4211
www.same-tractors.com
RUBIN 160
RUBIN 180
RUBIN 200