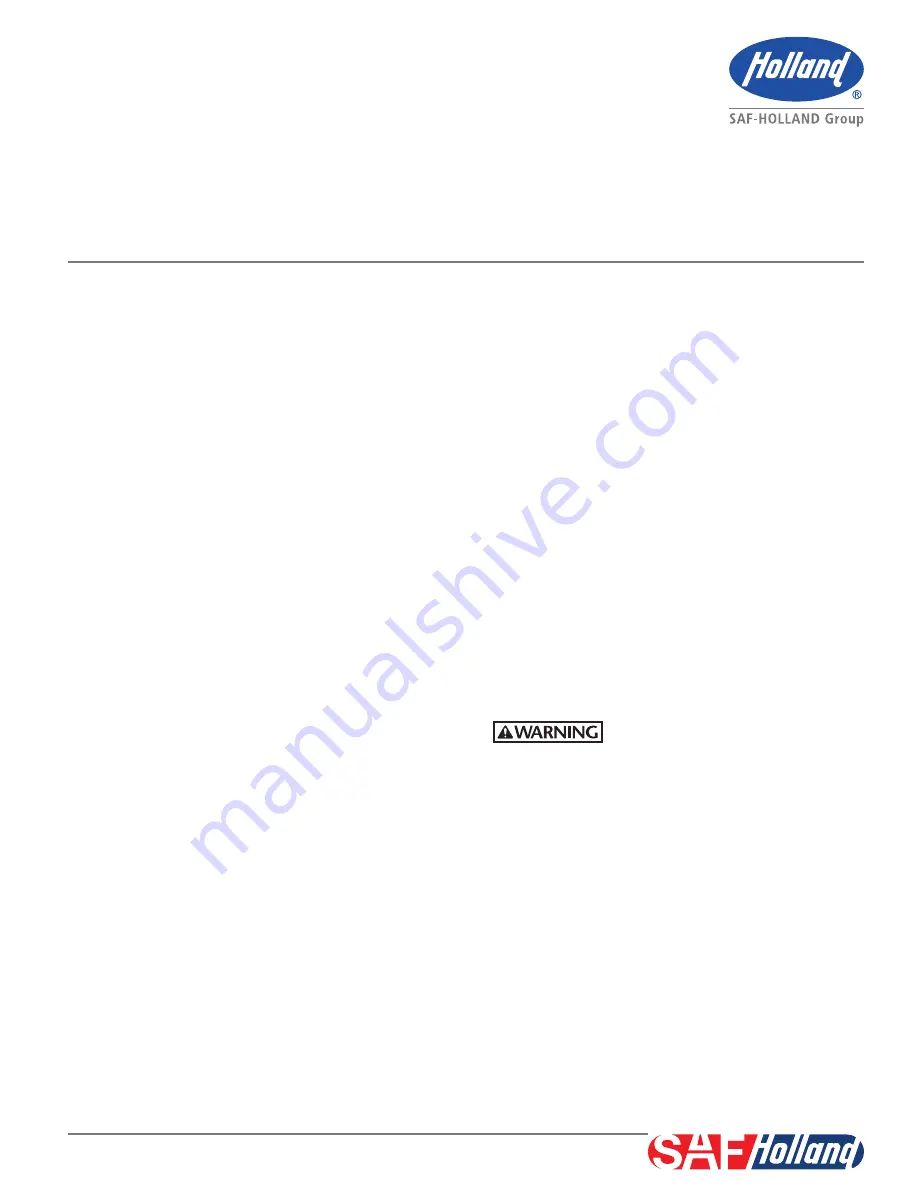
Drawbar Guides
Installation Instructions
For PH-200/210, PH-300/310 and PH400/410
Series Pintle Hook
XA-0255 (Right), XA-02556 (Left)
XL-PH353 Rev C · 2018-03-29 · Amendments and Errors Reserved · © SAF-HOLLAND, Inc., SAF-HOLLAND, HOLLAND, SAF, and logos are
trademarks of SAF-HOLLAND S.A., SAF-HOLLAND GmbH, and SAF-HOLLAND, Inc.
General Information
1. DO NOT modify or add to the product
2. Wear safety goggles during installation and removal.
3. NEVER strike any part of the item with a steel hammer.
4. DO NOT weld on this product, other than as directed
for installation.
This product is covered by HOLLAND’s Commercial Products
Warranty. HOLLAND reserves the right, without giving prior
notice, to change specifications and dimensions as designs
are altered or improved.
Mounting
1. Verify there is adequate clearance to install and inspect
the drawbar guides. Review drawing on reverse side.
2. The mounting structure must be of sufficient strength to
support the additional stresses and loads imparted on the
structure during the product operation.
3. Position drawbar guides as shown on reverse side.
Vertical position is taken from the bottom of the horn to
the bottom of the tube. Horizontal position is taken from
the centerline of the hook to the inside edge of the tube.
The Guides are now pre-welded at the proper angle. Weld
the tubes parallel and perpendicular to the mounting
surface. No need to angle guides at assembly. Guides
are also properly paced horizontally so the latch can be
replaced if needed without removal.
4. Remove a minimum of one (1) inch of paint from the
drawbar guide tube where it will be welded to the
vehicle. Install drawbar guides with a continuous 3/16"
(.19") Fillet weld. Refer to drawing on reverse side.
5. Verify the weld size and integrity before placing vehicle
in service.
When welding, use a procedure which
assures a sound, good quality weld which
protects the welding operator and others.
Over-welding may cause distortion and
damage. Under-welding may not develop
sufficient strength. A low hydrogen process
and AWS EX70XX filler metal are
recommended. Take precautions to ensure
that the vehicle electrical system is not
damaged by the welding.