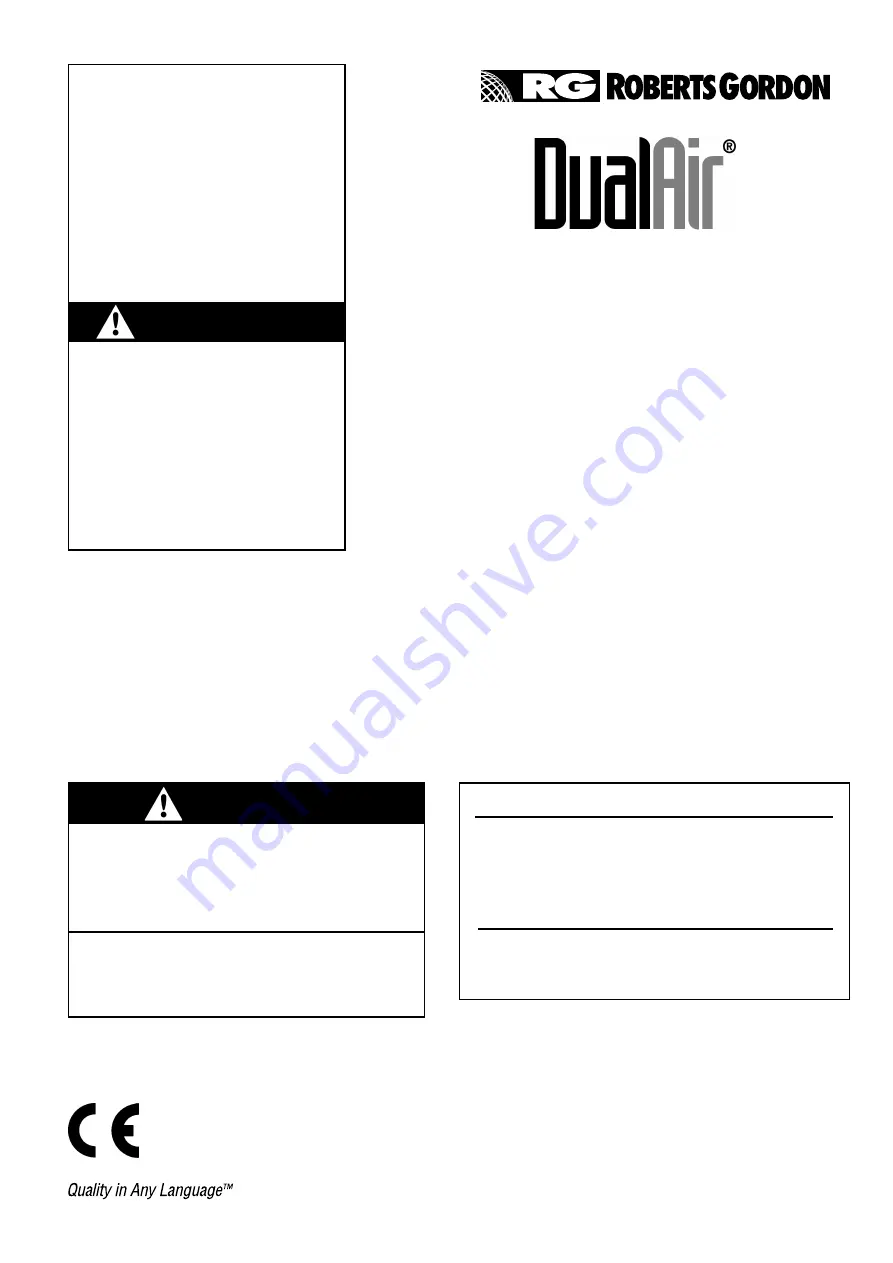
FOR YOUR SAFETY
If you smell gas:
1. Open windows.
2. DO NOT try to light any appliance.
3. DO NOT use electrical switches.
4. DO NOT use any telephone in
your building.
5. Leave the building.
6. Immediately call your local gas
supplier after leaving the building.
Follow the gas suppliers
instructions.
Do not store or use petrol or other
flammable vapours and liquids in the
vicinity of this or any other appli-
ance.
Failure to follow these instructions
can result in death, injury or property
damage.
WARNING
Improper installation, adjustment, alteration,
service or maintenance can result in death, injury
or property damage. Read the Installation,
operation and service manuals thoroughly before
installing or servicing this equipment
Installation must be done by a contractor qualified
in the installation and service of gas/oil fired
heating equipment (whichever is applicable).
Installer
Please take time to read and understand these
instructions prior to any installation. Installer must
give a copy of this manual to the user/owner.
Owner/User
Keep this manual in a safe place close to the heater
to provide your serviceman with information should it
become necessary.
Roberts-Gordon Europe Ltd.
Oxford Street
Bilston, West Midlands WV14 7EG UK
Telephone: +44 (0)1902 494425
Fax: +44 (0)1902 403200
email: [email protected]
www.combat.co.uk
www.rg-inc.com
V1
Heating & Cooling Unit
DA260G AND VARIANTS
DA300G AND VARIANTS
DA300L AND VARIANTS
DA325G AND VARIANTS
DA380G AND VARIANTS
DA380L AND VARIANTS
Installation, Commissioning,
Service & User Instructions
WARNING
Fire Hazard
X525D 02/03
© Copyright 2002 Roberts-Gordon
Summary of Contents for Dualair DA260G Series
Page 2: ...Details of condense drain for cooling coil ...
Page 9: ...Page 7 Fig 2 2 DualAir 380 Module Dimensions FRONT VIEW REAR VIEW SIDE VIEW ...
Page 34: ...Page 32 Fig 5 2 Wiring for DualAir Units On Off Burner 24v Controls ...
Page 35: ...Page 33 Fig 5 3 Wiring for DualAir Units Hi Low Burner 230v Controls ...
Page 36: ...Page 34 Fig 5 4 Wiring for DualAir Units Hi Low Burner 24v Controls ...
Page 37: ...Page 35 Fig 5 6 Wiring for DualAir Units BMS Burner Modulation 230v Controls ...
Page 38: ...Page 36 Fig 5 7 Wiring for DualAir Units BMS Burner Modulation 24v Controls ...
Page 39: ...Page 37 Fig 5 7 Wiring for DualAir Units Full Burner Modulation 230v Controls ...
Page 40: ...Page 38 Fig 5 8 Wiring for DualAir Units Full Burner Modulation 24v Controls ...
Page 41: ......
Page 42: ......
Page 43: ......
Page 44: ......
Page 45: ......
Page 46: ......
Page 47: ......
Page 48: ......
Page 49: ......
Page 50: ......