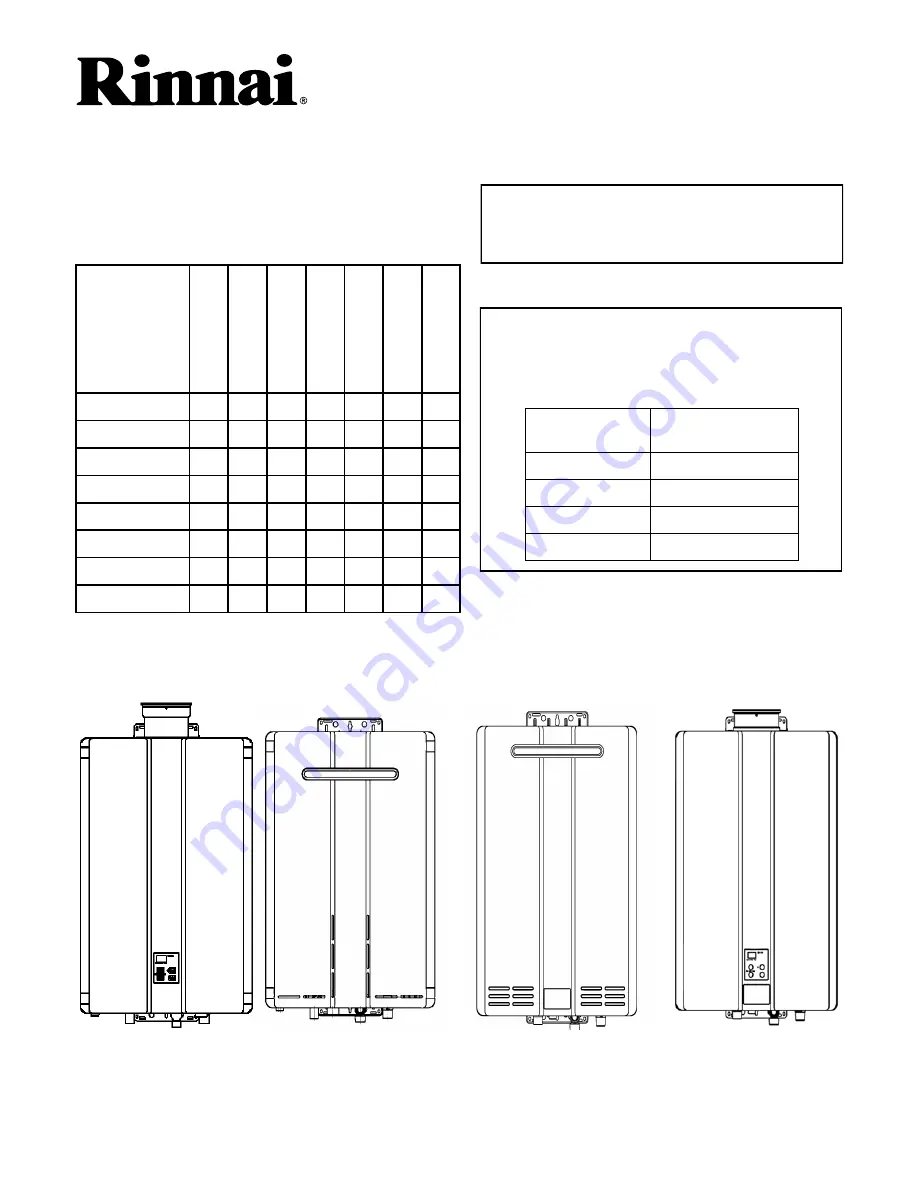
Key to Trade Names in this Manual:
RC & RU
-
Indicates condensing water heater
models.
Model with
valves in carton
Equivalent Model
RC80e
RC80HPe
RC80i
RC80HPi
RC98e
RC98HPe
RC98i
RC98HPi
Some of the trade names for models were changed
to indicate that their cartons included isolation valves
and a pressure relief valve. For service and repair
purposes the table below shows the equivalent
models.
RC80HPe
9
15
20
22
25
28
31
RC80HPi
9
15
20
22
25
28
34
RC98HPe
11
16
20
22
25
28
37
RC98HPi
11
16
20
22
25
28
40
RU80e
13
17
21
23
27
29
43
RU80i
13
17
21
23
27
29
43
RU98e
13
17
21
23
27
29
43
RU98i
13
17
21
23
27
29
43
DI
A
G
NO
S
T
ICS
W
IRE
DI
A
G
R
A
M
G
A
S
CO
NT
RO
L
F
A
N
P
C BO
A
RD
W
A
T
E
R F
L
O
W
CO
NT
RO
L
HE
A
T
E
X
C
H
A
NG
E
R
M
O
DE
L
S
This manual provides service information for the models
below. This table cross references each model to the
applicable page number for internal component
replacement instructions.
Condensing Tankless Water Heater Service Manual
KA Condensing
KB Condensing
100000354
Summary of Contents for Circ-Logic RU80e
Page 16: ...Condensing Water Heater Service Manual 16 100000354 KA Series Wiring Diagram RC80HPe RC80HPi ...
Page 17: ...Condensing Water Heater Service Manual 17 100000354 KA Series Wiring Diagram RC98HPe RC98HPi ...
Page 18: ...Condensing Water Heater Service Manual 18 100000354 KB Series Wiring Diagram RU80i e RU98i e ...
Page 57: ...Condensing Water Heater Service Manual 57 100000354 Notes ...
Page 58: ...Condensing Water Heater Service Manual 58 100000354 Notes ...
Page 59: ...Condensing Water Heater Service Manual 59 100000354 Notes ...