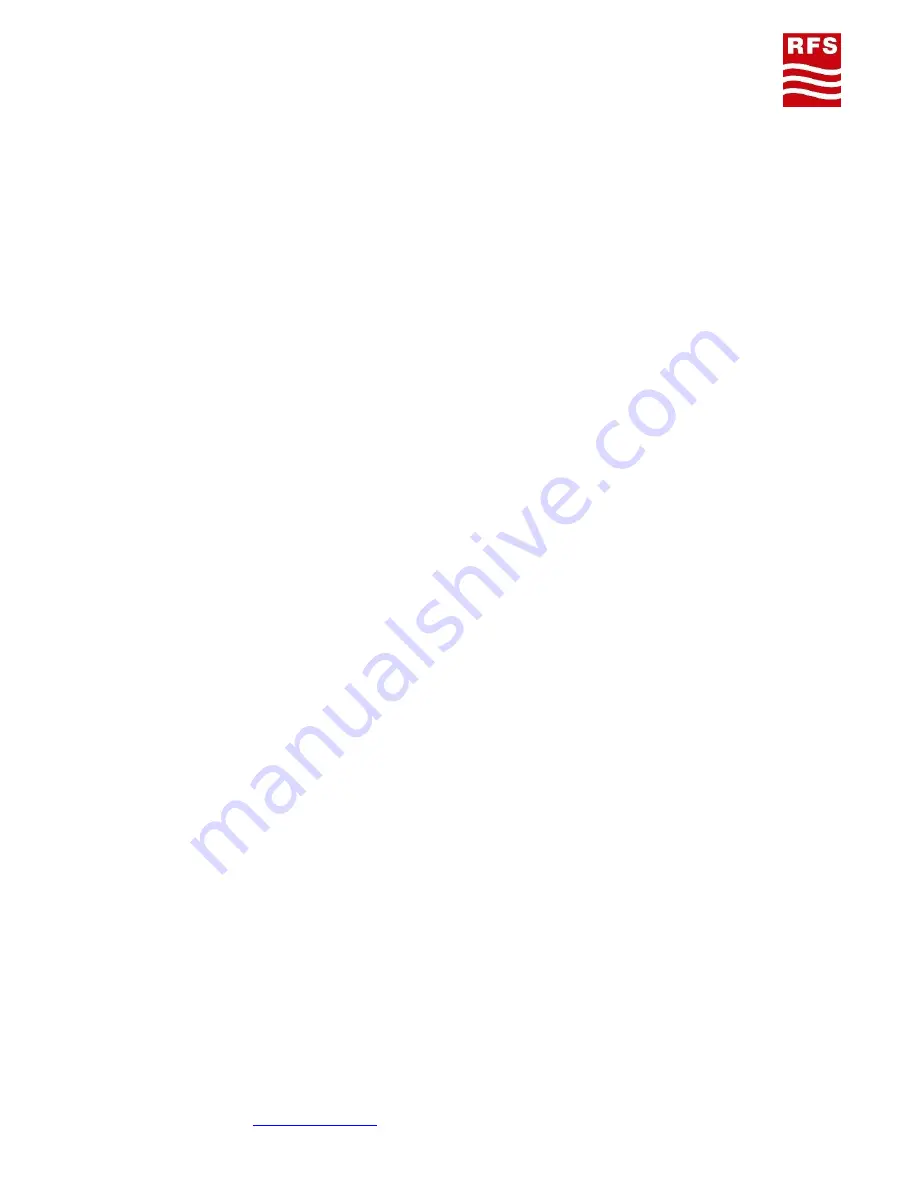
RFS INSTALLATION GUIDELINES
HYBRIFLEX
®
CABLE|603400210500|September 2020
Visit
for the most current product specifications
Page 1 of 43
Direct Connection RRH HYBRIFLEX
®
Guidelines and Instructions
RFS INSTALLATION GUIDELINES
HYBRIFLEX
®
CABLE|603400210500|September 2020
Visit
for the most current product specifications
Page 1 of 43
Direct Connection RRH HYBRIFLEX
®
Guidelines and Instructions