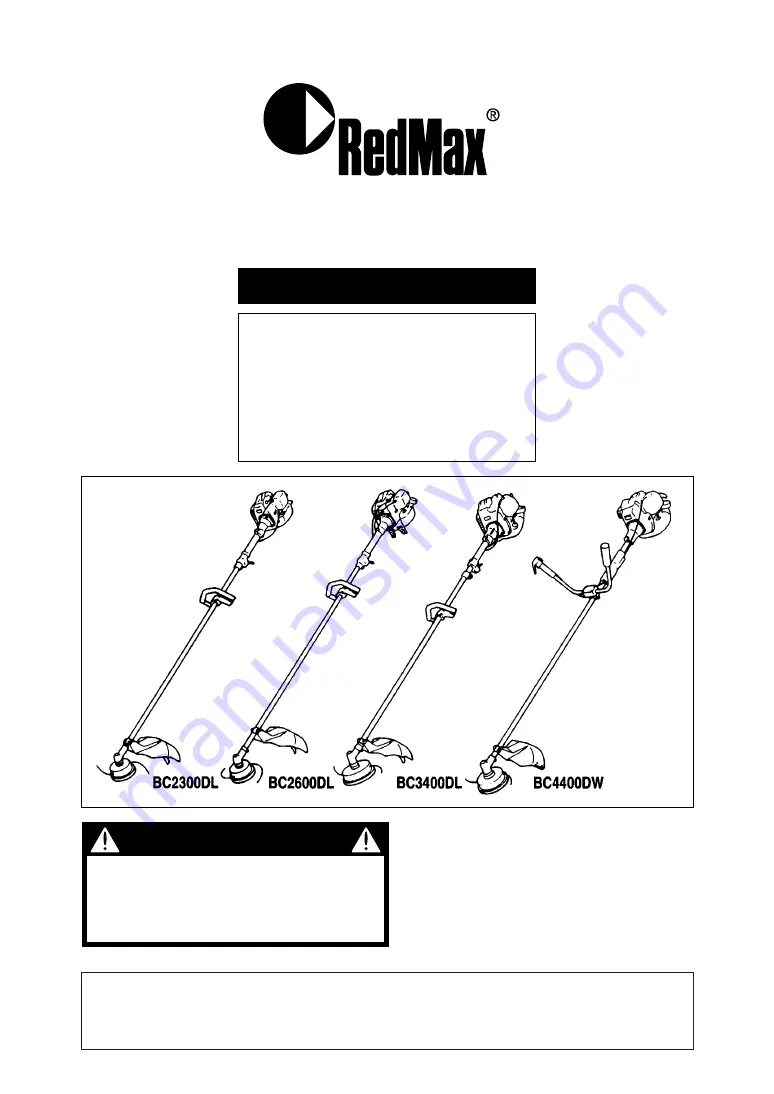
The engine exhaust from this product
contains chemicals known to the State
of California to cause cancer, birth
defects or other reproductive harm.
WARNING
OWNER / OPERATOR MANUAL
BRUSHCUTTERS
T1006-93110(010)
BC2300DL
BC2600DL
BC3400DL
BC4400DW
Thank you for purchasing a RedMax
product.
Before using our brushcutters, please
read this manual carefully to understand
the proper use of your unit.
BC2300DL
DRIVE UNIT 500000000 and up
ENGINE UNIT 990639 and up
BC2600DL
DRIVE UNIT 500000000 and up
ENGINE UNIT 978729 and up
BC3400DL
DRIVE UNIT 980101 and up
ENGINE UNIT 980101 and up
BC4400DW
DRIVE UNIT 980101 and up
ENGINE UNIT 980101 and up
APPLICABLE SERIAL NUMBERS :
Summary of Contents for BC2300DL
Page 26: ...Parts List 26 Fig 1 DRIVE UNIT BC2300DL BC2600DL ...
Page 28: ...Fig 2 ENGINE UNIT BC2300DL 28 Parts List ...
Page 30: ...Fig 3 ENGINE UNIT BC2600DL 30 Parts List ...
Page 32: ...Parts List 32 Fig 4 DRIVE UNIT BC3400DL S N 980101 and up ...
Page 34: ...Fig 5 ENGINE UNIT BC3400DL S N 980101 and up 34 Parts List ...
Page 36: ...Parts List 36 Fig 6 DRIVE UNIT BC4400DW S N 980101 and up ...
Page 38: ...Fig 7 ENGINE UNIT BC4400DW S N 980101 and up 38 Parts List ...