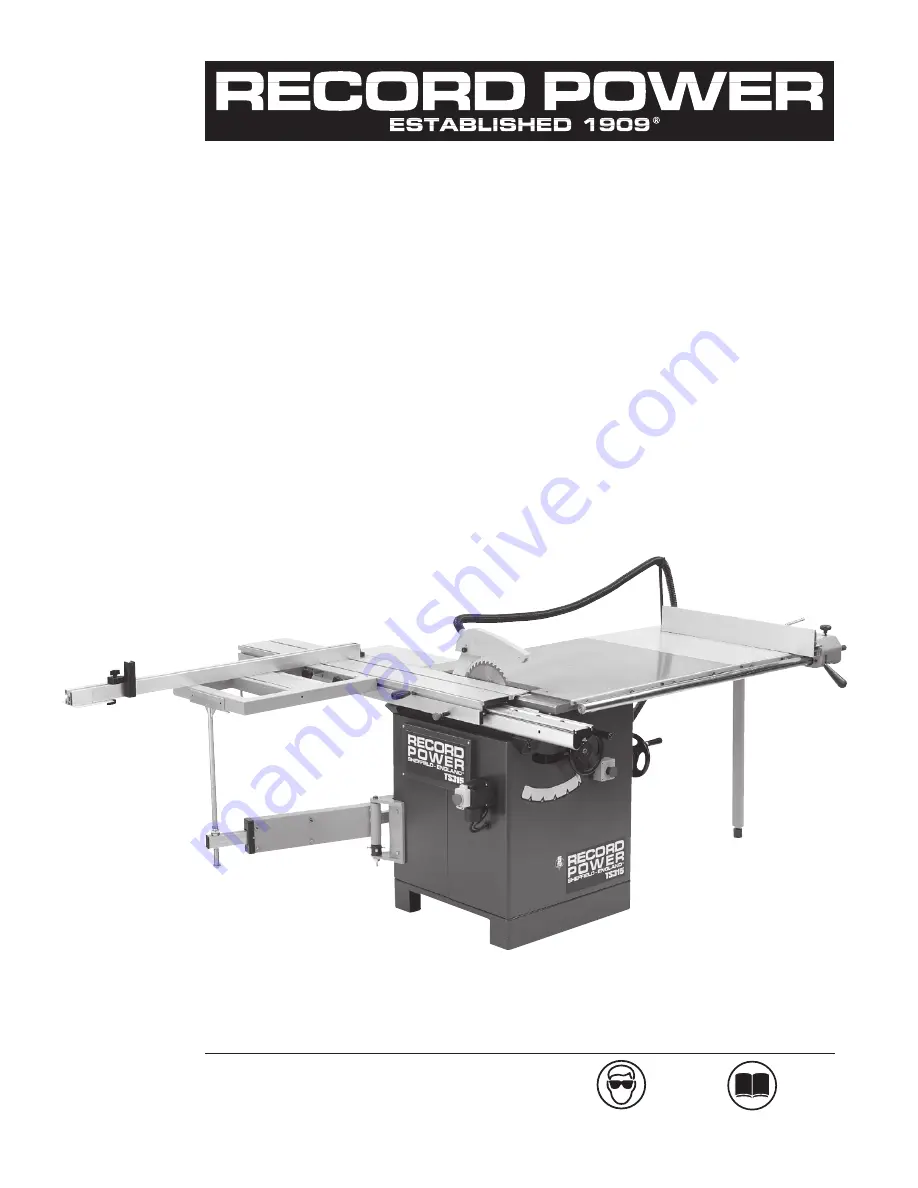
Original Instruction Manual
Version 2.1
February 2010
Woodworking Machines & Accessories
Telephone: 01246 561 520
Fax: 01246 561 537
Record Power Ltd
Unit B, Adelphi Way
Staveley S43 3LS
Email: [email protected]
www.recordpower.co.uk
TS315
Cast Iron Table
Saw with Scoring
IMPORTANT
For your safety read instructions
carefully before assembling or using
this product. Save this manual for
future reference.
HEALTH AND SAFETY GUIDELINES
Always follow the instructions provided with the manual. Always wear safety glasses when using woodworking
equipment. Always disconnect the power before adjusting any equipment. Failure to observe proper safety
procedures and guidelines can result in serious injury.
WARNING:
Do not allow familiarity (gained from frequent use of your machine and accessories) to become
commonplace. Always remember that a careless fraction of a second is sufficient to inflict severe injury.
Always wear safety glasses when
using woodworking equipment.
Always read the instructions
provided before using
woodworking equipment.
Summary of Contents for TS315
Page 31: ...30 31 ...