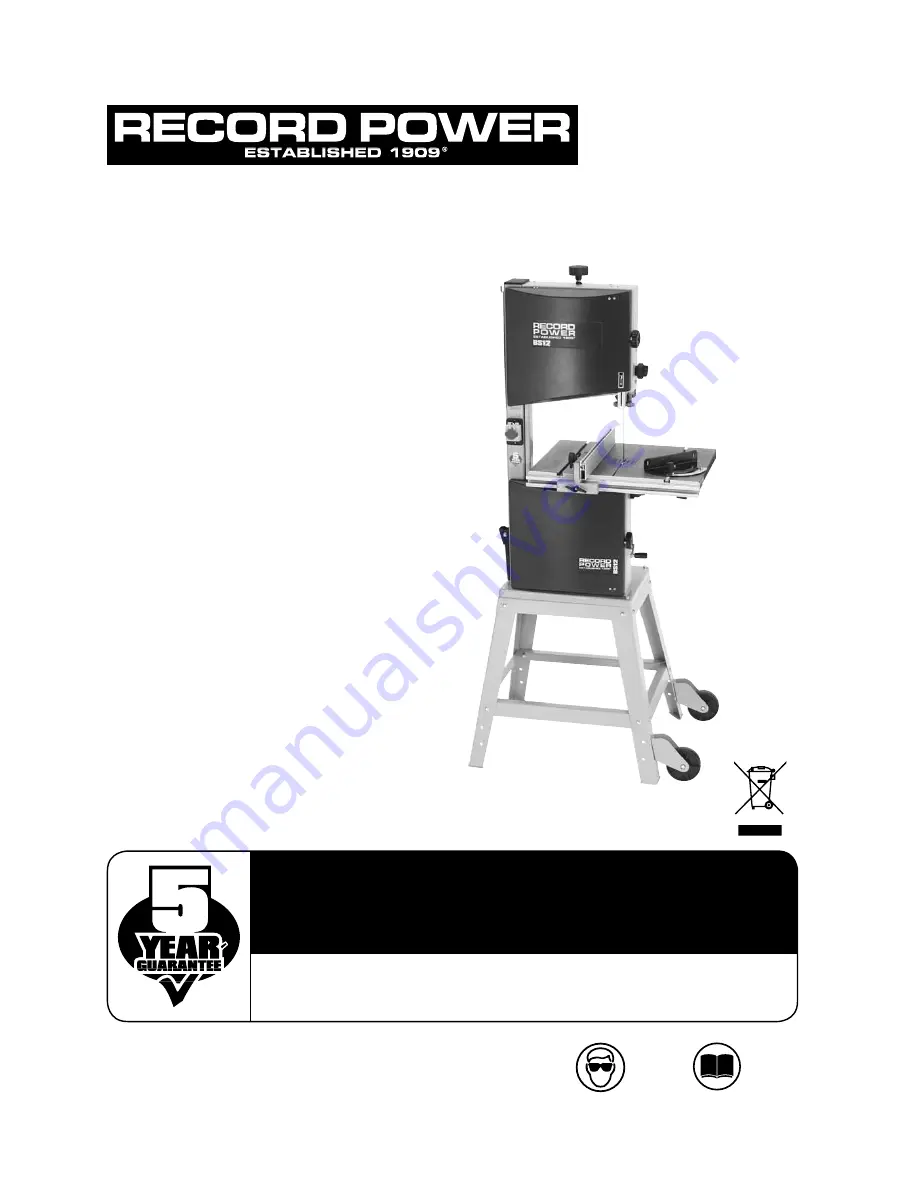
Tel: 01246 561 520 | www.recordpower.co.uk
Original Instruction Manual
IMPORTANT
For your safety read
instructions carefully
before assembling or
using this product.
Save this manual for
future reference.
Version 2.0
February 2012
Telephone: 01246 561 520
Fax: 01246 561 537
Record Power Ltd
Unit B, Adelphi Way
Staveley S43 3LS
Email: [email protected]
www.recordpower.co.uk
HEALTH AND SAFETY GUIDELINES
Always follow the instructions provided with the manual. Always wear safety glasses when using
woodworking equipment. Always disconnect the power before adjusting any equipment. Failure to
observe proper safety procedures and guidelines can result in serious injury.
WARNING:
Do not allow familiarity (gained from frequent use of your machine and accessories) to
become commonplace. Always remember that a careless fraction of a second is sufficient to inflict
severe injury.
Always wear safety
glasses when using
woodworking equipment.
Always read the instructions
provided before using
woodworking equipment.
Please register this product by logging in at
www.recordpower.co.uk
or calling
Record Power on
01246 561 520
It is important to register your product as soon as possible in order to receive
efficient after sales support and be entitled to the full
5 year guarantee
.
Your statutory rights are not affected.
BS12
12" Bandsaw