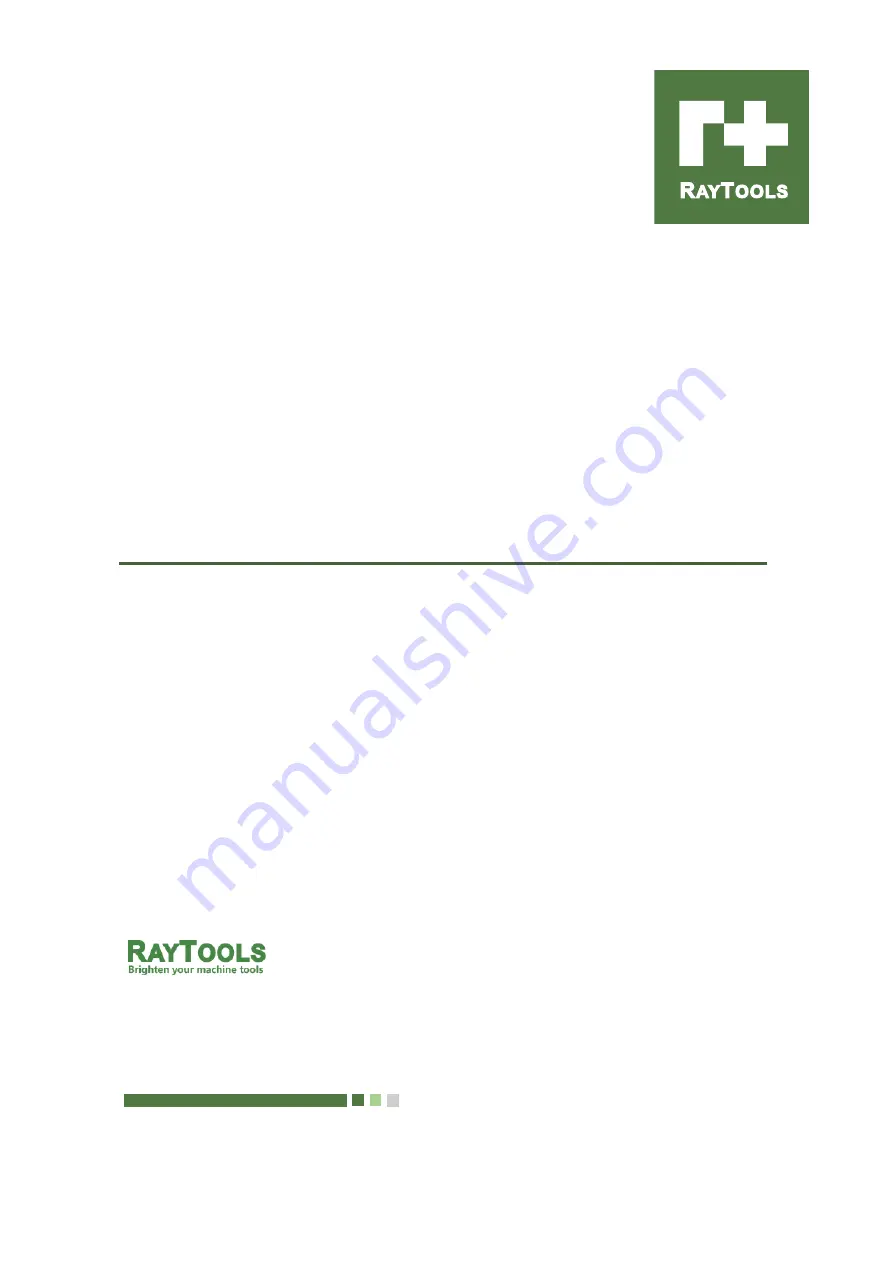
BM114S SERIES
6KW Auto-Focusing Laser Cutting Head- User Manual
Email: [email protected]
Add:
EMMENTALSTRASSE 96 CH-3414 OBERBURG, SWITZERLAND
BM114S SERIES
6KW Auto-Focusing Laser Cutting Head- User Manual
Email: [email protected]
Add:
EMMENTALSTRASSE 96 CH-3414 OBERBURG, SWITZERLAND