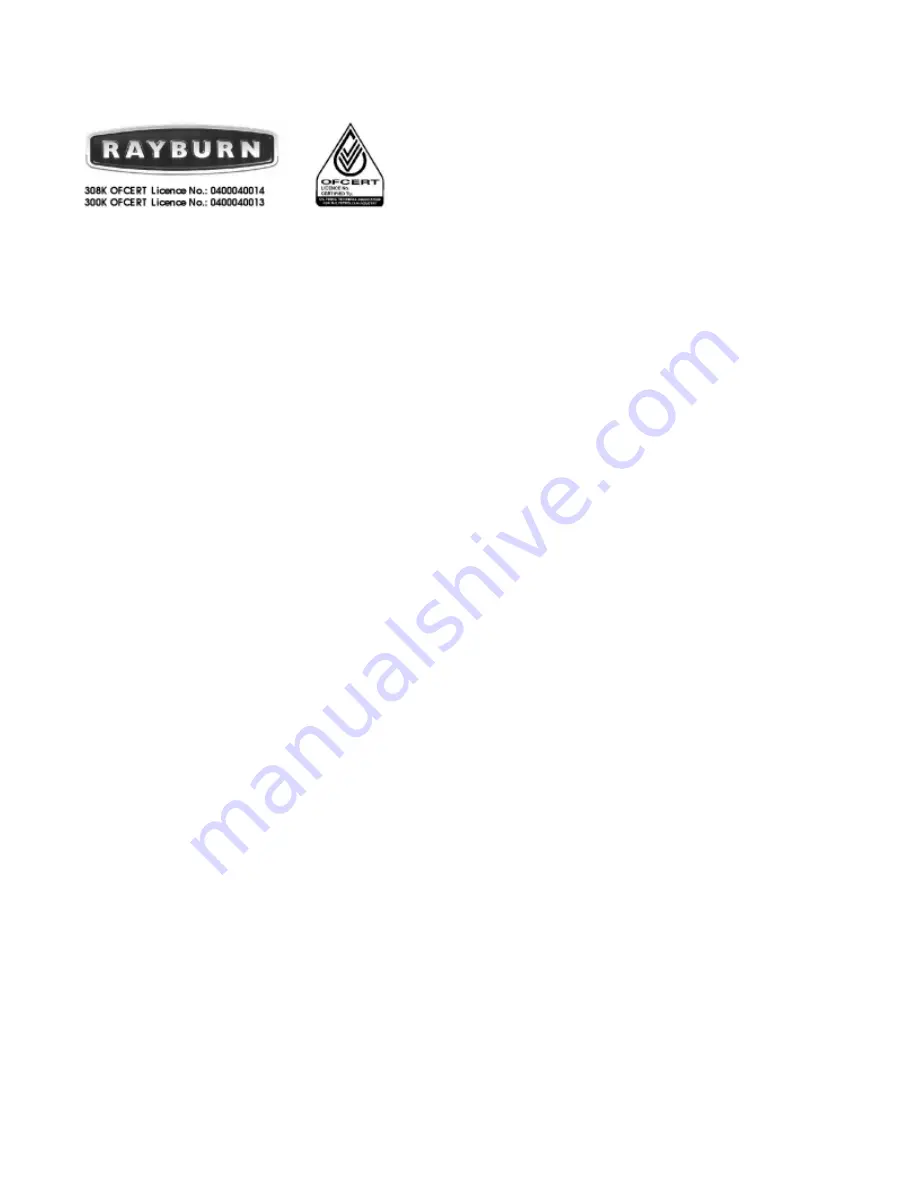
10/05 EINS 511985
Better than you ever imagined
Installation & Servicing Instructions
for Rayburn Cookmaster 300K and
Rayburn Cookmaster Plus 308K
Oil-Fired Cooker
Consumer Protection Act 1987
As responsible manufacturers we take care to make sure that our products are designed and constructed to meet
the required safety standards when properly installed and used.
IMPORTANT NOTICE:
Any alteration that is not approved by Aga-Rayburn, could invalidate the approval of the
appliance, operation of the warranty and could also affect your statutory rights.
Control of Substances - Health and Safety Important
This appliance may contain some of the materials that are indicated. It is the Users/Installers responsibility to
ensure that the necessary personal protective clothing is worn whenhandling, where applicable, the pertinent
parts that contain any of the listed materials that could be interpreted as being injurious to health and safety, see
below for information.
Firebricks, Fuel beds, Artificial Fuels -
when handling use disposable gloves.
Fire Cement -
when handling use disposable gloves.
Glues and Sealants -
exercise caution - if these are still in liquid form use face mask and disposable gloves.
Glass Yarn, Mineral Wool, Insulation Pads, Ceramic Fibre, Kerosene/Gas Oil -
may be harmful if inhaled,
may be irritating to skin, eyes, nose and throat. When handling avoid inhaling and contact with skin or eyes. Use
disposable gloves, face-masks and eye protection. After handling wash hands and other exposed parts. When
disposing of the product, reduce dust with water spray, ensure that parts are securely wrapped.
INTRODUCTION
The Rayburn Cookmaster Plus 308K is a cooker providing domestic hot water and cooking facilities. It is available
with a vertical flue and outlet only, with the oil burner operating on natural draught.
The boiler is designed for use in an open vented water system only, with gravity D.H.W. primaries.
Page 1 of 23
EINS 511985
26/10/2006
file://\\server1\docs\NetCDs\Aga%20Product%20Information%20Spares%20and%20Tec...