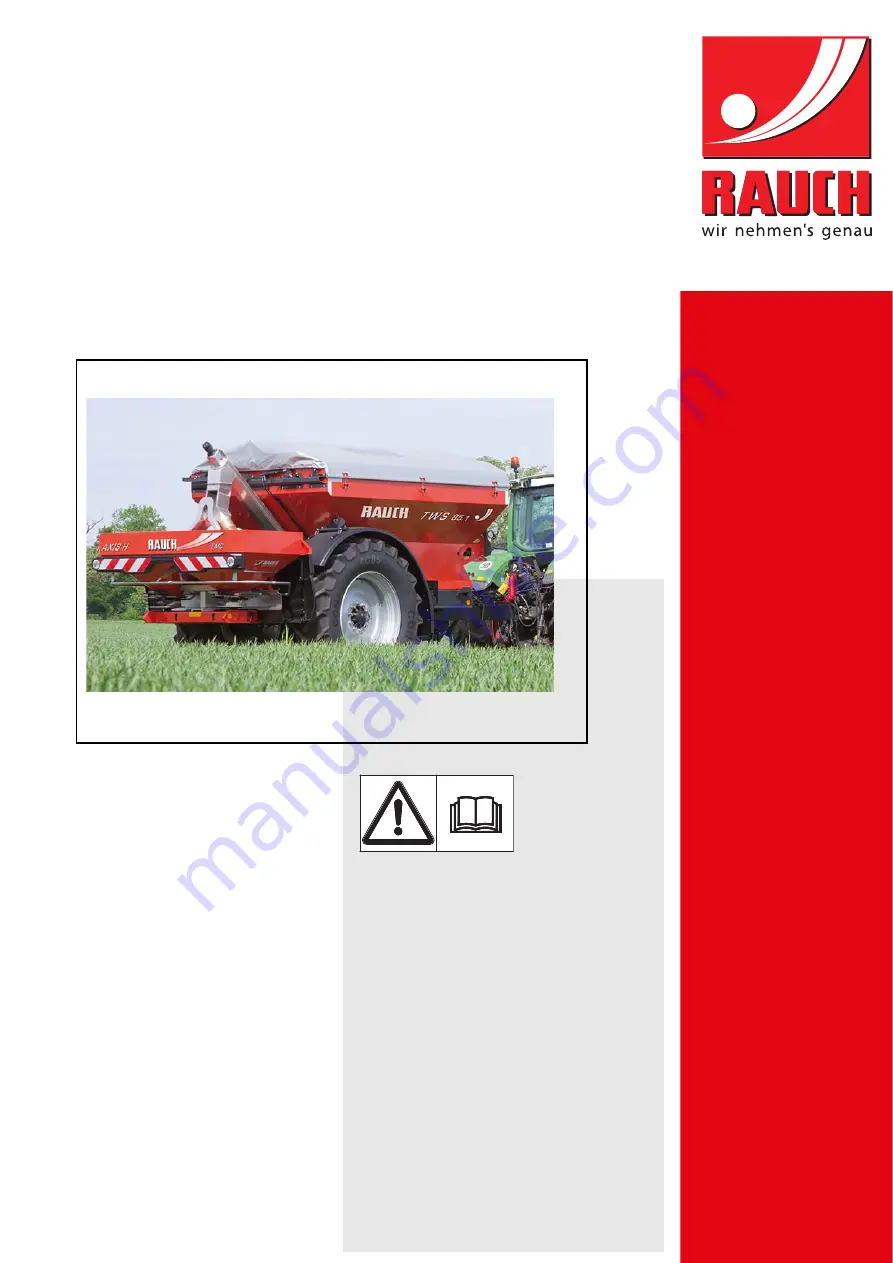
INSTRUCTION MANUAL
TWS
85.1
Please read carefully
before using the ma-
chine.
Keep for future reference.
This instruction manual/assembly in-
struction is to be considered as part of
the machine. Suppliers of new and sec-
ond-hand machines are required to
document in writing that the instruc-
tion manual/assembly instruction was
delivered with the machine and hand-
ed over to the customer.
Original instructions
5901746-
a
-en-1015
Summary of Contents for TWS 85.1
Page 30: ...Safety 3 24...
Page 38: ...Transportation without tractor 5 32...
Page 76: ...Instructions for load transfer 7 70...
Page 78: ...Faults and possible causes 8 72...
Page 104: ......