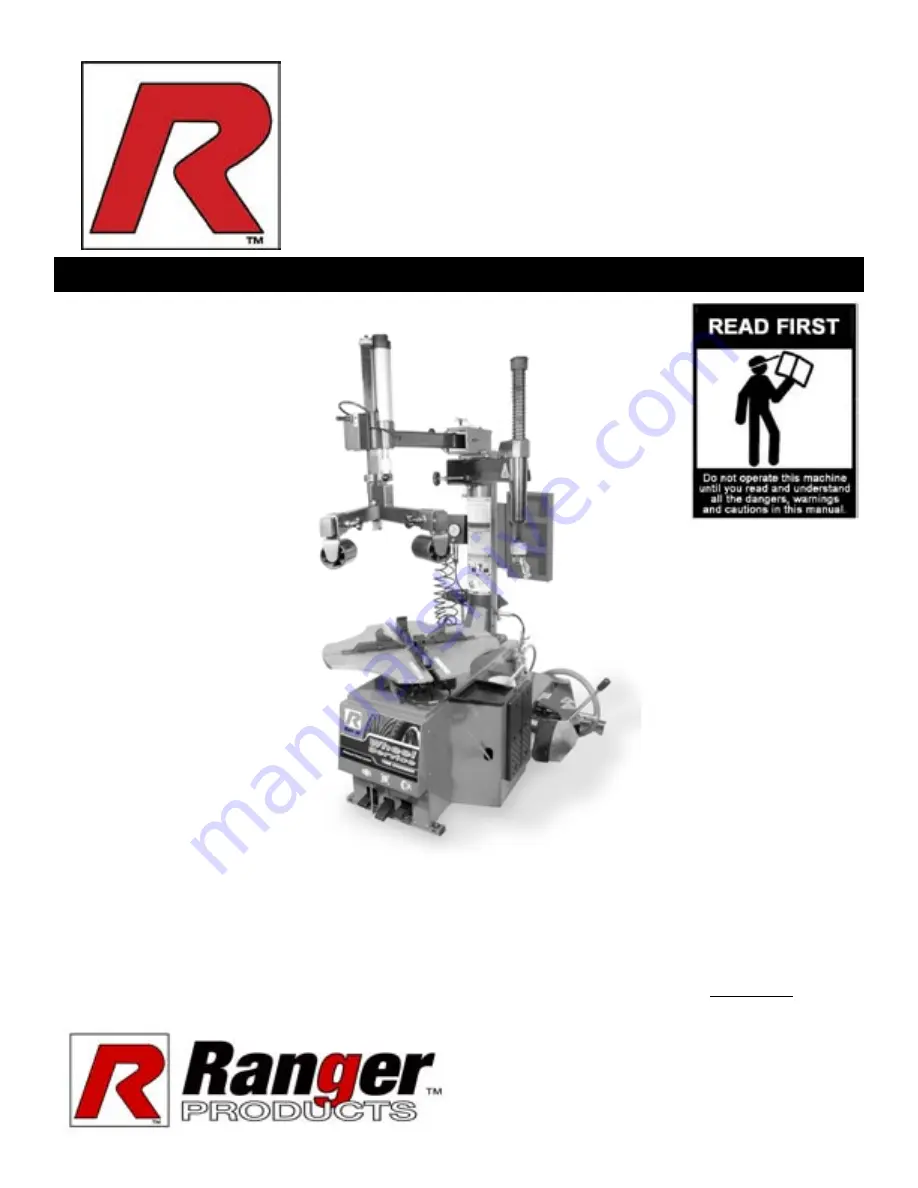
1
INSTALLATION AND OPERATION MANUAL
RECEIVING
The shipment should be thoroughly inspected as soon as it
is received. The signed Bill of Lading is acknowledgement
by the shipping carrier as receipt of this product as listed
in your invoice as being in a good condition of shipment. If
any of these goods listed on this Bill of Lading are missing
or damaged, do not accept goods until the shipping carrier
makes a notation on the freight bill of the missing or dam-
aged goods. Do this for your own protection.
BE SAFE
Your new tire changer was designed and built with safety
in mind. However, your overall safety can be increased with
proper training and thoughtful operation on the part of the
operator. DO NOT operate or repair this equipment without
reading this manual and the important safety instructions
shown inside. Keep this operation manual near the tire
changer at all times. Make sure that ALL USERS read and
understand this manual.
1645 Lemonwood Dr.
Santa Paula, CA. 93060, USA
Toll Free 1-800-253-2363
Tel: 1-805-933-9970
Fax: 1-805-933-9160
www.bendpak.com
IMPORTANT SAFETY INSTRUCTIONS
SAVE THESE INSTRUCTIONS
PLEASE READ THE ENTIRE CONTENTS OF THIS MANUAL PRIOR TO
INSTALLATION AND OPERATION. BY PROCEEDING WITH TIRE CHANGER
INSTALLATION AND OPERATION YOU AGREE THAT YOU FULLY
UNDERSTAND AND COMPREHEND THE FULL CONTENTS OF THIS MANUAL.
FORWARD THIS MANUAL TO ALL OPERATORS. FAILURE TO OPER-
ATE THIS EqUIPMENT AS DIRECTED MAY CAUSE INjURY OR DEATH.
MAN REV B 04-20-11
P/N 5900380
AUTOMOBIlE AND lIGHT TRUCK
SINGlE PIECE WHEEl
TIRE CHANGER
MODEl:
R30XlT
Summary of Contents for R30XLT
Page 34: ...34 ...
Page 38: ...38 ...
Page 43: ...43 ...
Page 45: ...45 ...
Page 46: ...46 RECORD ALL MAINTENANCE NOTES AND SERVICE HISTORY HERE ...
Page 47: ...47 TIRE AND WHEEL DATA ...