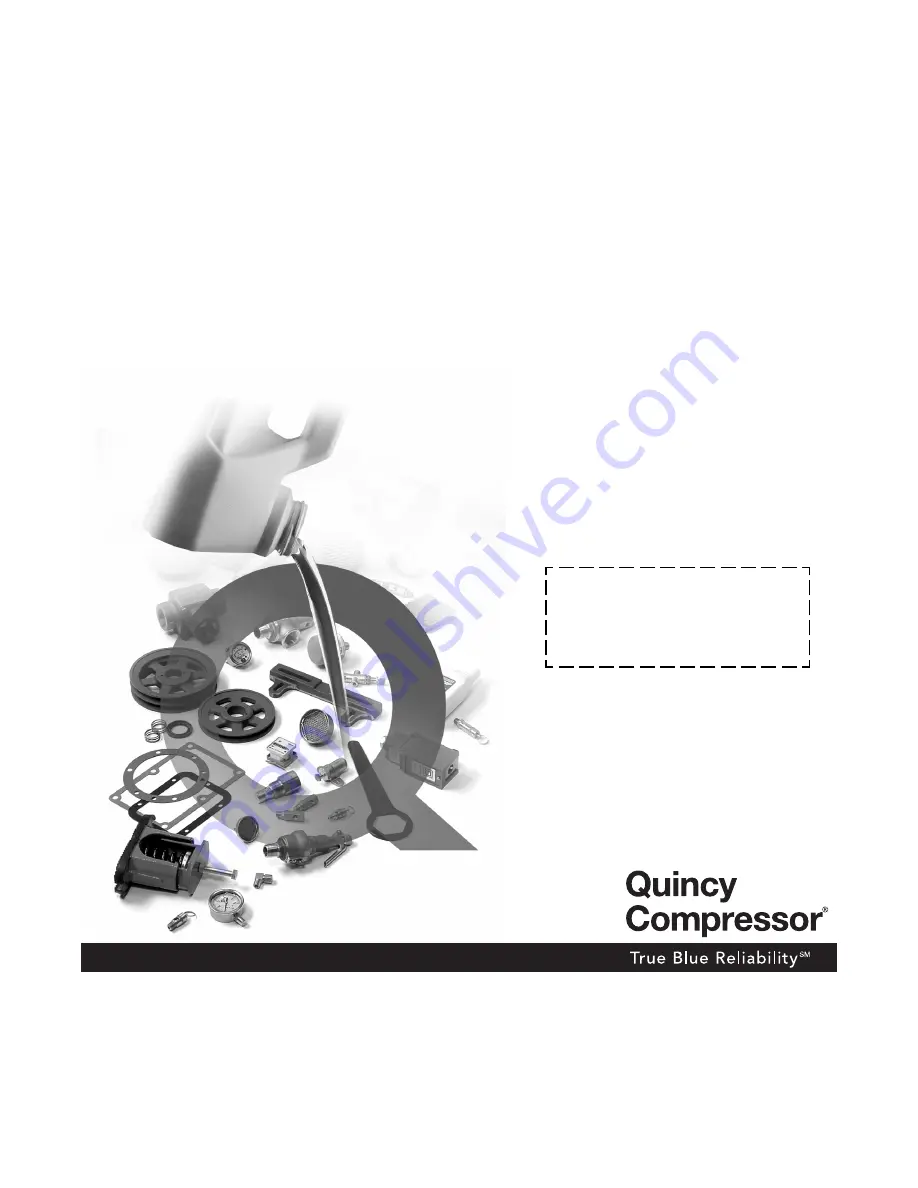
T r u e B l u e R e l i a b i l i t y
TM
This manual contains important safety
information and should be made available
to all personnel who operate and/or
maintain this product. Carefully read this
manual before attempting to operate or
perform maintenance on this compressor.
Manual No. 52201-105
May 2003 Edition
Quincy QR-25
®
Series
Instruction Manual
Summary of Contents for QR-25 Series
Page 42: ......