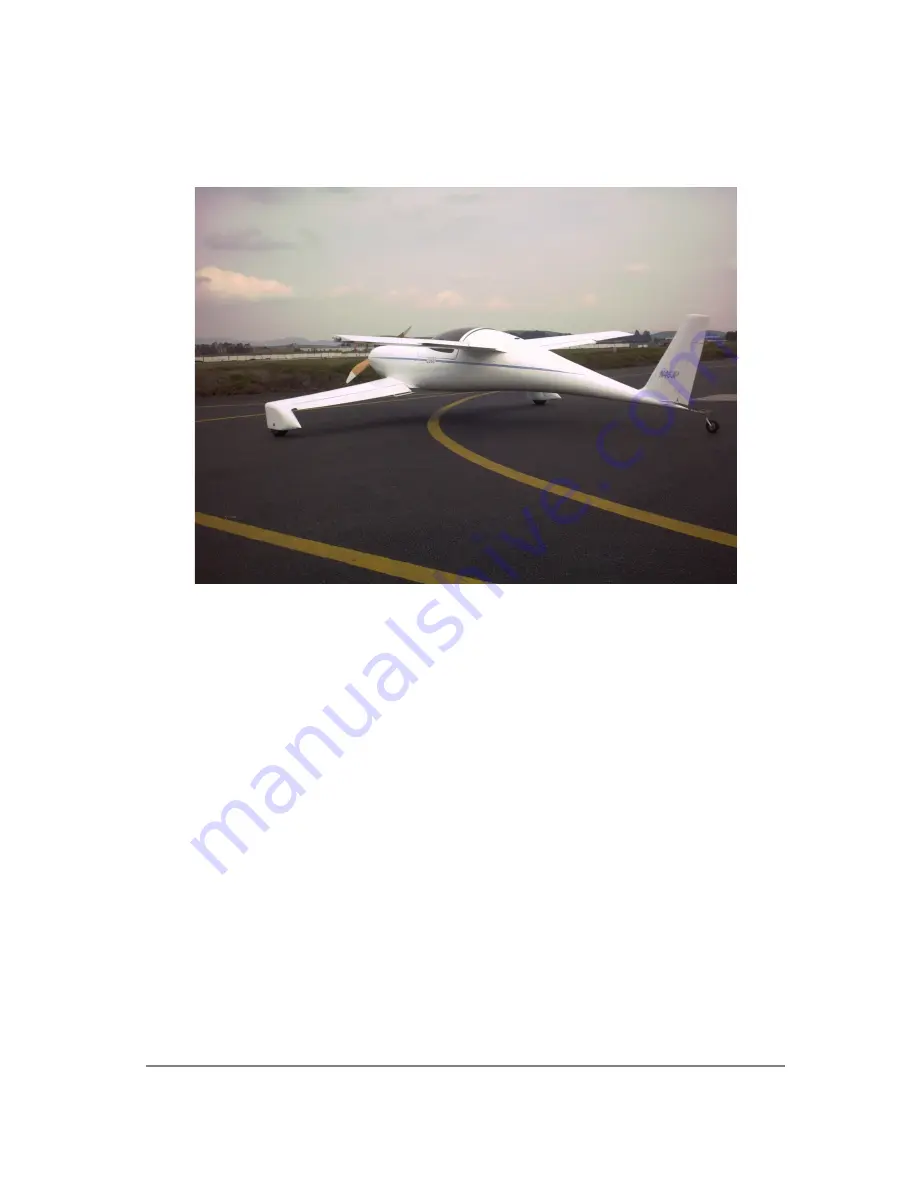
Q2 Quickie Construction Manual
The QUICKIE Q2 kit, properly constructed, will reproduce the successful
original QUICKIE Q2 designed, and tested by QUICKIE AIRCRAFT CORPORATION.
QUICKIE AIRCRAFT CORPORATION is not responsible, and makes no warranties,
express or implied whatsoever, regarding the structural integrity,
performance, flight characteristics, or safety of the Buyer's completed
aircraft and its component parts. QUICKIE AIRCRAFT CORPORATION has no control
and assumes no control over the Buyer's ability to successfully construct and
test the QUICKIE Q2 AIRCRAFT. Buyer expressly waives any and all claims
arising from structural integrity, performance, flight characteristics,
mechanical failures, and safety against QUICKIE AIRCRAFT CORPORATION. Buyer
acknowledges awareness of the risks of flying a homebuilt aircraft. Buyer
acknowledges that the FAA must inspect the aircraft at construction intervals,
as well as the completed project, prior to flight and should work with his
local FAA representative regarding the construction and licensing of the
aircraft.
..
QUICKIE AIRCRAFT CORPORATION reserves the right to make recommended revisions
in the plans and construction of the aircraft at any time without liability to
QUICKIE AIRCRAFT CORPORATION, as such revisions or changes may be deemed
advisable from time to time.
Summary of Contents for Q2 Lite
Page 10: ...Q2 Plans Appendix Page v Q2 Plans Chapter 1 Page 1 1...
Page 17: ...Q2 Plans Chapter 1 Page 1 3...
Page 18: ......
Page 25: ...CONTINUED ON NEXT PAGE PAGE 3 1 Q2 Plans Chapter 3 Page 3 02...
Page 29: ...CONTINUED ON NEXT PAGE...
Page 70: ...CONTINUED ON NEXT PAGE PAGE 3 15 Q2 Plans Chapter 3 Page 3 16...
Page 71: ......
Page 72: ......
Page 74: ...CONTINUED ON NEXT PAGE PAGE 3 16 Q2 Plans Chapter 3 Page 3 17...
Page 115: ...Q2 Plans Chapter 6 Page 6 02...
Page 123: ...END OF CHAPTER PAGE 7 2 Q2 Plans Chapter 8 Page 8 01...
Page 127: ...CONTINUED ON NEXT PAGE PAGE 8 2 Q2 Plans Chapter 8 Page 8 03...
Page 134: ...END OF CHAPTER PAGE 8 5...
Page 136: ...NOTE See Bottom and Top Main Wing Lamination Drawing for exact sizing of sparcaps A thru M...
Page 137: ...CONTINUED ON NEXT PAGE PAGE 9 1 Q2 Plans Chapter 9 Page 9 02...
Page 138: ...CONTINUED ON NEXT PAGE PAGE 9 2 Q2 Plans Chapter 9 Page 9 03...
Page 154: ...CONTINUED ON NEXT PAGE PAGE 9 8 Q2 Plans Chapter 9 Page 9 09...
Page 155: ......
Page 161: ...PAGE 10 2 Q2 Plans Chapter 10 Page 10 03 PAGE 10 3...
Page 167: ...PAGE 10 5...
Page 174: ......
Page 176: ...CONTINUED ON NEXT PAGE PAGE 10 9 Q2 Plans Chapter 10 Page 10 10...
Page 185: ...PAGE 11 2...
Page 187: ...CONTINUED ON NEXT PAGE PAGE 11 3...
Page 192: ...CONTINUED ON NEXT PAGE PAGE 11 5...
Page 196: ...PAGE 12 1...
Page 198: ......
Page 199: ......
Page 200: ...PAGE 12 2...
Page 206: ...PAGE 13 1 Q2 Plans Chapter 13 Page 13 02...
Page 209: ...PAGE 13 2 Q2 Plans Chapter 13 Page 13 03...
Page 211: ......
Page 212: ......
Page 213: ...PAGE 13 3...
Page 216: ...END OF CHAPTER PAGE 13 4...
Page 221: ...PAGE 14 2 Q2 Plans Chapter 14 Page 14 03...
Page 225: ......
Page 227: ...CONTINUED ON NEXT PAGE PAGE 14 4 Q2 Plans Chapter 14 Page 14 05...
Page 230: ...CONTINUED ON NEXT PAGE PAGE 14 5 Q2 Plans Chapter 14 Page 14 06...
Page 237: ......
Page 238: ...CONTINUED ON NEXT PAGE PAGE 14 8...
Page 240: ...PAGE 14 9...
Page 242: ......
Page 243: ...PAGE 14 10...
Page 246: ...PAGE 15 1 Q2 Plans Chapter 15 Page 15 02...
Page 249: ...END OF CHAPTER PAGE 15 2 Q2 Plans Chapter 16 Page 16 01 ENGINE INSTALLATION...
Page 254: ...PAGE 16 2 Q2 Plans Chapter 16 Page 16 03...
Page 257: ......
Page 258: ...PAGE 16 3 Q2 Plans Chapter 16 Page 16 04...
Page 263: ......
Page 264: ...PAGE 16 5 Q2 Plans Chapter 16 Page 16 06...
Page 266: ......
Page 272: ......
Page 273: ...PAGE 17 2...
Page 276: ...END OF CHAPTER PAGE 17 3...
Page 279: ...END OF CHAPTER PAGE 18 1...
Page 284: ......
Page 286: ......
Page 288: ......
Page 295: ...Congratulations on completing your very own Q2 PAGE 20 4...
Page 296: ...Q2 Plans Chapter 20 Page 20 05...
Page 297: ......
Page 299: ......