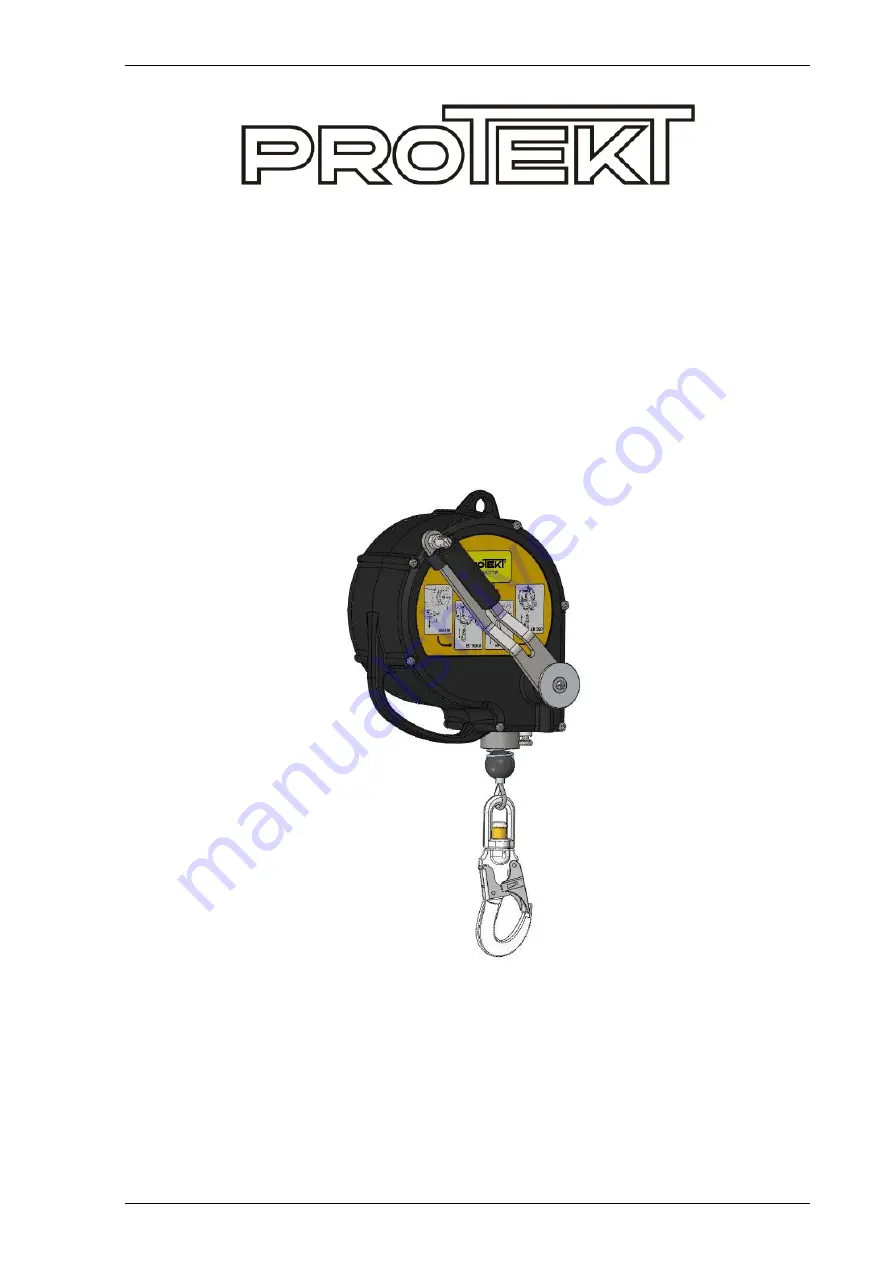
edition: PROTEKT_EN-01
CRW 200
RETRACTABLE TYPE FALL ARRESTER
RESCUE LIFTING DEVICE
SERVICE MANUAL
CONTENTS
1. CRW 200 Technical specification
.......................................
1.1.
Description ...............................................................
1.2.
Technical data ..........................................................
1.3.
Standards .................................................................
1.4.
Identification and marking ........................................
2. Terms of servicing
..............................................................
3. Servicing equipment
..........................................................
4. Servicing operations
..........................................................
4.1. The device dismantling ..................................................
4.2. The retracting spring set maintenance and inspection ..
4.3. The drum set maintenance and inspection ....................
4.4 The brake set maintenance and inspection ....................
4.5. The winch unit dismantling and maintenance ................
4.6. The device rebuilding ....................................................
5. Post assembly check
.........................................................
6. CRW200 - Spare parts
........................................................
2
2
2
2
2
3
3
4
4
6
6
7
9
10
12
13