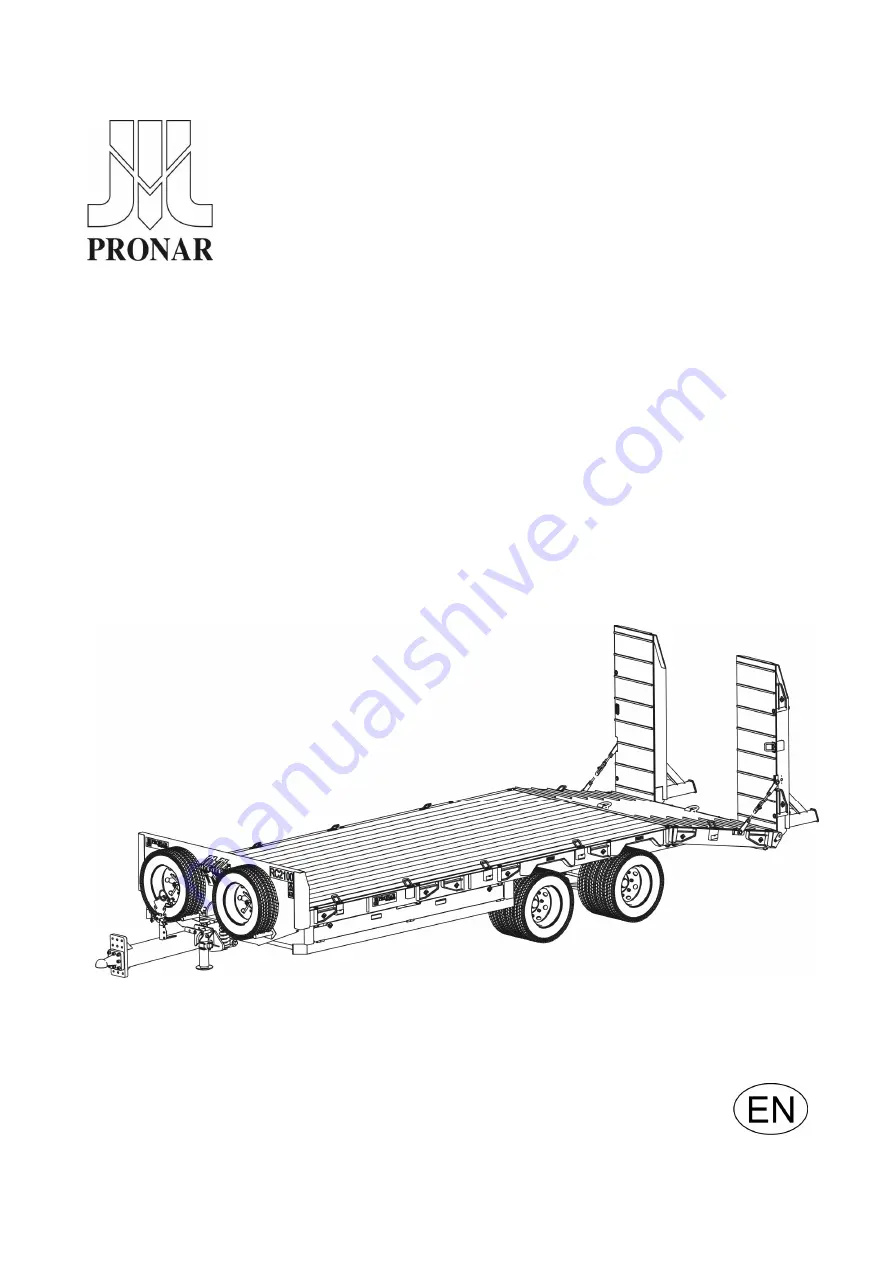
PRONAR Sp. z o.o.
17-210 NAREW, UL. MICKIEWICZA 101A, WOJ. PODLASKIE
tel.:
+48 085 681 63 29
+48 085 681 64 29
+48 085 681 63 81
+48 085 681 63 82
fax:
+48 085 681 63 83
+48 085 682 71 10
www.pronar.pl
OPERATOR'S MANUAL
AGRICULTURAL TRAILER
PRONAR RC2100
TRANSLATION OF THE ORIGINAL COPY OF THE MANUAL
ISSUE 2A-09-2010
PUBLICATION NO 208N-00000000-UM
Summary of Contents for RC2100
Page 2: ......
Page 6: ......
Page 11: ...SECTION 1 BASIC INFORMATION ...
Page 24: ...Pronar RC2100 SECTION 1 1 14 ...
Page 25: ...SECTION 2 SAFETY ADVICE ...
Page 41: ...SECTION 2 Pronar RC2100 2 17 FIG 2 3 Locations of information and warning decals ...
Page 42: ...Pronar RC2100 SECTION 2 2 18 ...
Page 43: ...SECTION 3 DESIGN AND OPERATION ...
Page 58: ...Pronar RC2100 SECTION 3 3 16 ...
Page 59: ...SECTION 4 CORRECT USE ...
Page 82: ...Pronar RC2100 SECTION 4 4 24 ...
Page 83: ...SECTION 5 MAINTENANCE ...
Page 113: ...SECTION 5 Pronar RC2100 5 31 FIG 5 12 Lubrication points part 1 ...
Page 114: ...Pronar RC2100 SECTION 5 5 32 FIG 5 13 Lubrication points part 2 ...
Page 123: ...NOTES ...
Page 124: ... ...
Page 125: ...ANNEX A Tyre dimensions LP AXLE FRONT REAR WHEEL BRAKE 1 215 75 R17 5 135 133 J 17 5x6 75 ...