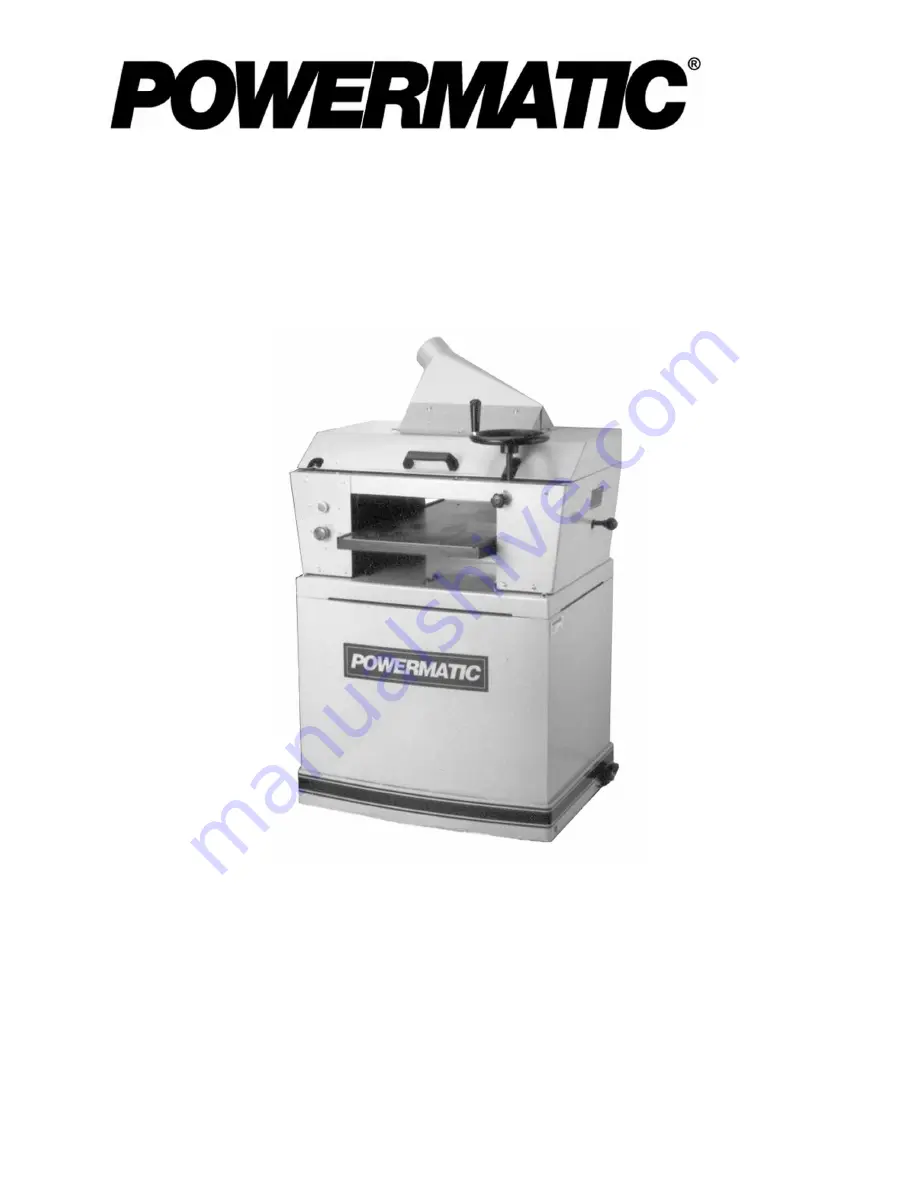
Operating Instructions and Parts Manual
15-inch Planer-Molder
Model PM15
*Manual Revision F for machines with serial number 0412PM15488 and higher
WMH TOOL GROUP, Inc.
2420 Vantage Drive
Elgin, Illinois 60124
Part No. M-0460264
Ph.: 800-274-6848
*Revision F
9/07
www.powermatic.com
Copyright © 2007 WMH Tool Group, Inc.
Summary of Contents for PM15
Page 29: ...29 Base Assembly ...
Page 31: ...31 Gearbox Assembly ...
Page 33: ...33 Stand Assembly ...
Page 36: ...36 Cutterhead Hood and Table Assembly ...
Page 37: ...37 Accessories Knives and Moldings for PM15 Planer Molder ...
Page 38: ...38 Accessories Knives and Moldings cont ...
Page 39: ...39 Electrical Connections ...