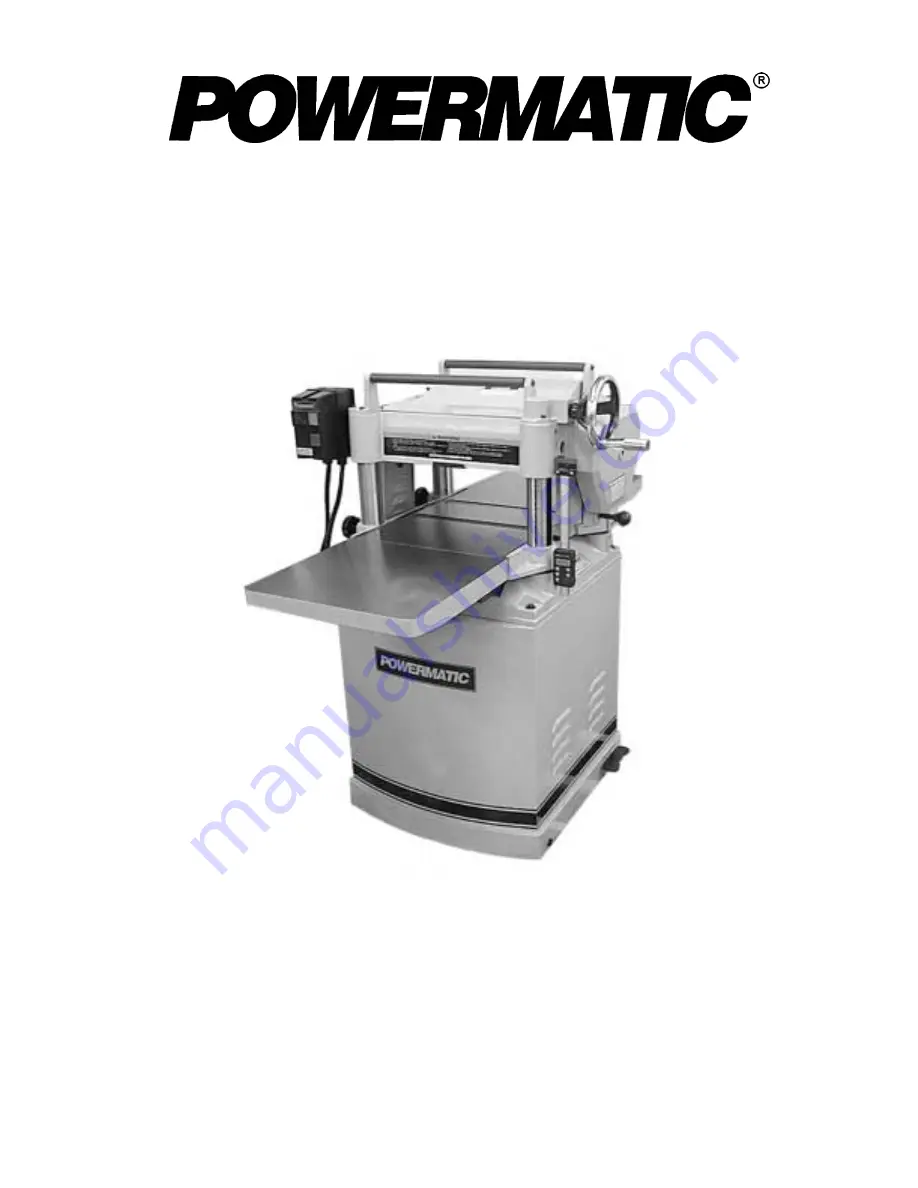
OWNER’S MANUAL
Model 15S Planer
WMH TOOL GROUP
Consumer Woodworking Division
2420 Vantage Drive
Elgin, IL 60123
Ph: 888-804-7129
▪
Fax: 800-274-6840
E-mail: [email protected]
M-0460286 10/03
www.wmhtoolgroup.com
Copyright © WMH Tool Group
Summary of Contents for 15S
Page 7: ...7 FEATURES 15S Planer Fig 2 ...
Page 33: ...33 Base Assembly 15S Planer ...
Page 35: ...35 Table Assembly 15S Planer ...
Page 37: ...37 Gearbox Assembly 15S Planer ...
Page 39: ...39 Cabinet Assembly 15S Planer ...
Page 42: ...42 Head Assembly 15S Planer ...
Page 43: ...43 ELECTRICAL SCHEMATIC 15S Planer Single phase 230 volt ...
Page 44: ...44 ...
Page 46: ...46 ...
Page 47: ...47 ...