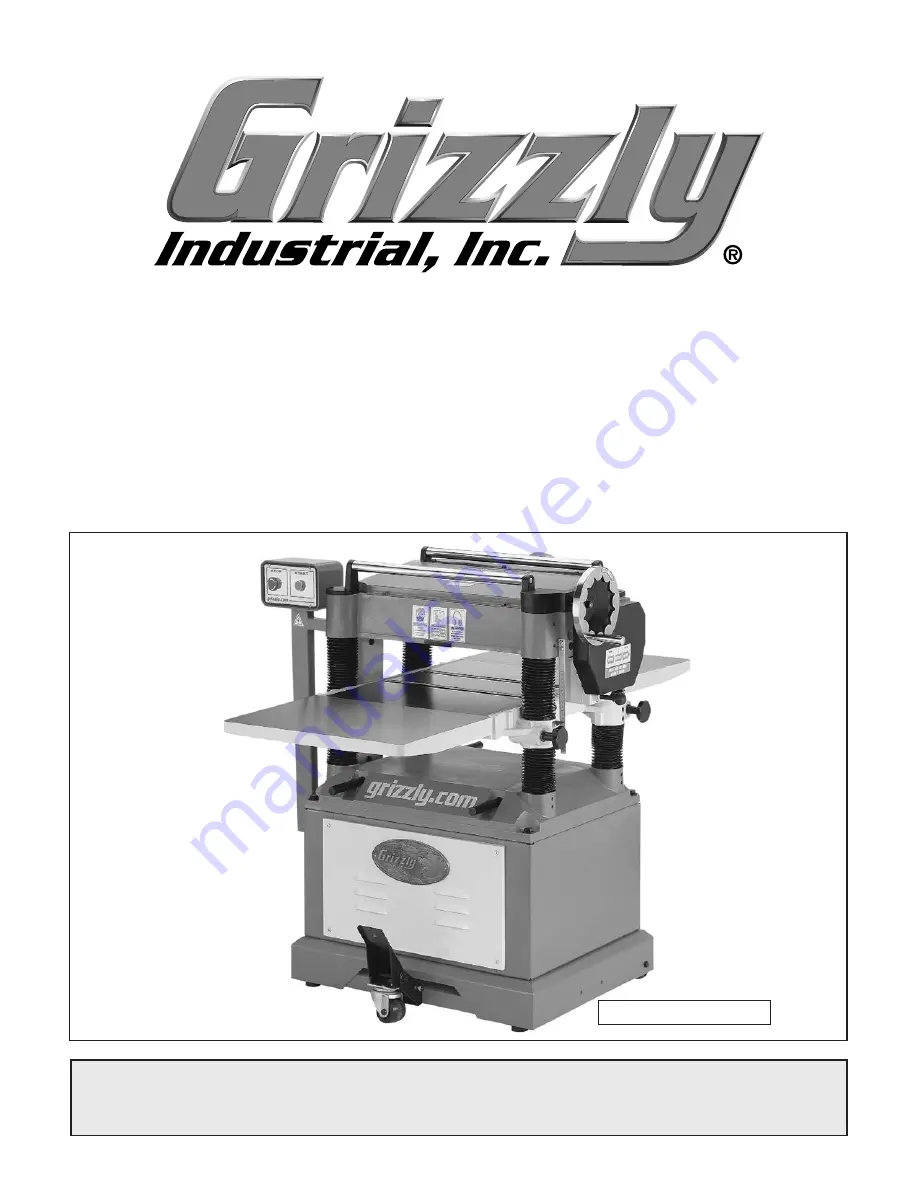
MODEL G0453Z/G0454Z
15" & 20" MOBILE PLANER
w/SPIRAL CUTTERHEAD
OWNER'S MANUAL
COPYRIGHT © APRIL, 2009 BY GRIZZLY INDUSTRIAL, INC., REVISED JUNE, 2018 (HE)
WARNING: NO PORTION OF THIS MANUAL MAY BE REPRODUCED IN ANY SHAPE
OR FORM WITHOUT THE WRITTEN APPROVAL OF GRIZZLY INDUSTRIAL, INC.
(FOR MODELS MANUFACTURED SINCE 1/09) #TS11416 PRINTED IN CHINA
Model G0454Z Shown
Summary of Contents for G0453Z
Page 68: ......