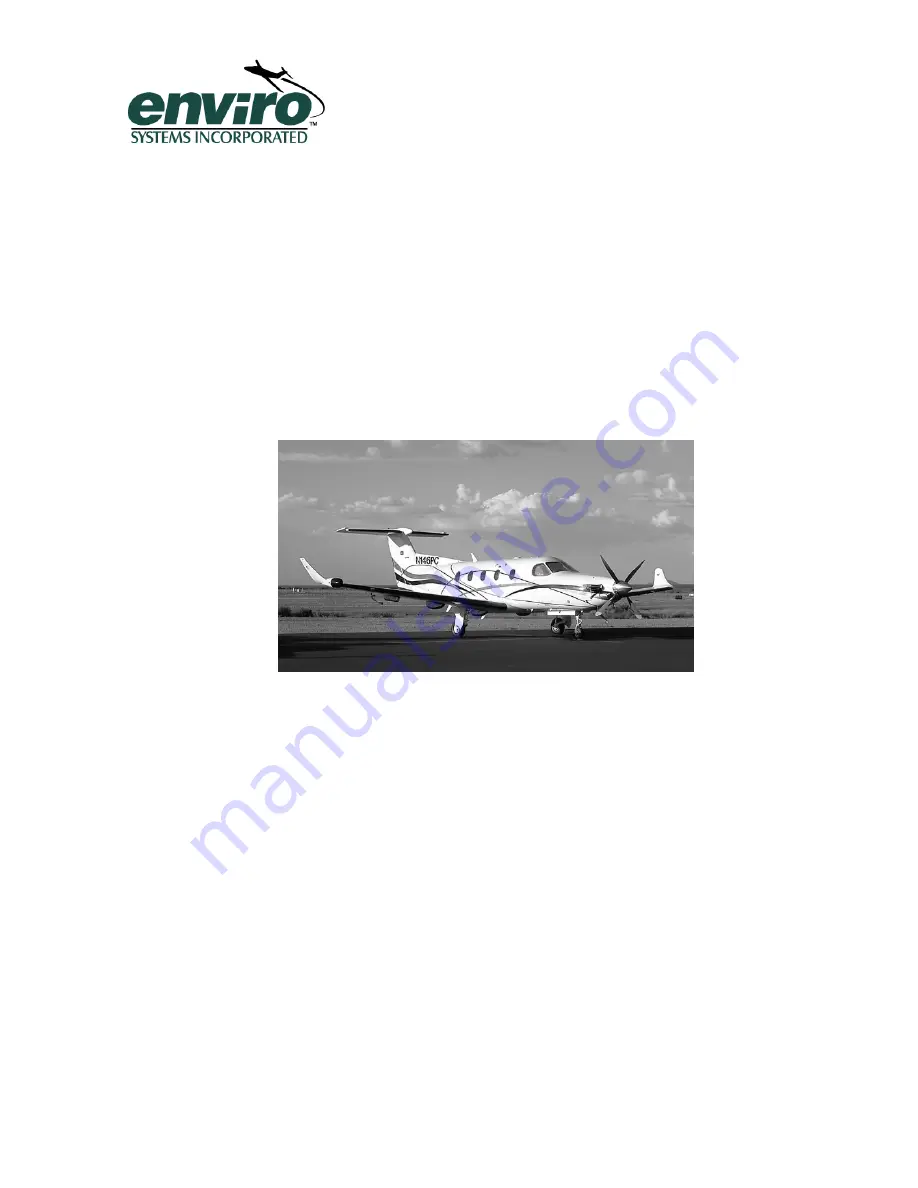
12037 N Highway 99
Seminole, OK 74868
Phone (405) 382-0731
Fax (405) 382-0737
http://www.enviro-ok.com
COPYRIGHT
2007
ENVIRO SYSTEM INC.
ORIGINAL ISSUE
DECEMBER 28/ 2007
21-00-22
JULY 21, 2011
OPERATING, SERVICING, AND COMPONENT
MAINTENANCE MANUAL
WITH ILLUSTRATED PARTS LIST
PILATUS PC12
R-12 AIR CONDITIONING SYSTEM COMPONENTS:
1) COMPRESSOR CONDENSER MODULE ASSEMBLY, PART # 1250900-4
2) EVAPORATOR MODULE ASSEMBLY, PART # 1250200-42 (L) /-43 (C,R)
ATA SPECIFICATION
21-00-22