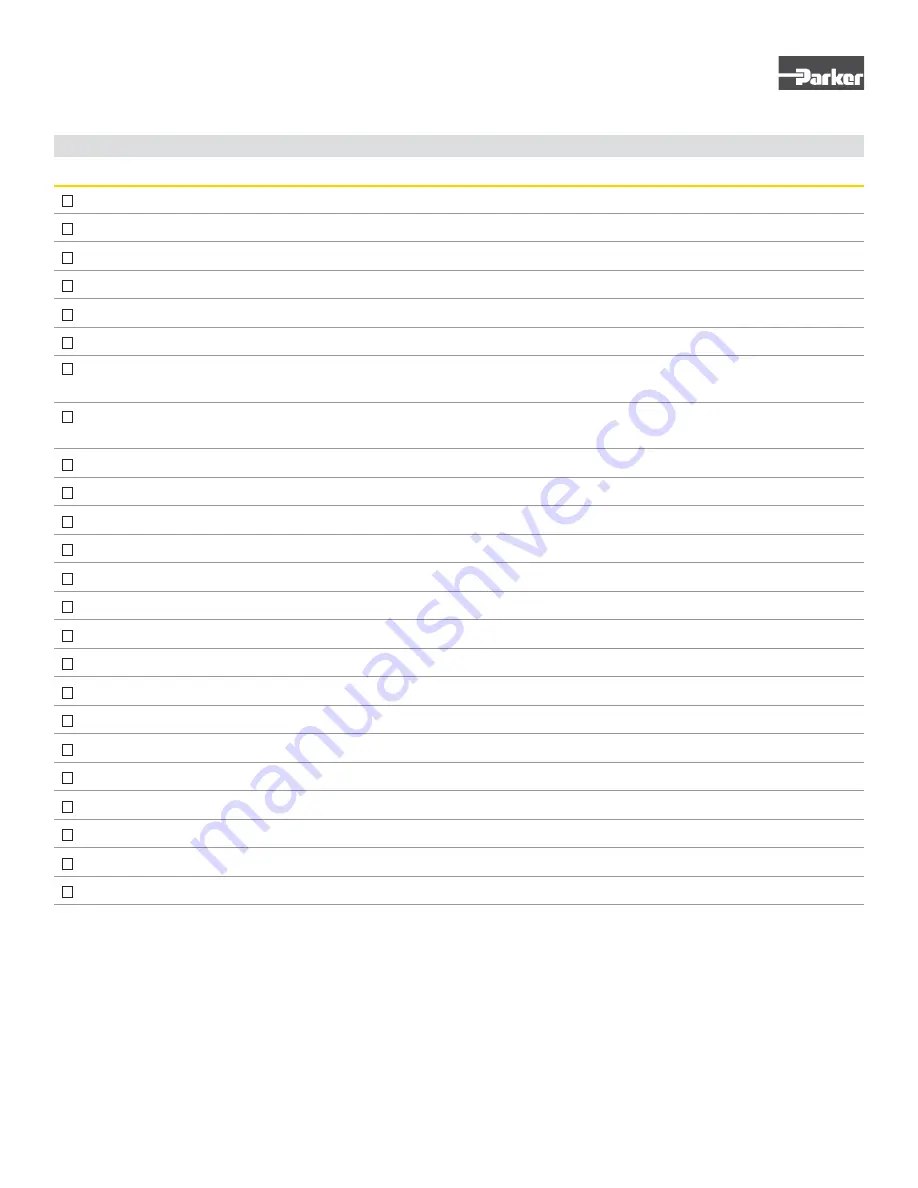
Pneumatic Division
Richland, Michigan USA
www.parker.com/pneumatics
H SERIES FIELDBUS SYSTEM
Bulletin Number
Bulletin Description
32 Point Valve Driver Series A, PSSV32A Instructions
DeviceNet Adapter Series A, PSSCDM12A, PSSCDM18PA Instructions
PROFIBUS Adapter Series A, PSSCPBA Instructions
ControlNet Adapter Series A, PSSCCNA Instructions
EtherNet/IP Adapter Series A, PSSCENA Instructions
24VDC Expansion Power Supply Series A, PSSSE24A Instructions
Relay Output Module Series A, PSSTR4M12A Instructions
24VDC Analog Input Module Series A, PSSNACM12A, PSSNAVM12A Instructions
24VDC Analog Output Module Series A, PSSTACM12A, PSSTAVM12A Instructions
I/O RS-232 ASCII Module Series A, PSSS23A Instructions
Industrial Automation Wiring and Grounding Guidelines
Safety Guidelines for Application Installation & Maintenance of Solid State Control
Extension Units, Series A, PSSEXT1, PSSEXT3 Instructions
DeviceNet Media, Design & Installation Guide
I/O ControlNet Adapter, PSSCCNA Release Notes
I/O EtherNet I/P Adapter, PSSCENA Release Notes
Serial Bus System, Selection Guide
DeviceNet Adapters, PSSCDM12A, PSSCDM18PA, User Manual
25-Pin, D-Sub Cable, Installation & Service Instructions
ex Fieldbus, Installation & Service Instructions
Turck Fieldbus, Installation & Service Instructions
(03-05-2019)
Click here to view bookmarks.
Summary of Contents for H Series
Page 135: ...DeviceNet Media Design and Installation Guide...
Page 144: ...Publication DNET UM072C EN P July 2004 Table of Contents iv...
Page 170: ...Publication DNET UM072C EN P July 2004 1 26 Get Started Notes...
Page 194: ...Publication DNET UM072C EN P July 2004 2 24 Identify Cable System Components Notes...
Page 212: ...Publication DNET UM072C EN P July 2004 3 18 Make Cable Connections Notes...
Page 238: ...Publication DNET UM072C EN P July 2004 4 26 Determine Power Requirements Notes...
Page 248: ...Publication DNET UM072C EN P July 2004 5 10 Correct and Prevent Network Problems Notes...
Page 250: ...Publication DNET UM072C EN P July 2004 A 2 Understand Select NEC Topics Notes...
Page 263: ......
Page 267: ...Isysnet Serial Bus System Selection Guide Pneumatic...
Page 287: ...H Series Fieldbus DeviceNet Adapters PSSCDM12A PSSCDM18PA User Manual...