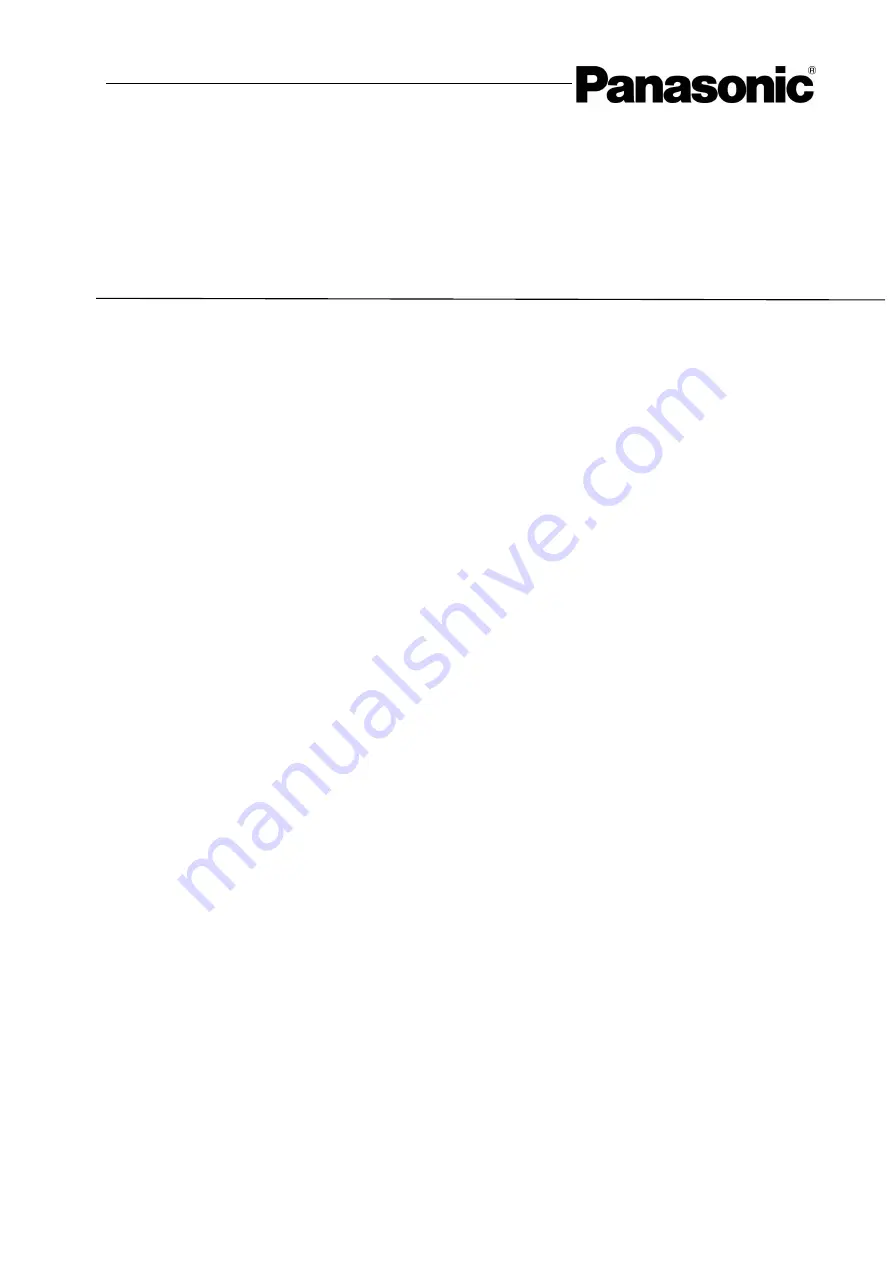
● Thank you for your purchase of Panasonic welding power source.
● Before operating this product, please read the instructions carefully and save this
manual for future use. First of all, please read “Safety precautions” or “Safety
manual”.
● SPEC. No.
:
YD-500KR2HD0
、
YD-500KR2HU0
Panasonic Welding Systems (Tangshan) Co., Ltd.
Model No.
YD-500KR
Operating Instructions
Thyristor Controlled MIG/MAG Arc Welding Power Source
TSM50262-02
Summary of Contents for YD-500KR
Page 45: ...CIRCUITDIAGRAM ...
Page 46: ...44 OUTSIDE DRAWING W D H YD 500KR2 436 675 762 ...