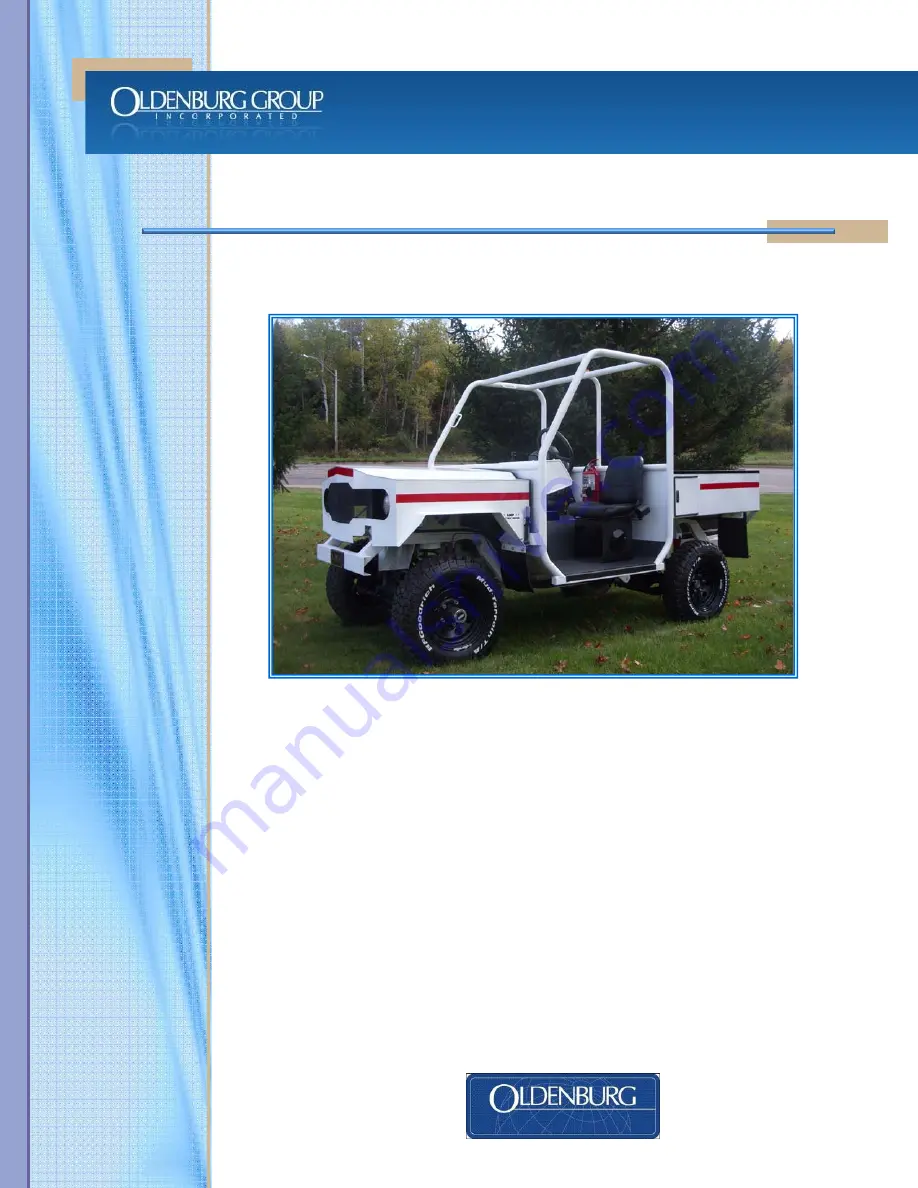
EUV-400 ELECTRIC UTILITY VEHICLE
PARTS AND SERVICE MANUAL
PUB. NO. 1486
© 2010 All rights reserved.
OLDENBURG ELECTRIC UTILITY VEHICLE INCLUDES:
25 HP OLDENBURG ELECTRIC AC MOTOR
HEAVY DUTY DANA 44 DRIVE AXLES
FRONT AND REAR DISC BRAKES
ATLAS TRANSFER CASE
FLUX VECTOR VARIABLE SPEED AC DRIVE
DIGITAL GRAPHIC DISPLAY
REMOVABLE BATTERY PACK WITH QUICK DISCONNECT
with AMP Electric Drive
Revision
2
November
2010
Summary of Contents for euv-400
Page 2: ......
Page 11: ...2 3 SECTION 2 SAFETY Seat Belts Battery Disconnect Battery Disconnect ...
Page 33: ...3 15 SECTION 3 PARTS DROP BOX GROUP Transfer Case 706067 Qty 1 Front View Rear View ...
Page 41: ...3 23 SECTION 3 PARTS OPTIONS LED Backup Lights 704070 Qty 2 ...
Page 56: ......
Page 58: ......
Page 59: ......