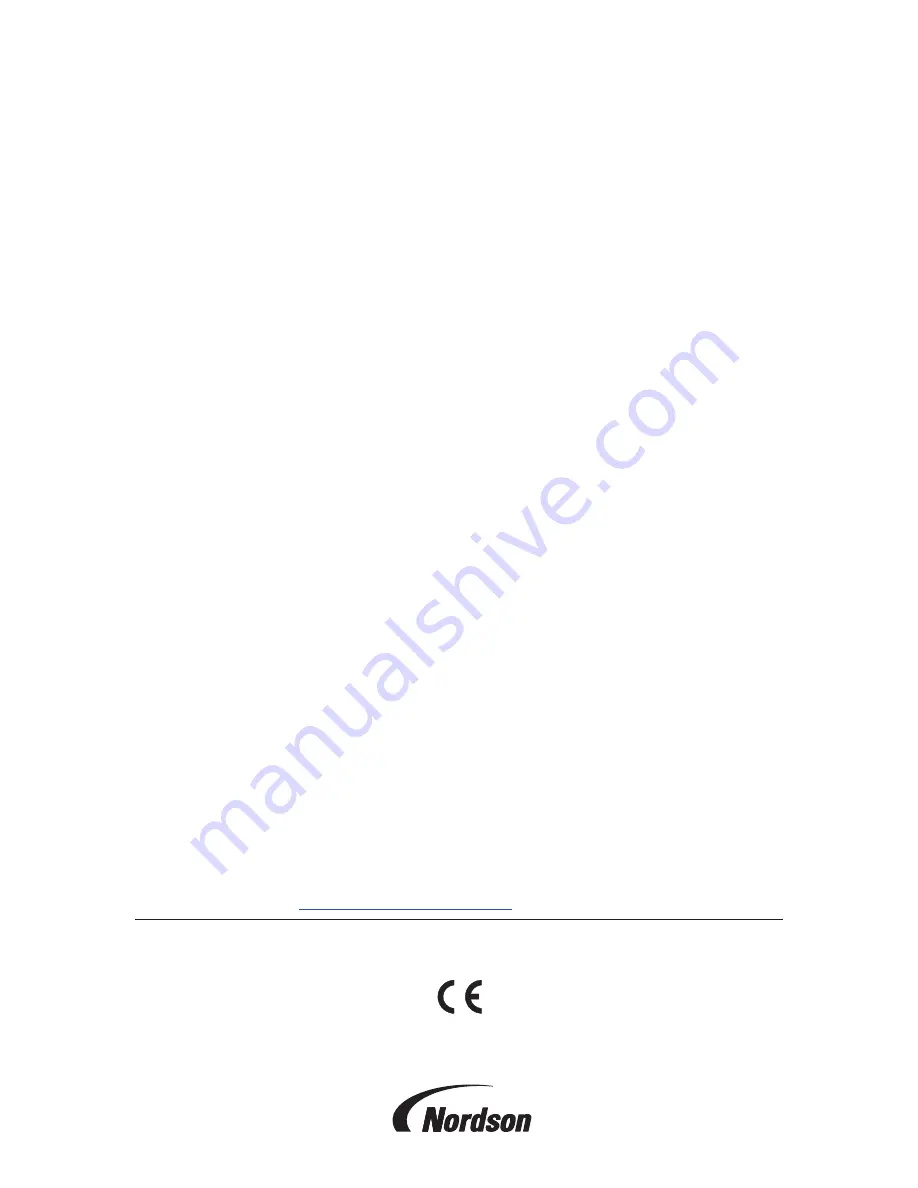
Trilogy
®
GP and LVLP Air
Spray Siphon Fed Manual
Spray Guns
Customer Product Manual
Document Number
1601056-05
Issued 12/21
For parts and technical support, call the Industrial Coating
Systems Customer Support Center at (800) 433-9319 or
contact your local Nordson representative.
This document is subject to change without notice.
for the latest version.
NORDSON CORPORATION • AMHERST, OHIO • USA