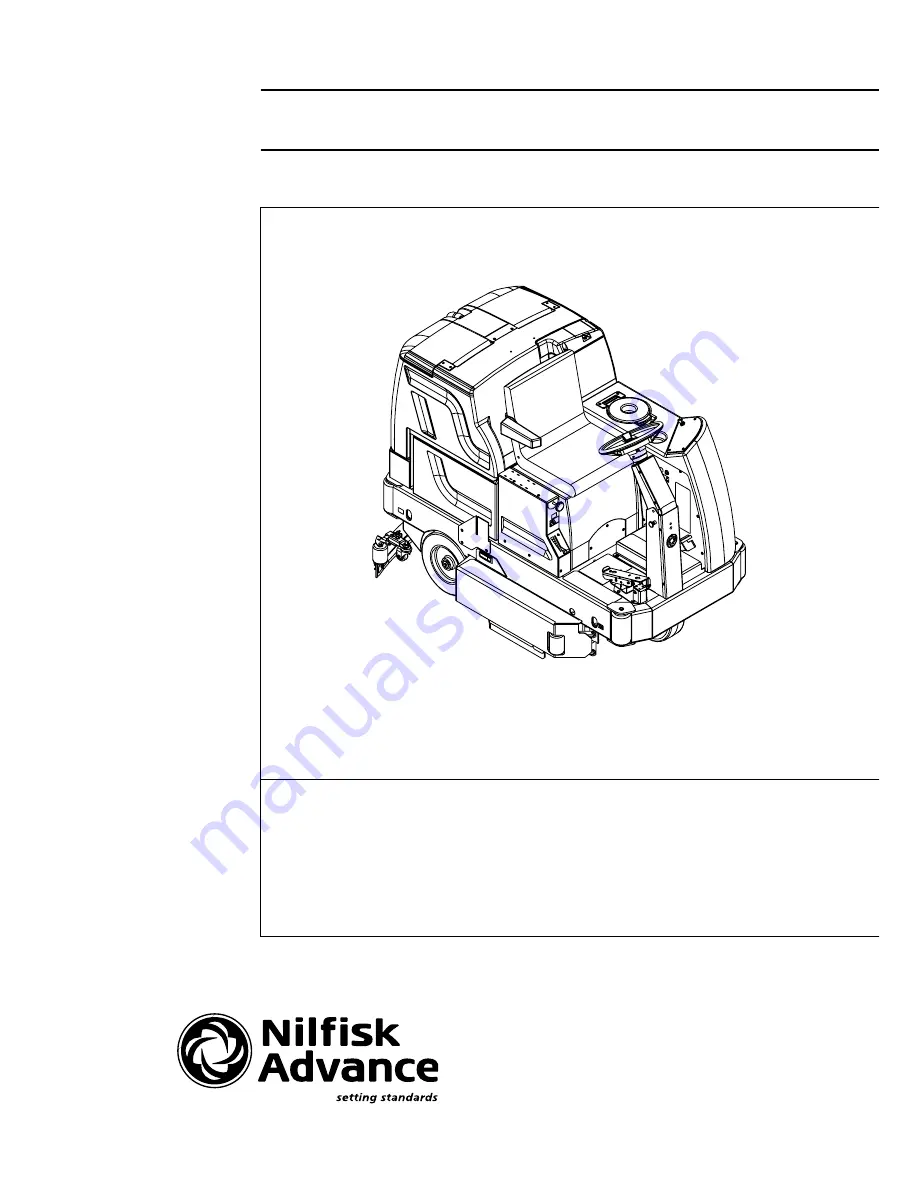
1/01 revised 2/05 Form Number 56043058
Hydro-Retriever
™
3800
Hydro-Retriever
™
2042
BR 1100, 1100C, 1100C-XL
SERVICE MANUAL
Advance MODELS 56410000 (disc), 56410350 (cyl.),
56410001 (2042), 56410500 (cyl. rollout),
56410501 (disc rollout), 56410502 (2042 rollout)
Nilfisk MODELS 56410002 (disc), 56410351 (cyl.),
56410425 (1100C-XL)