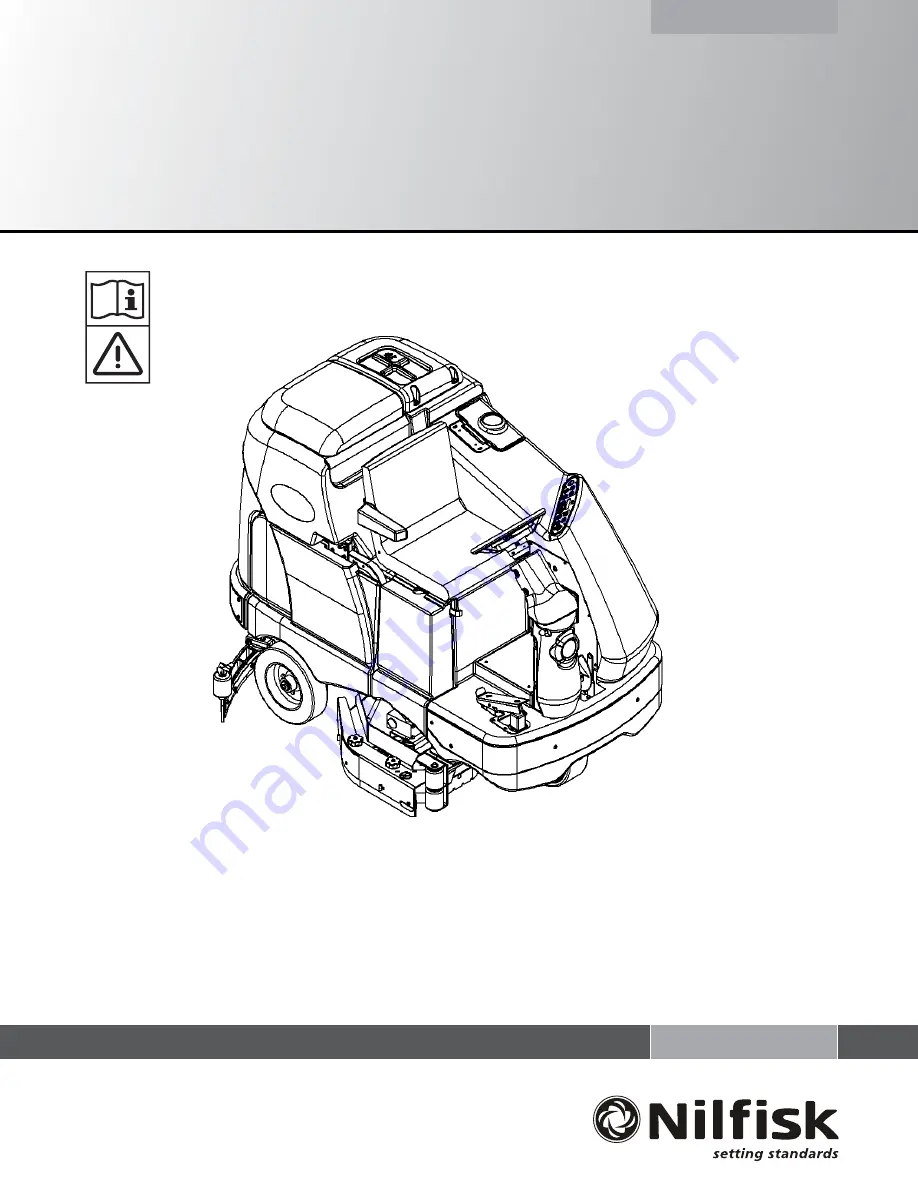
BR 1100S, BR 1300S
Service Manual
11/08 revised
2
/10
FORM NO. 56043122
Printed in USA
Models:
56413006(BR 1100S), 56413007(BR 1100S C / w/sweep system), 56413889(OBS / BR 1100S C / w/o sweep system)
56413010(BR 1300S), 56413011(BR 1300S C / w/sweep system), 56413890(OBS / BR 1300S C / w/o sweep system)
56413785(BR 1100S EDS), 56413781(BR 1100S C EDS / w/sweep system), 56413897(OBS / BR 1100S C EDS / w/o sweep system)
56413782(BR 1300S EDS), 56413783(BR 1300S C EDS / w/sweep system), 56413898(OBS / BR 1300S C EDS / w/o sweep system)
Summary of Contents for 56413006
Page 7: ...FORM NO 56043122 BR 1100S 1300S 5 SPECIFICATIONS ...
Page 9: ...FORM NO 56043122 BR 1100S 1300S 7 FIGURE 1 ...
Page 10: ...8 FORM NO 56043122 BR 1100S 1300S THIS PAGE INTENTIONALLY BLANK ...
Page 36: ...34 FORM NO 56043122 BR 1100S 1300S 4 RECOVERY SYSTEM FIGURE 4 2 ...
Page 39: ...FORM NO 56043122 BR 1100S 1300S 37 SQUEEGEE SYSTEM 5 FIGURE 5 2 ...
Page 47: ...FORM NO 56043122 BR 1100S 1300S 45 WHEEL DRIVE SYSTEM 6 FIGURE 6 5 ...
Page 53: ...FORM NO 56043122 BR 1100S 1300S 51 REAR WHEEL SYSTEM 7 FIGURE 7 3 ...
Page 61: ...FORM NO 56043122 BR 1100S 1300S 59 ELECTRICAL SYSTEM 8 J Ø 4 K Fault Indicator 03 FIGURE 8 7 ...