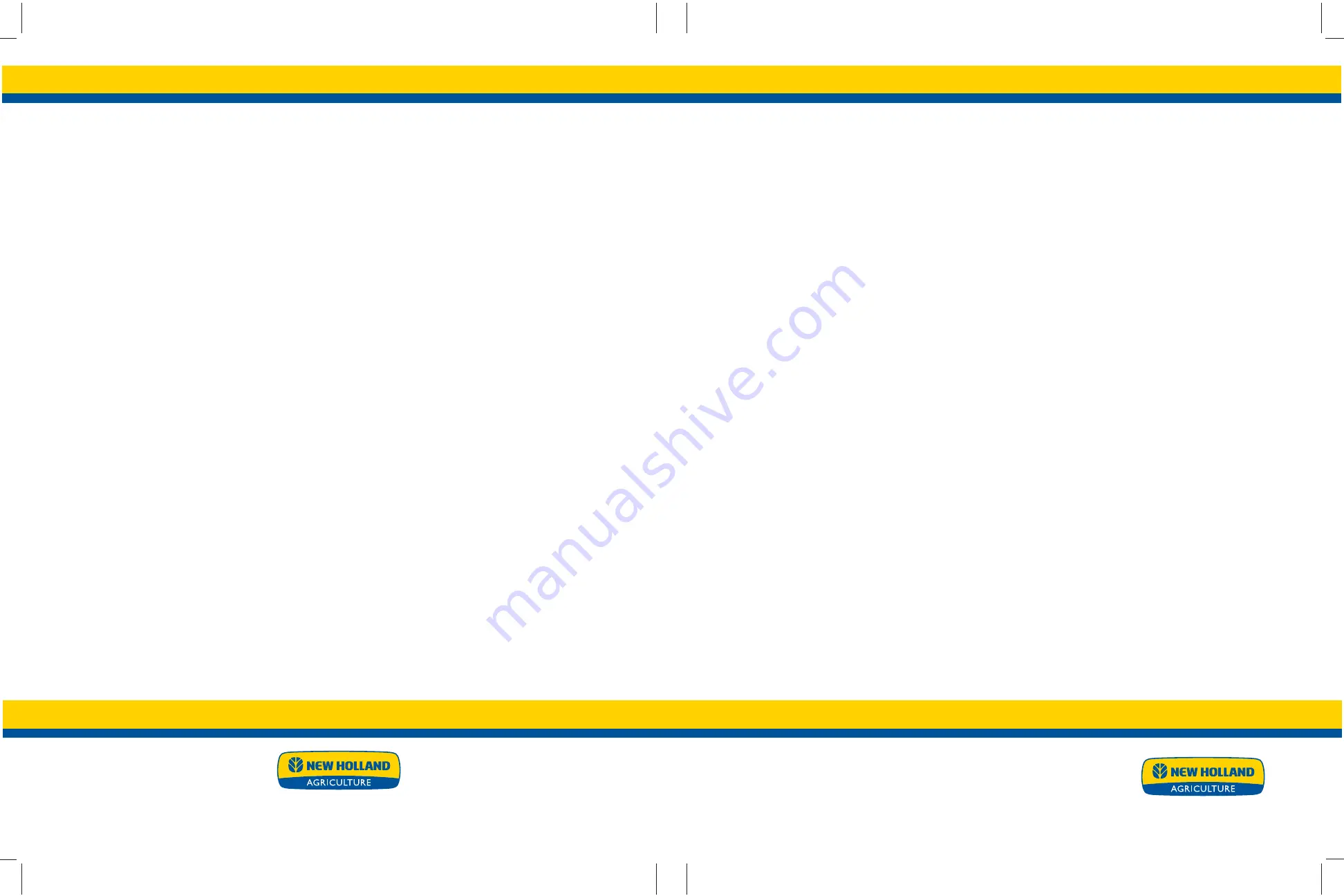
Part number 47881877
1
st
edition English
January 2016
SERVICE MANUAL
Workmaster
™
33
Workmaster
™
37
Tier 4B (final)
Compact Tractor
Printed
in U.S.A.
© 2016 CNH Industrial America LLC. All Rights Reserved.
New
Holland is a trademark registered in the United States and many other countries,
owned by or licensed to CNH Industrial N.V., its subsidiaries or affiliates.
Summary of Contents for Workmaster 33 Tier 4B
Page 7: ...47881877 13 01 2016 Find manuals at https best manuals com ...
Page 8: ...INTRODUCTION 47881877 13 01 2016 1 Find manuals at https best manuals com ...
Page 14: ...INTRODUCTION Safety rules Workmaster 33 NA Workmaster 37 NA BT09A213 1 47881877 13 01 2016 7 ...
Page 37: ...INTRODUCTION NHIL15CT00475HA 1 47881877 13 01 2016 30 ...
Page 41: ...INTRODUCTION 47881877 13 01 2016 34 ...
Page 51: ...This as a preview PDF file from best manuals com Download full PDF manual at best manuals com ...