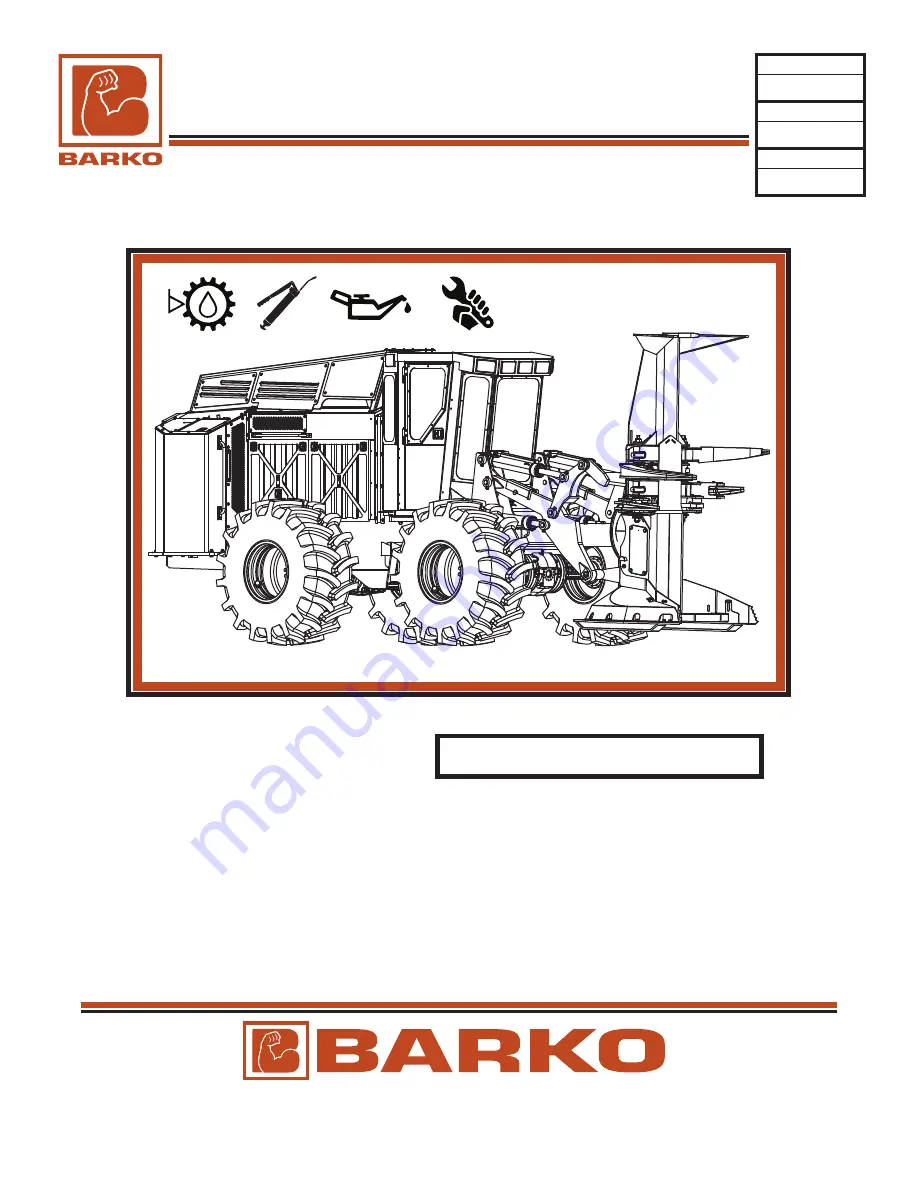
®
SERVICE MANUAL
®
1 Banks Avenue • Superior • WI • 54880
Phone:
800-544-6532 • 715-395-6700
Fax:
800-772-2448 • 715-392-9348
Web:
www.barko.com
Email:
MANUAL P/N
REVISION
DATE
Serial Number Range:
Machine Serial Number:
NOTE:
This Service Manual does not include safety, operation, or parts information. Seperate Oprator’s and Parts Manuals are
available for this machine and can be purchased through your Barko dealer. The Operator’s Manual include safety instructions
which must be read and understood before operating or servicing this machine. Keep the machine’s Operator’s Manual with
the machine at all times.
The information and illustrations in this manual have been approved as accurate at the time of printing. However, this manual
may contain information on options not present on your loader. The right is reserved by Barko Hydraulics, LLC to make
changes and improvements in its product at any time without notice or obligation.
Grapple and attachment information is not included in this manual. See separate Grapple and Attachment Owner’s,
Installation, Parts and Service Manual(s) which accompanies all grapples from the factory.
800-00479
0
06/07/2019
WHEELED FELLER BUNCHER (WFB)
830B
11983025001 thru
Summary of Contents for 830B
Page 4: ...THIS PAGE INTENTIONALLY BLANK SUPERIOR WI USA www barko com...
Page 42: ...THIS PAGE LEFT INTENTIONALLY BLANK...
Page 48: ...THIS PAGE LEFT INTENTIONALLY BLANK...
Page 50: ...THIS PAGE LEFT INTENTIONALLY BLANK...
Page 54: ...THIS PAGE LEFT INTENTIONALLY BLANK...
Page 60: ...THIS PAGE LEFT INTENTIONALLY BLANK...
Page 70: ...THIS PAGE LEFT INTENTIONALLY BLANK...
Page 94: ...THIS PAGE LEFT INTENTIONALLY BLANK...
Page 102: ...THIS PAGE LEFT INTENTIONALLY BLANK...
Page 104: ...THIS PAGE LEFT INTENTIONALLY BLANK...
Page 114: ...THIS PAGE LEFT INTENTIONALLY BLANK...
Page 118: ...THIS PAGE LEFT INTENTIONALLY BLANK...
Page 124: ...THIS PAGE LEFT INTENTIONALLY BLANK...
Page 133: ...THIS PAGE LEFT INTENTIONALLY BLANK...
Page 134: ...THIS PAGE LEFT INTENTIONALLY BLANK...
Page 138: ...THIS PAGE LEFT INTENTIONALLY BLANK...
Page 172: ...THIS PAGE LEFT INTENTIONALLY BLANK...
Page 181: ...THIS PAGE LEFT INTENTIONALLY BLANK...
Page 182: ...THIS PAGE LEFT INTENTIONALLY BLANK...
Page 184: ...THIS PAGE LEFT INTENTIONALLY BLANK...
Page 194: ...THIS PAGE LEFT INTENTIONALLY BLANK...
Page 207: ...THIS PAGE LEFT INTENTIONALLY BLANK...
Page 208: ...THIS PAGE LEFT INTENTIONALLY BLANK...
Page 210: ...THIS PAGE LEFT INTENTIONALLY BLANK...
Page 215: ...THIS PAGE LEFT INTENTIONALLY BLANK...
Page 216: ...THIS PAGE LEFT INTENTIONALLY BLANK...
Page 217: ...THIS PAGE LEFT INTENTIONALLY BLANK...