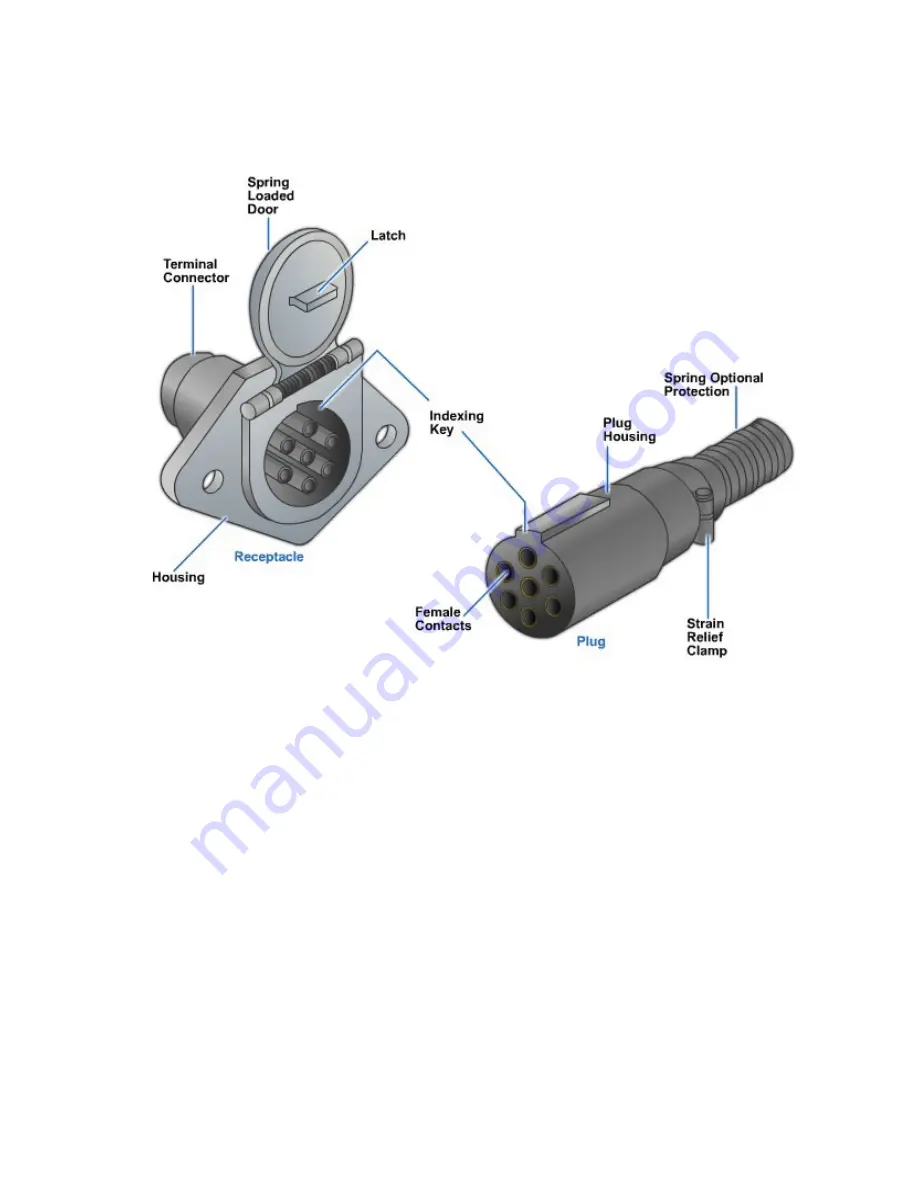
Trailer connections.
Both the tractor and trailer have a seven-terminal trailer
receptacle that accepts the trailer electrical cable plug (
Figure 6-54
). Trailers used as a
part of double and triple trailers have trailer receptacles at both the front and rear of the
trailer to provide interconnection between trailers and dollies.
Figure 6-54 - Tractor-trailer connectors.
Because most tractors do not pull the same trailer all the time, the trailer receptacle and
cable are standardized throughout North America. The trailer interconnection is defined
by SAE recommended practice J560. Each of the seven circuits on all trucks and
trailers should be wired in the prescribed manner to permit tractors and trailers
throughout North America to be interchangeable.
NAVEDTRA 14050A
6-53