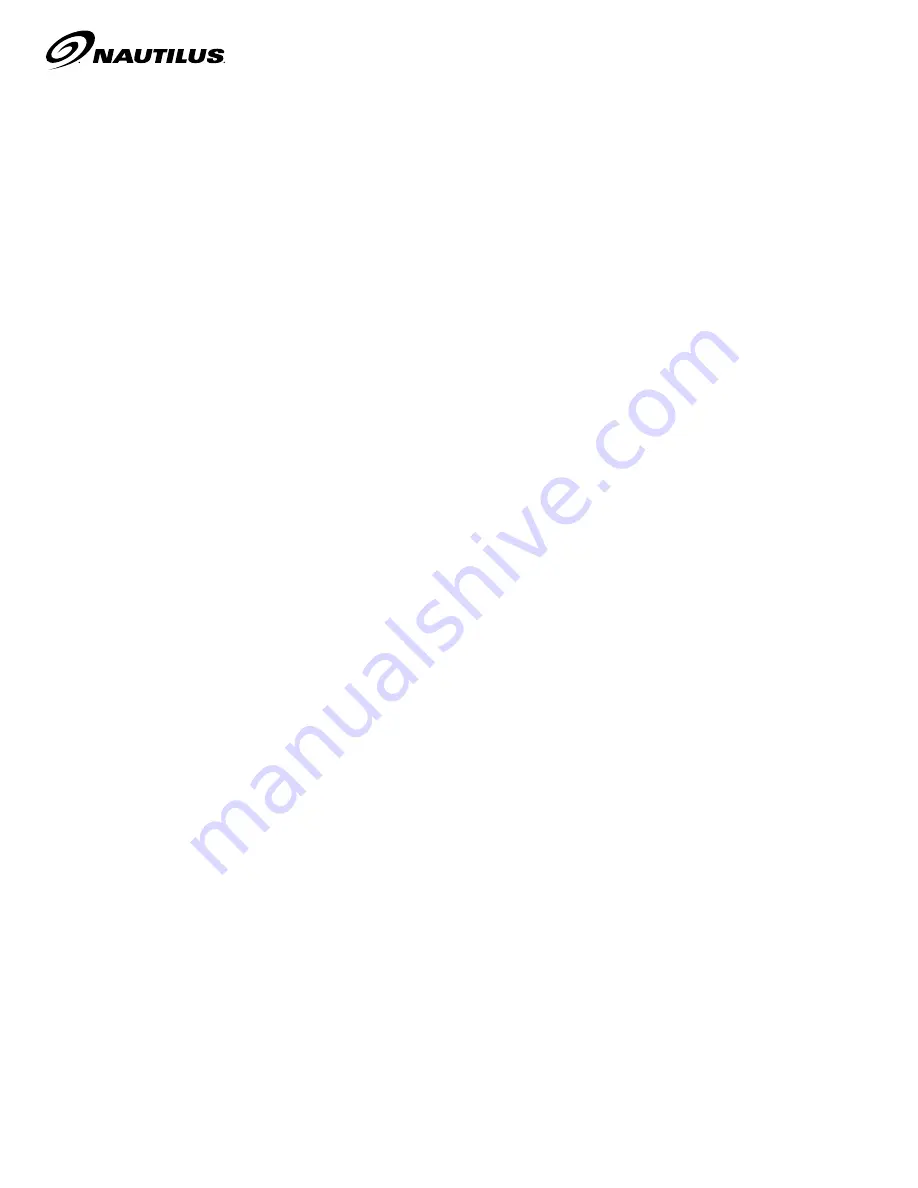
1
Nautilus
®
U624/U626 (Model Year 2014)
Upright Bikes Service Manual
8008323.040115.A
Service Manual
Important Safety Instructions
2
Safety Warning Labels and Serial Number
3
Reading the Product Specification Label
3
Specifications
3
Maintenance 4
Leveling the Machne
5
Moving the Machine
5
Troubleshooting 6
Console Service Mode
8
Maintenance Parts Exploded View
10
Replacement Procedure Skill Level
12
Mechanical Procedures
13
Belt Tension Adjustment
13
Set the Brake Tension (Calibration)
16
Part Replacement
19
Console
19
Pedals
21
Crank Arms – U626
23
Transport Wheels, Front Endcaps and Footpads
27
Shrouds
29
Handlebar Assembly
34
Console Mast
37
Data Cable in the Mast
41
Brake Assembly
44
Servo Motor
46
Drive Belt and Flywheel Assembly
50
Belt Tensioner Assembly (Idler Assembly)
53
Drive Pulley Assembly (Crank Assembly) – U624
55
RPM Sensor (Speed Sensor)
58
Power Inlet
60
Table of Contents
Nautilus, Inc., www.NautilusInc.com - Customer Service: [email protected] | 18225 NE Riverside Parkway, Portland, OR 97230 USA | © 2014 Nautilus, Inc. | ® indicates trademarks
registered in the United States. These marks may be registered in other nations or otherwise protected by common law. Polar
®
and Bluetooth
®
are registered trademarks of their
respective owners.
ORIGINAL DOCUMENT - ENGLISH VERSION ONLY