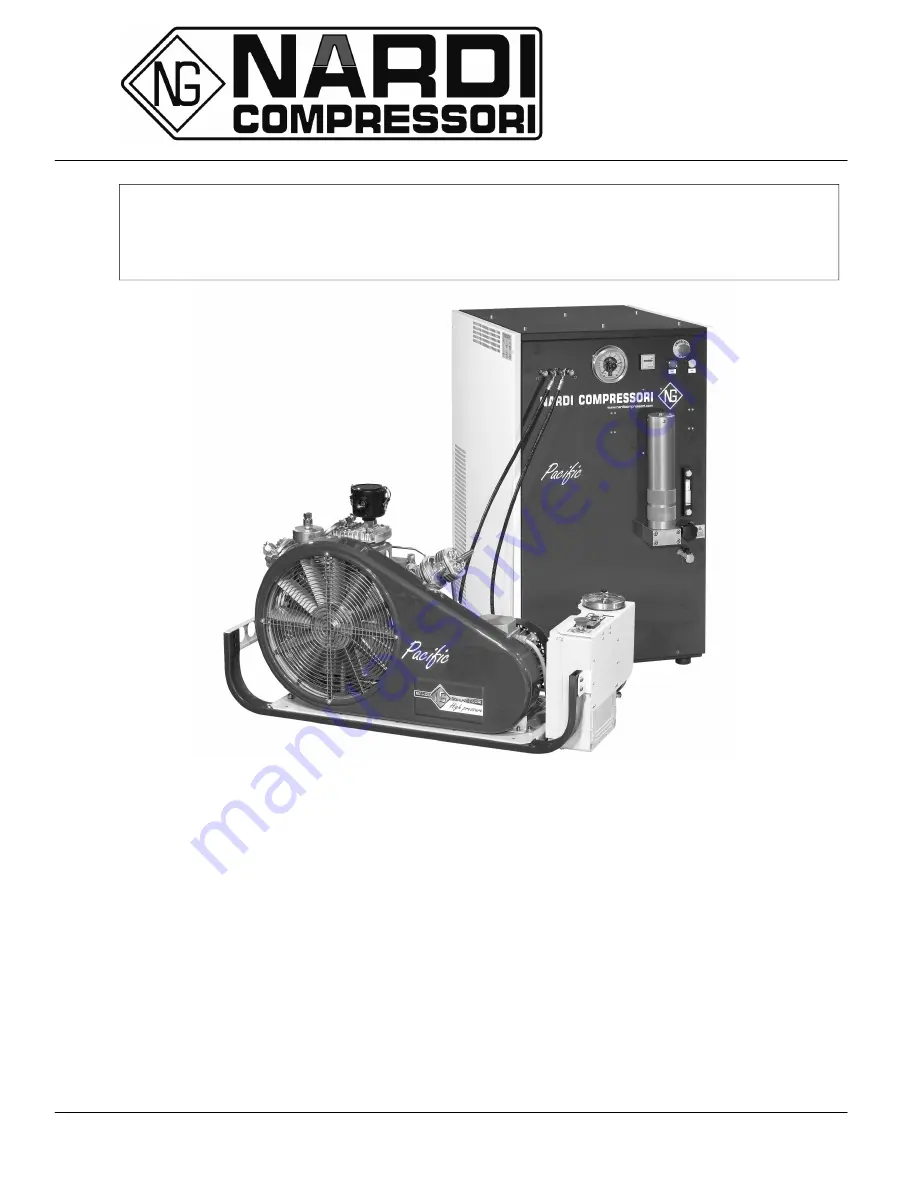
1
Instruction Manual and Spare Parts Catalogue
Pacific 210
This manual contains operating instructions and maintenance schedules for the high
pressure breathing air compressors. Operators must read and understand all
information inside the manual.
ATTENTION.
This machine can be used only after a careful reading of this instruction
manual. The machine may only used to produce compressed air. Other use is strictly
prohibited. The manufacturer and the supplier void all responsibility for damage or injury
resulting from failure to follow these instructions.
ENGLISH INSTRUCTION MANUAL