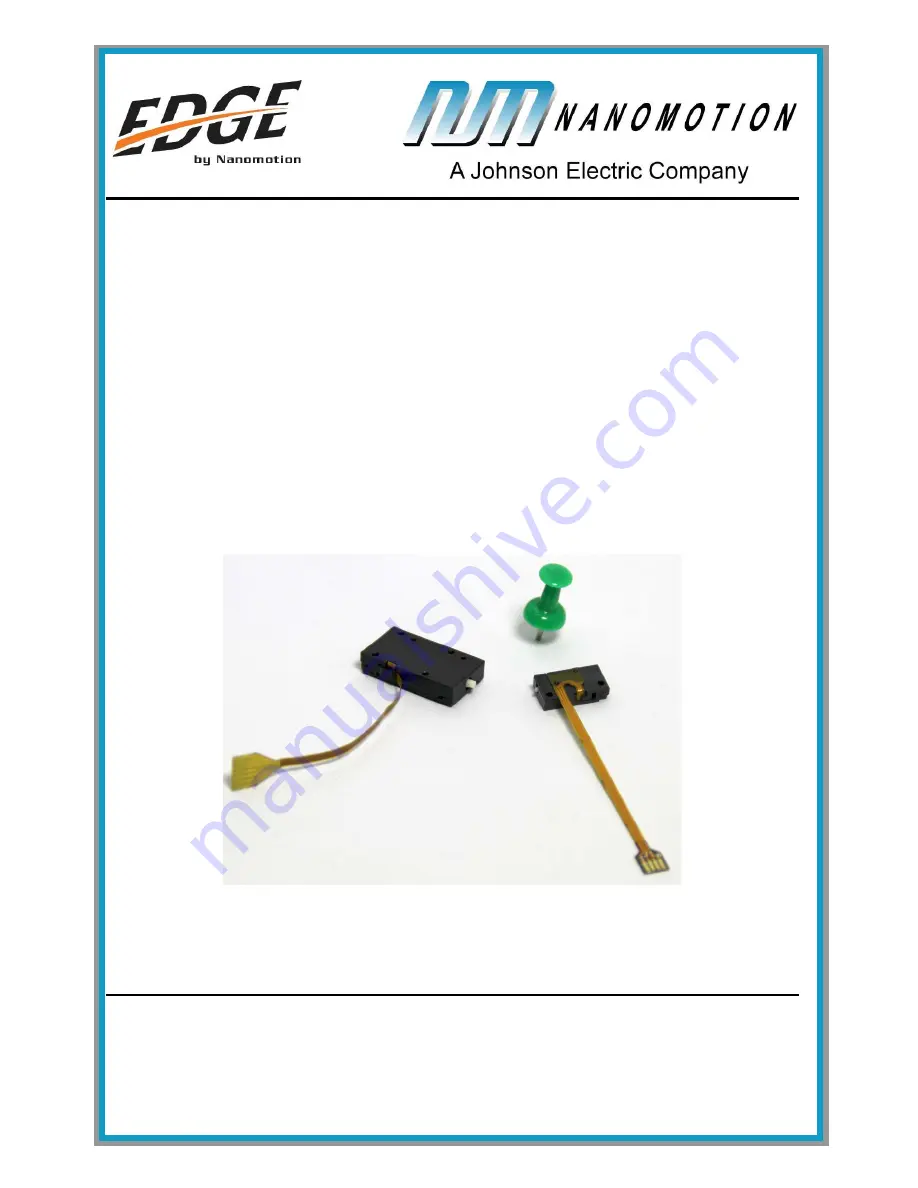
EDGE458001-01 REV:A
Dec 2016
Nanomotion Ltd. POB 623, Yokneam 20692, Israel
Tel: 972-73-2498000 Fax: 972-73-2498099
Web Site: www.nanomotion.com
E-mail: [email protected]
EDGE & EDGE-4X
Motors
User Manual
EDGE458001-01 REV:A
Dec 2016
Nanomotion Ltd. POB 623, Yokneam 20692, Israel
Tel: 972-73-2498000 Fax: 972-73-2498099
Web Site: www.nanomotion.com
E-mail: [email protected]
EDGE & EDGE-4X
Motors
User Manual