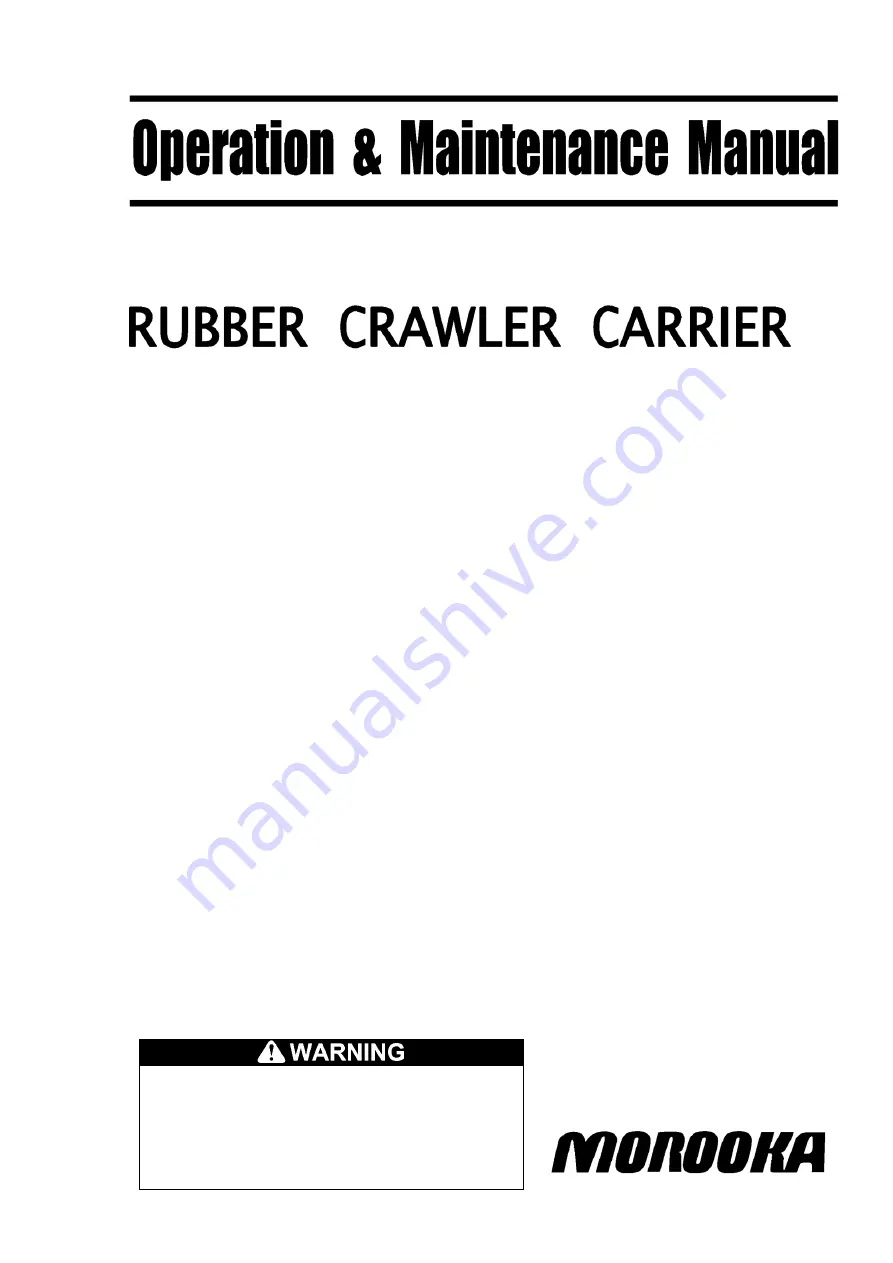
AE10800VD2-01
MST-800VD
Serial No. 4001 and up
Unsafe use of this machine may cause serious injury or
death. Operators and maintenance personnel must read
this manual before operating or maintaining this
machine. This manual should be kept near the machine
for reference and periodically reviewed by all personnel
will come into contact with it.
Summary of Contents for MST-800VD
Page 2: ......
Page 6: ...A 4 ...
Page 12: ...0 6 ...
Page 34: ...1 22 ...
Page 131: ...4 1 SPECIFICATIONS 1 DIMENSIONDRAWING 4 2 2 SPECIFICATIONSTABLE 4 3 ...
Page 132: ...4 2 1 DIMENSION DRAWING CabSpecifications CanopySpecifications ...