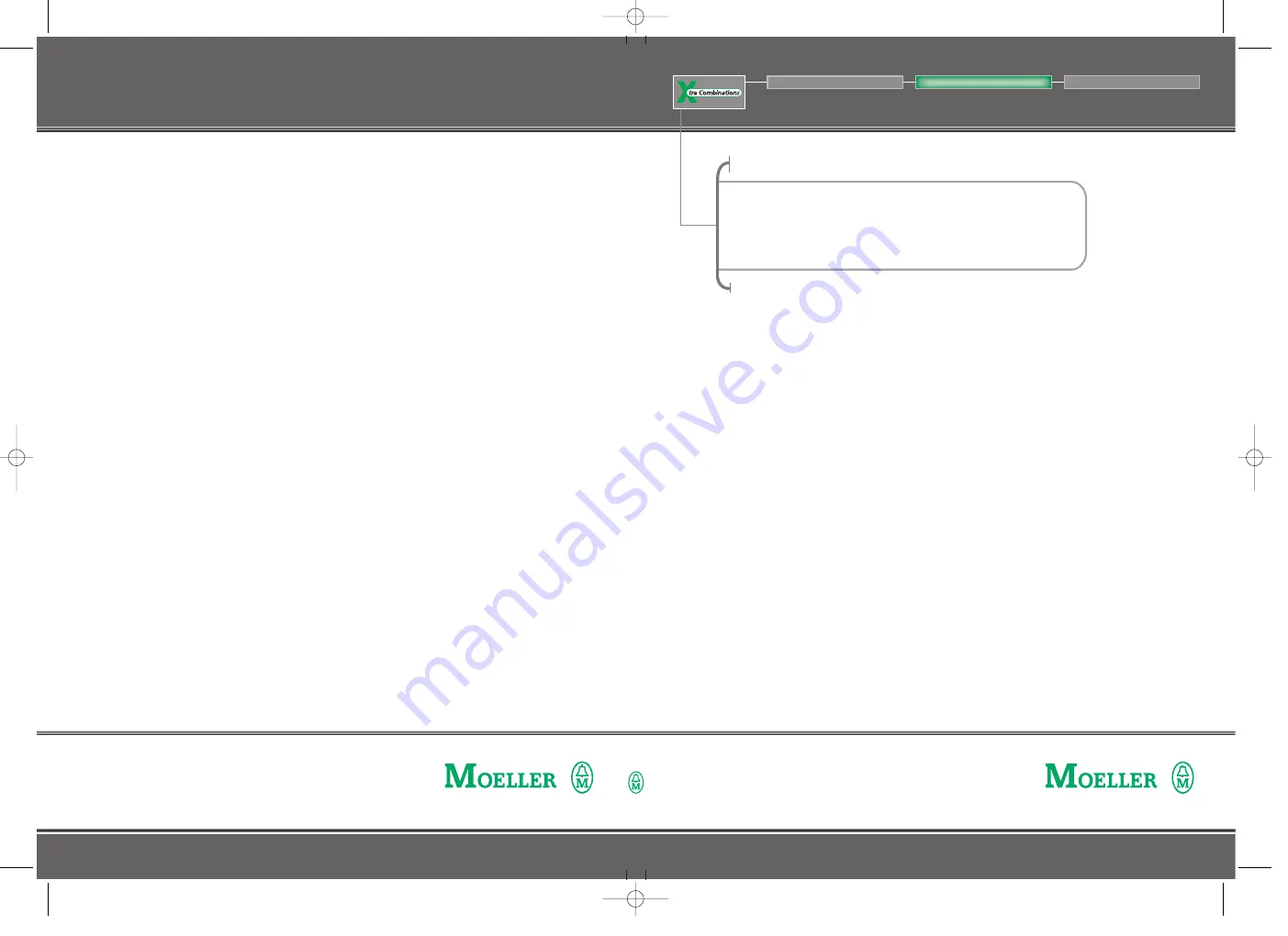
Moeller GmbH
Industrial Automation
Hein-Moeller-Str. 7–11
D-53115 Bonn
E-Mail: [email protected]
Internet: www.moeller.net
© 2001 by Moeller GmbH
Subject to alteration
AWB2700-1409GB DMD/MDS/B+W 04/01
Printed in the Federal Republic of Germany (04/01)
Article No.: 231344
Hardware and Engineering
CM4-505-GV1
CM4-505-GV2
AS-i/PROFIBUS-Gateways
Think future. Switch to green.
Think future. Switch to green.
Systems
Industrial Automation
Building Automation
AWB2700-1409GB 04/01
CM4-505-GV
. AS-i/PROFIBUS-Gateways
AWB 2700-1409 GB (Bund 5mm) 18.05.2001 11:48 Uhr Seite 1
Summary of Contents for CM4-505-GV1
Page 2: ......
Page 6: ...AS i PROFIBUS Gateway The Used Symbols issue date 22 6 2001 6 ...
Page 8: ...AS i PROFIBUS Gateway Safety issue date 22 6 2001 8 ...
Page 16: ...AS i PROFIBUS Gateway Connections Displays and Operating Keys issue date 22 6 2001 16 ...
Page 22: ...AS i PROFIBUS Gateway Operating the AS i PROFIBUS Gateway issue date 22 6 2001 22 ...
Page 62: ...AS i PROFIBUS Gateway PROFIBUS DP issue date 22 6 2001 62 ...
Page 68: ...AS i PROFIBUS Gateway Commissioning Tools and Accessories issue date 22 6 2001 68 ...
Page 77: ......