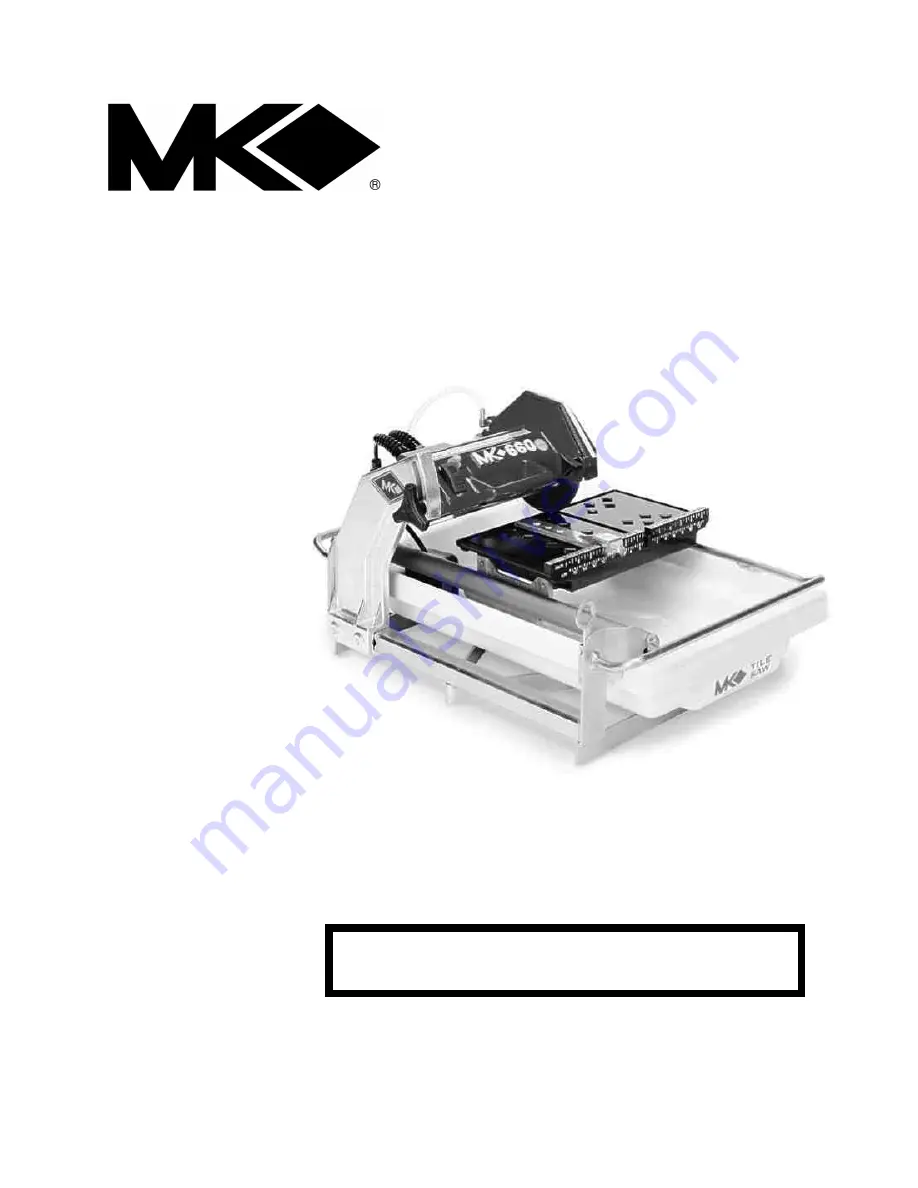
MK-660 SERIES
CAUTION:
Read all safety and
operating instructions
before using this
equipment
TILE SAW
OWNER’S MANUAL &
OPERATING INSTRUCTIONS
Enter the Serial Number of your new saw in the
space below. The Serial Number is located on the
rear of the Cutting Head.
NOTE:
For your (1) one year warranty to be effective,
complete the warranty card (including the Serial
Number and mail it in as soon as possible.
SERIAL NUMBER: