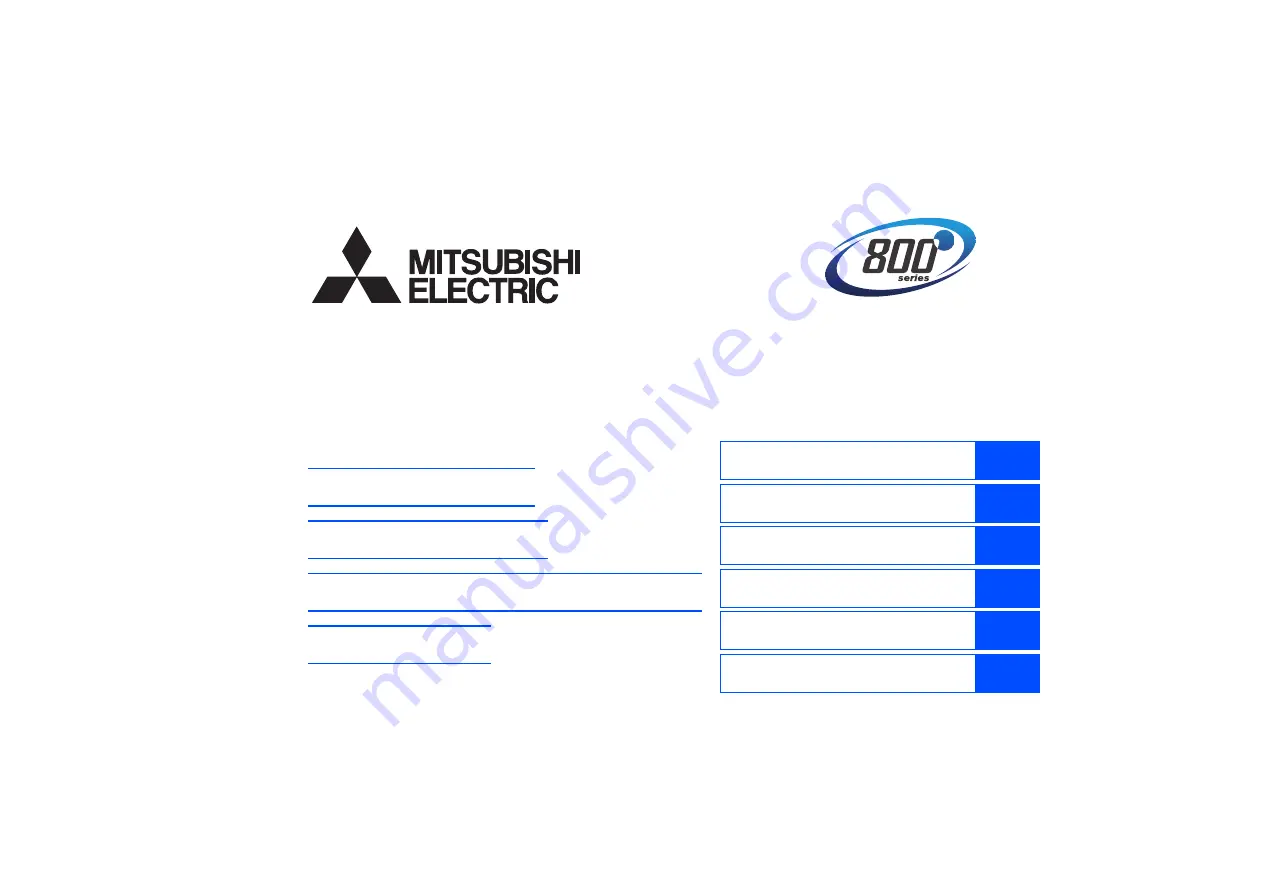
INVERTER
Plug-in option
INSTRUCTION MANUAL
1
2
3
4
RESOLVER (ENCODER) FEEDBACK
CONTROL
5
6
FR-A8APR
Resolver interface
Orientation control
Resolver (encoder) feedback control
Vector control
Summary of Contents for FR-A8APR
Page 37: ...37 MEMO ...
Page 38: ...38 MEMO ...