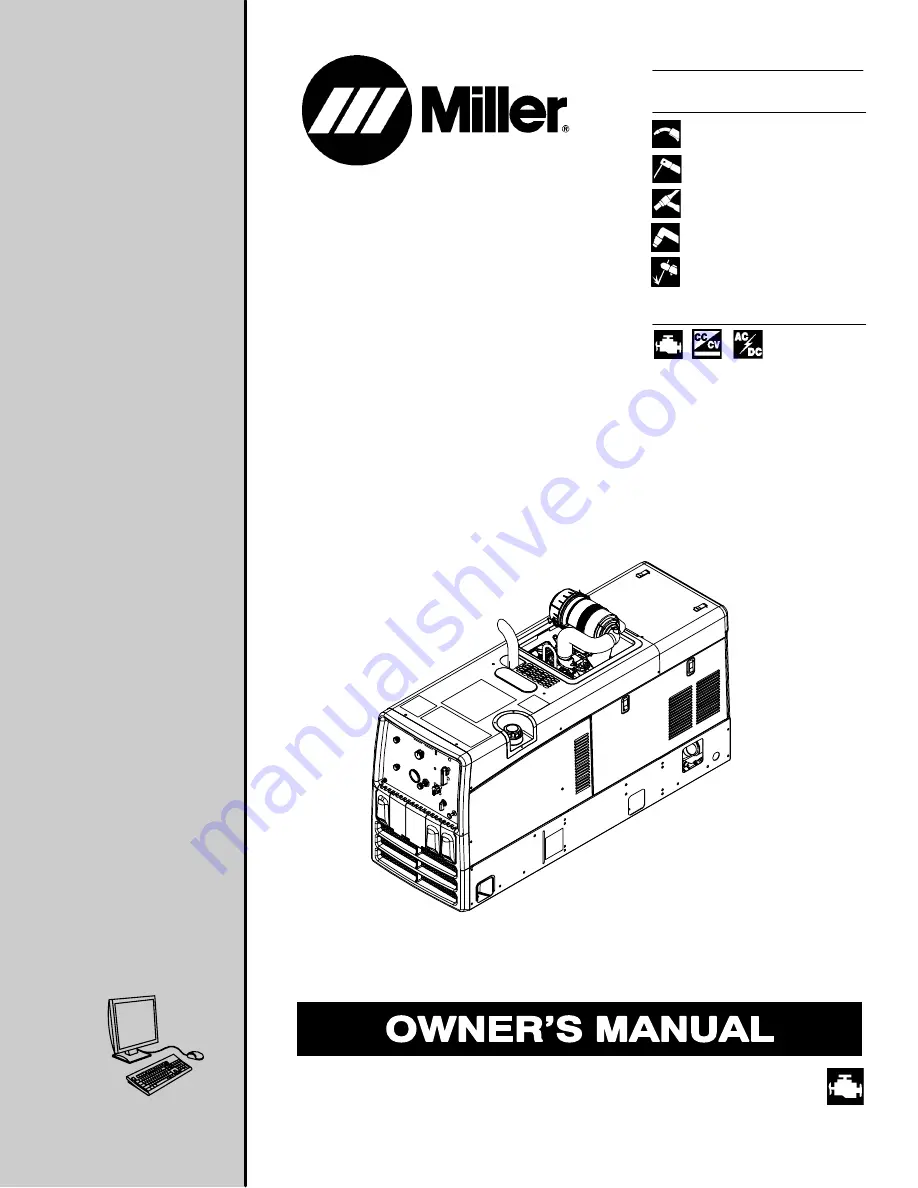
Trailblazer 302 Air Pak
Processes
Description
TIG (GTAW) Welding
Stick (SMAW) Welding
MIG (GMAW) Welding
Flux Cored (FCAW)
OM-229 930A
2009
−
01
Air Plasma Cutting and Gouging
with Spectrum
Unit
Air Carbon Arc (CAC-A) Cutting
and Gouging
Visit our website at
www.MillerWelds.com
File: Engine Drive
Engine Driven Welding Generator And
Air Compressor
™