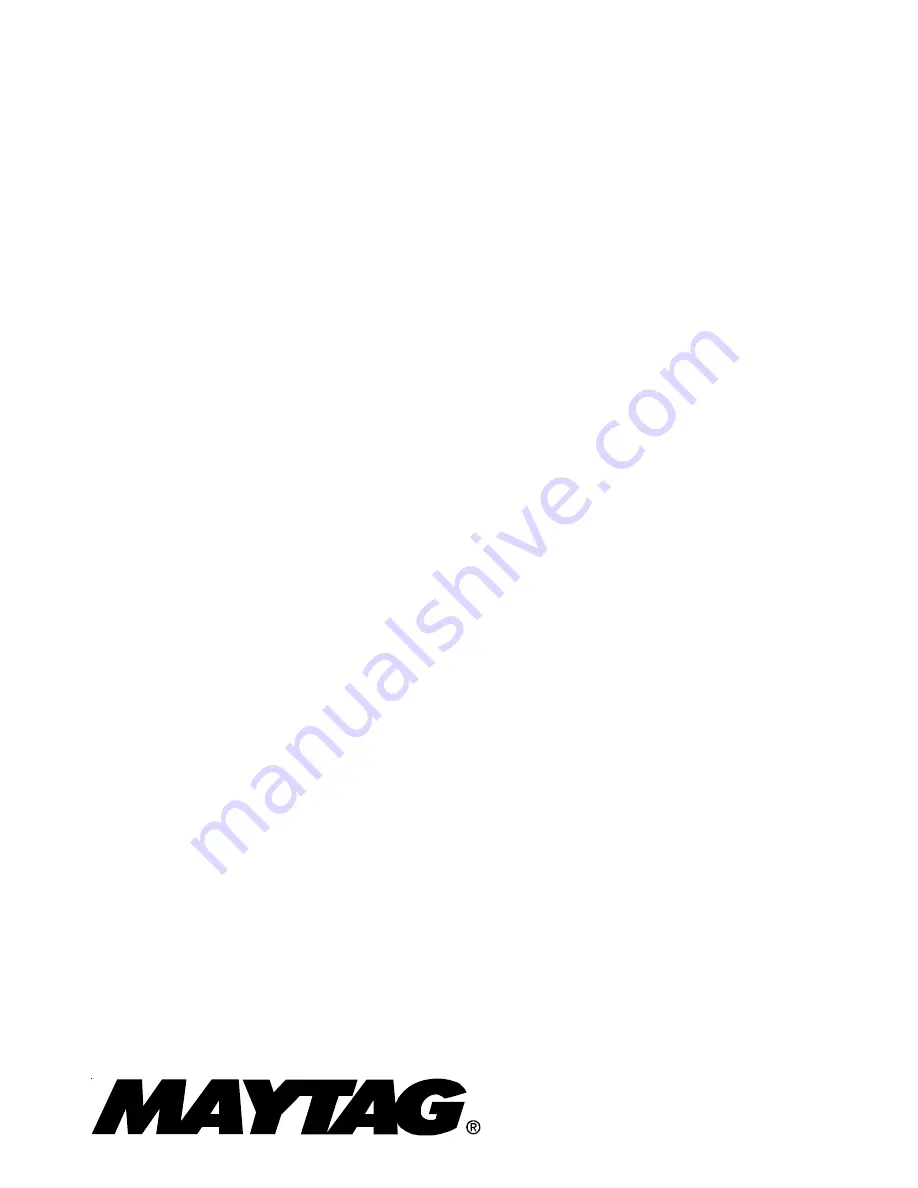
27” Front Load
Washer
This Base Manual covers general information.
Refer to individual Technical Sheet
for information on specific models.
This manual includes, but is
not limited to the following:
MAH9700AW*
Service
This manual is to be used by qualified appliance
technicians only. Maytag does not assume any
responsibility for property damage or personal
injury for improper service procedures done by
an unqualified person.
16025909
March 2005
©2005 Maytag Services
Summary of Contents for MAH9700AW 16025909
Page 7: ... 2005Maytag Services 16025909 Rev 0 7 Important Safety Information ...
Page 42: ...42 16025909 Rev 0 2005 Maytag Services 101504 DC68 02032B ...
Page 43: ... 2005 Maytag Services 16025909 Rev 0 43 ...
Page 44: ...44 16025909 Rev 0 2005 Maytag Services WARNING ...
Page 46: ...46 16025909 Rev 0 2005 Maytag Services ...
Page 48: ...48 16025909 Rev 0 2005 Maytag Services ...
Page 50: ...50 16025909 Rev 0 2005 Maytag Services ...
Page 51: ... 2005 Maytag Services 16025909 Rev 0 51 ...
Page 52: ...52 16025909 Rev 0 2005 Maytag Services ...
Page 53: ... 2005 Maytag Services 16025909 Rev 0 53 ...
Page 54: ...54 16025909 Rev 0 2005 Maytag Services ...
Page 55: ... 2005 Maytag Services 16025909 Rev 0 55 ...
Page 56: ...56 16025909 Rev 0 2005 Maytag Services ...
Page 57: ... 2005 Maytag Services 16025909 Rev 0 57 ...
Page 58: ...58 16025909 Rev 0 2005 Maytag Services ...
Page 59: ... 2005 Maytag Services 16025909 Rev 0 59 ...
Page 60: ...60 16025909 Rev 0 2005 Maytag Services ...
Page 61: ... 2005 Maytag Services 16025909 Rev 0 61 ...
Page 62: ...62 16025909 Rev 0 2005 Maytag Services ...