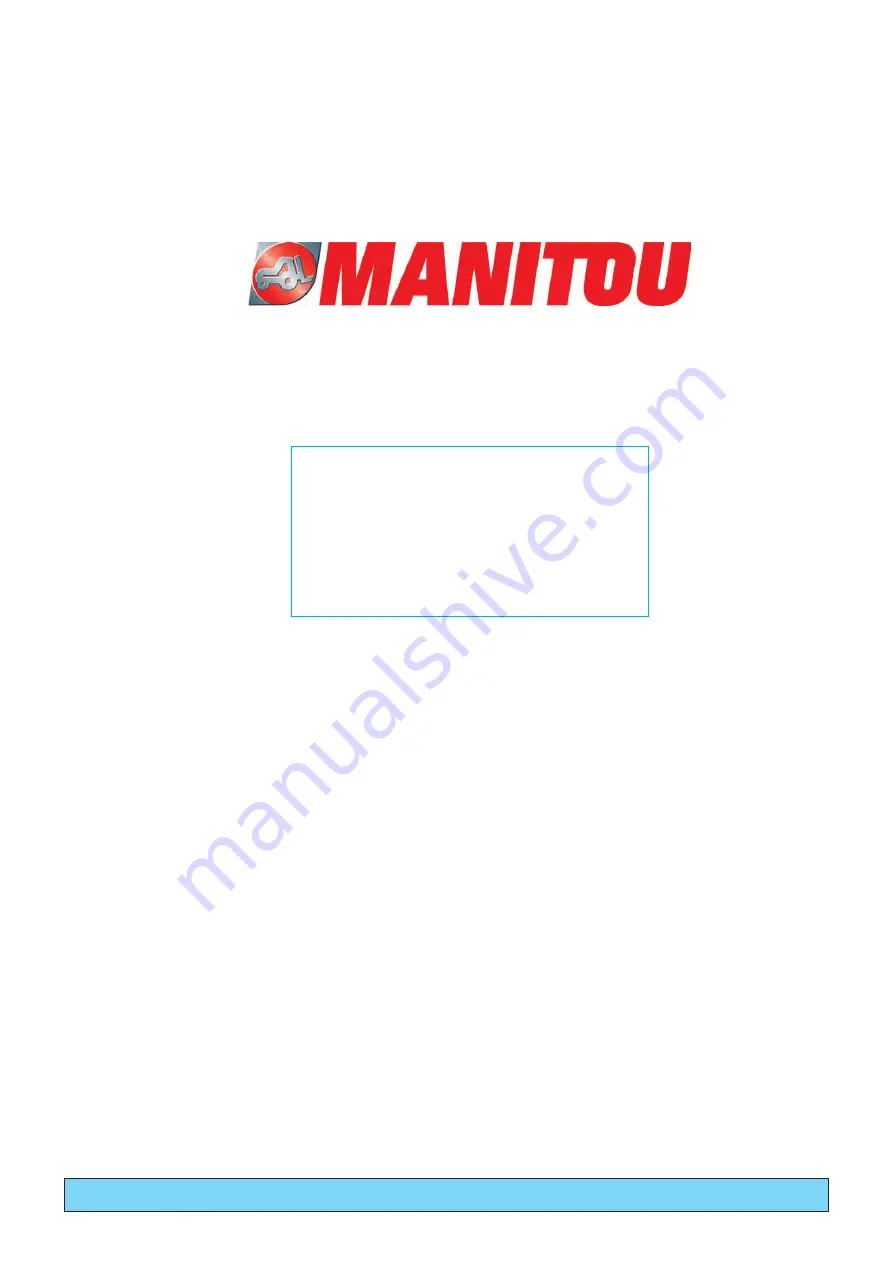
647382 EN (13/02/2015)
260 TJ
280 TJ
MANITOU BF
BP 10249
44158 ANCENIS CEDEX - FRANCE
TEL: + 33 (0)2 40 09 10 11
YOUR DEALER
INSTRUCTIONS MANUAL
(ORIGINAL INSTRUCTIONS MANUAL)
THIS INSTRUCTIONS MANUAL MUST BE KEPT PERMANENTLY IN THE LIFT TRUCK
AND THE OPERATORS MUST HAVE READ AND FULLY UNDERSTOOD IT.
Summary of Contents for 260 TJ
Page 4: ...FRONT REAR 260 TJ 280 TJ 647382 EN 01 02 2015...
Page 6: ...1 2 647382 EN 01 02 2015...
Page 25: ...1 21 647382 EN 01 02 2015...
Page 40: ...1 36 647382 EN 01 02 2015...
Page 41: ...2 1 2 DESCRIPTION 2 DESCRIPTION 647382 EN 01 02 2015...
Page 42: ...2 2 647382 EN 01 02 2015...
Page 73: ...2 33 647382 EN 01 02 2015...
Page 92: ...2 52 647382 EN 01 02 2015...
Page 94: ...2 54 647382 EN 01 02 2015...
Page 95: ...3 1 3 MAINTENANCE 3 MAINTENANCE 647382 EN 01 02 2015...
Page 96: ...3 2 647382 EN 01 02 2015...
Page 135: ...4 1 4 ELECTRICITY 4 ELECTRICITY 647382 EN 01 02 2015...
Page 136: ...4 2 647382 EN 01 02 2015...
Page 138: ...4 4 647382 EN 01 02 2015...