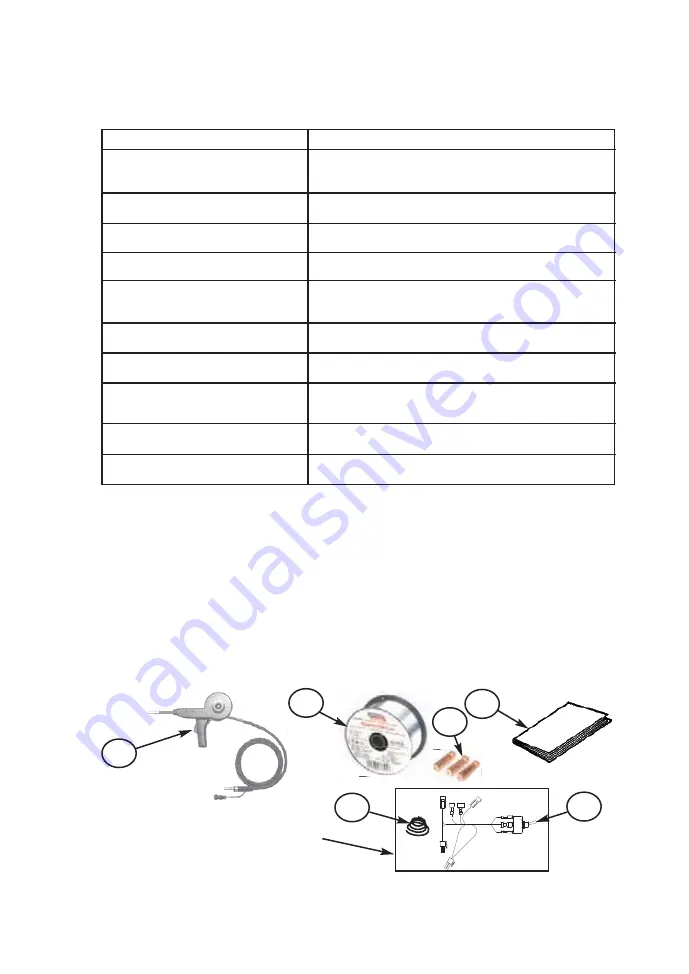
INSTALLATION
TECHNICAL SPECIFICATIONS - MAGNUM
®
100SG SPOOL GUN K2532-1
MODEL
WELDING PROCESS
WIRE ALLOYS
WIRE SIZES (DIAMETERS)
SPOOL SIZE
RATED WELDING CURRENT
AND DUTY CYCLE
OVERALL WEIGHT
CABLE LENGTH
OVERALL SIZE (BOUNDING BOX)
METHOD OF GUIDANCE
METHOD OF COOLING
K25
3
2-1
M
agnum
®
100S
G
S
p
ool
G
un
Aluminum
GM
AW
(M
I
G)
, DC electrode
p
ositive
p
olarit
y
with 100% argon welding shielding gas.
Aluminum onl
y
: allo
y
s 404
3
or 5
3
56
Solid wire 0.0
3
0 or 0.0
3
5 inches
(
0.8 or 0.9 mm
)
1 lb. weight, nominal 4 inch diameter s
p
ool
1
3
0 am
p
s at
3
0%
f
or 10-minute basis
3
.5 lbs. with cable but without case or s
p
ool
10.0±0.2
f
eet
In inches: 15.75 long x 10.50 high x 4.25 thick max.,
without case or gun cable.
Semiautomatic
(
manuall
y
-guided
)
Air-cooled
UNPACKING THE SPOOL GUN
The s
p
ool gun is
f
actor
y
-assembled and tested, and then
p
acked in its own cush-
ioned carr
y
ing case. It is shi
pp
ed
f
ull
y
-e
q
ui
pp
ed to weld with 0.0
3
5 inch diameter alu-
minum wire. A
f
ter o
p
ening the case, check that it contains the
f
ollowing items:
1. One
f
ull
y
assembled K25
3
2-1 s
p
ool gun.
2. One T11862-65 Conical Com
p
ression S
p
ring
f
or use with allo
y
5
3
56 wire
(
s
p
ool
not included
)
.
3
. One s
p
ool o
f
0.0
3
5 aluminum allo
y
404
3
wire
4. Three S19726-
3
contact ti
p
s
5. One instruction manual
(
I
M
91
3)
6. One
M
21182 electrical harness with toggle switch.
1
3
4
5
6
2
A-1
Plastic Bag