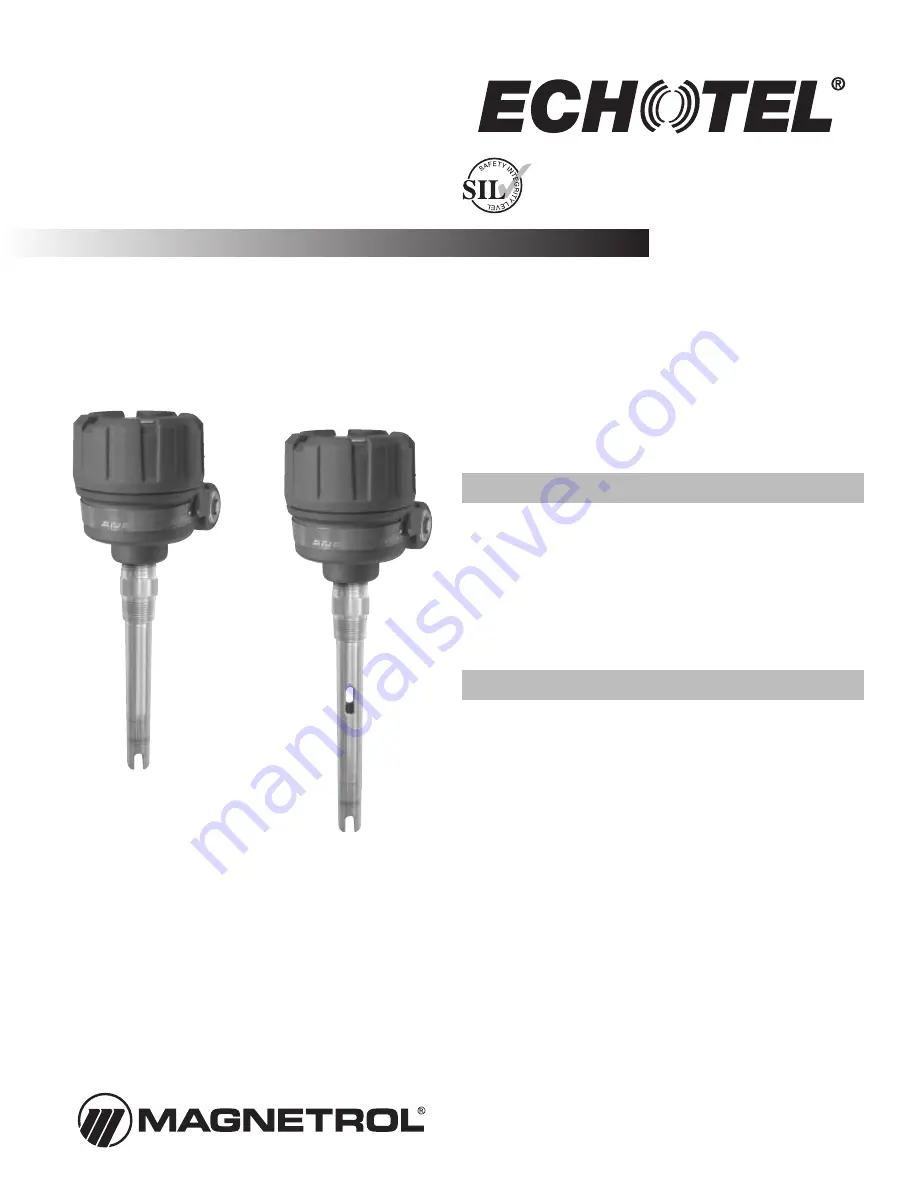
Ultrasonic
Level Switches
SIL Safety Manual for
Echotel
®
Model 961/962
Application
Echotel
®
Model 961/962 ultrasonic level switches utilize
pulsed signal technology to detect high, low, or dual-
point level in a broad range of liquid media applications.
The advanced self-test technology provides reliability
and continuous testing of electronics, transducer, piezo-
electric crystals, and electromagnetic noise.
Benefits
The Echotel Model 961/962 ultrasonic level switches
provide the following benefits:
• Single- or dual-point liquid level measurement
• Adjustable time-delay for turbulent aerated liquids
• Reliable liquid level measurement independent of
changes in media density, conductivity, or temperature
• Two-wire mA current shift and relay output options
• Relay output or mA current shift with separate
malfunction indication
• Integral or remote mount electronics
• Pulsed signal technology
• Extensive FM, CSA, ATEX and IEC explosion proof
and intrinsically safe approvals
• Suitable for Safety Integrity Level (SIL) 2 loops
Functional Safety Manual
This manual complements and is intended to be used with
the Magnetrol
Echotel
®
Model 961/962 Ultrasonic Single and
Dual Point Level Switches Installation and Operating Manual
(Bulletin 51-646).
Model 961
Model 962