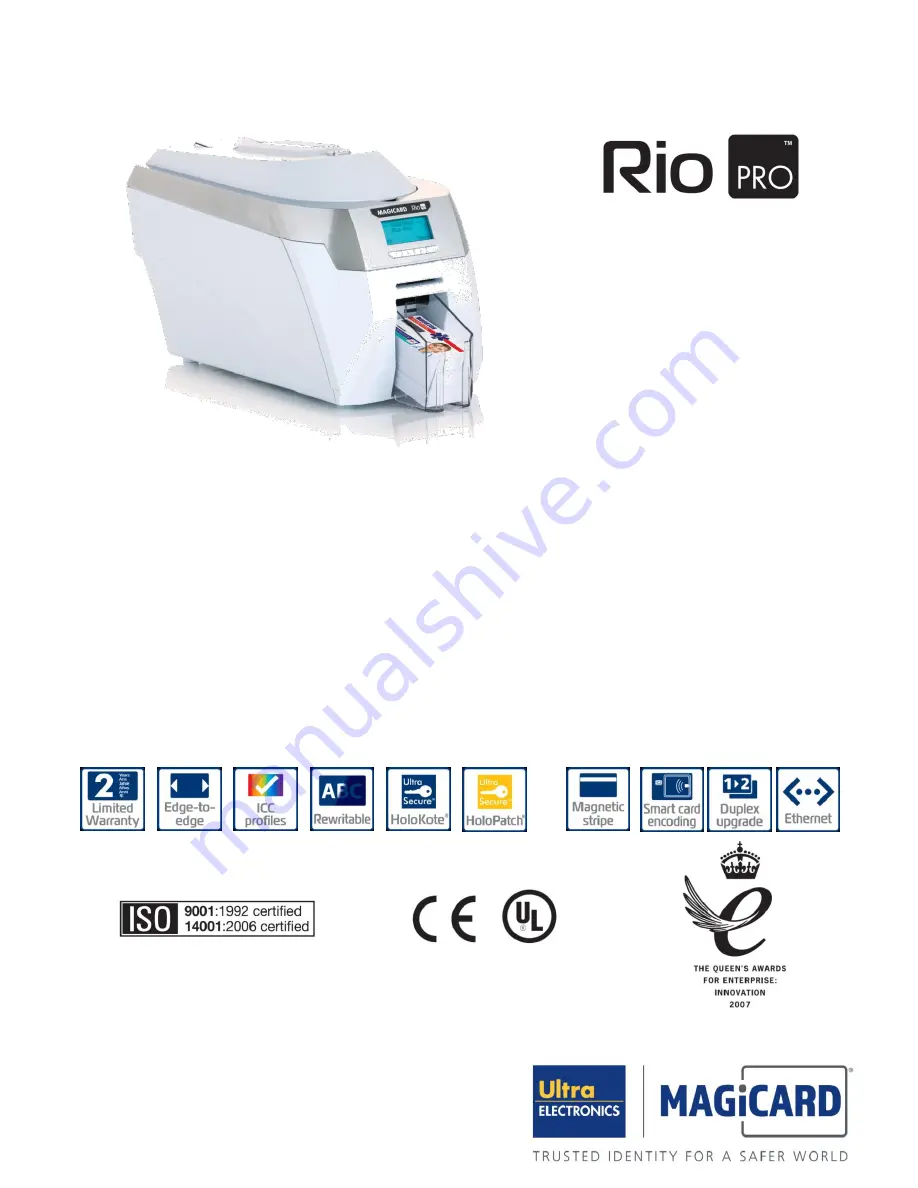
Issue 2
10/12/2010
Colour ID Card Printer MAGICARD
®
Rio Pro Maintenance Manual
Ultra Electronics Card Systems
www.magicard.com
Magicard Rio Pro single sided colour ID Card Printer
-
3633-9001
Magicard Rio Pro Duo double sided colour ID Card Printer
-
3633-9021
Magicard Rio Pro Mag single sided colour ID Card Printer
-
3652-9002
Magicard Rio Pro Duo Mag double sided colour ID Card Printer
-
3652-9022
Magicard Rio Pro single sided colour ID Card Printer with Smart Encoder
-
3652-9005
Magicard Rio Pro Duo double sided colour ID Card Printer with Smart Encoder
-
3652-9025
Magicard Rio Pro Mag single sided colour ID Card Printer with Smart Encoder
-
3652-9006
Magicard Rio Pro Duo Mag double sided colour ID Card Printer with Smart Encoder
-
3652-9026
Duplex Upgrade Kit
-
3633-0052
Standard
Option
Option
Standard
Standard
Standard
Standard
Standard
Option
Option
Summary of Contents for Rio Pro
Page 27: ...Ultra Electronics Card Systems Rio Pro Maintenance Manual 27 ...
Page 60: ...Ultra Electronics Card Systems Rio Pro Maintenance Manual 60 ...
Page 72: ...Ultra Electronics Card Systems Rio Pro Maintenance Manual 72 ...
Page 105: ...Ultra Electronics Card Systems Rio Pro Maintenance Manual 105 ...
Page 108: ...Ultra Electronics Card Systems Rio Pro Maintenance Manual 108 ...