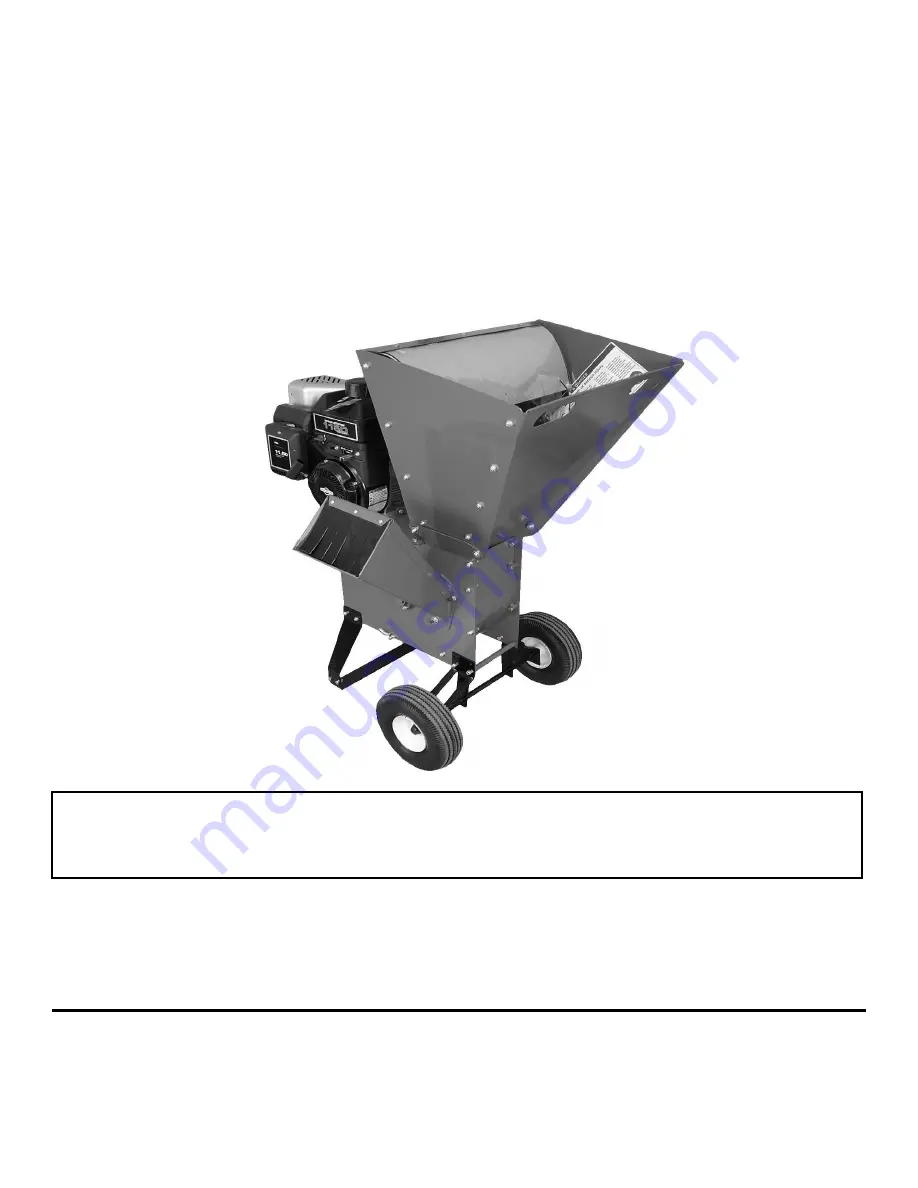
OWNER’S MANUAL
SC300M
SHREDDER-CHIPPER
ASSEMBLY AND OPERATING INSTRUCTIONS
.
This manual contains information concerning proper and improper operating procedures, warnings,
maintenance, trouble shooting, assembly, tips. Everyone who operates this machine should read
these instructions and be thoroughly familiar with them.
THIS MACHINE IS CAPABLE OF INFLICTING
SERIOUS INJURY IF OPERATED IMPROPERLY
- READ WARNINGS AND CAUTION LABELS -
MACKISSIC, INC. P.O. BOX 111, PARKER FORD, PA 19457-0111
PHONE: 1-800-348-1117 e-mail: [email protected] Fax: (610) 495-5951
3/2018
Summary of Contents for SC300M
Page 25: ...Schematic BASIC MACHINE ASSEMBLY 25...
Page 29: ...Schematic HOPPERS AND SCREEN 29 5...
Page 31: ...Schematic SHREDDER HOPPER 31...
Page 33: ...Schematic ROTOR ASSEMBLY 33...
Page 34: ...Notes 34...
Page 35: ...Notes 35...