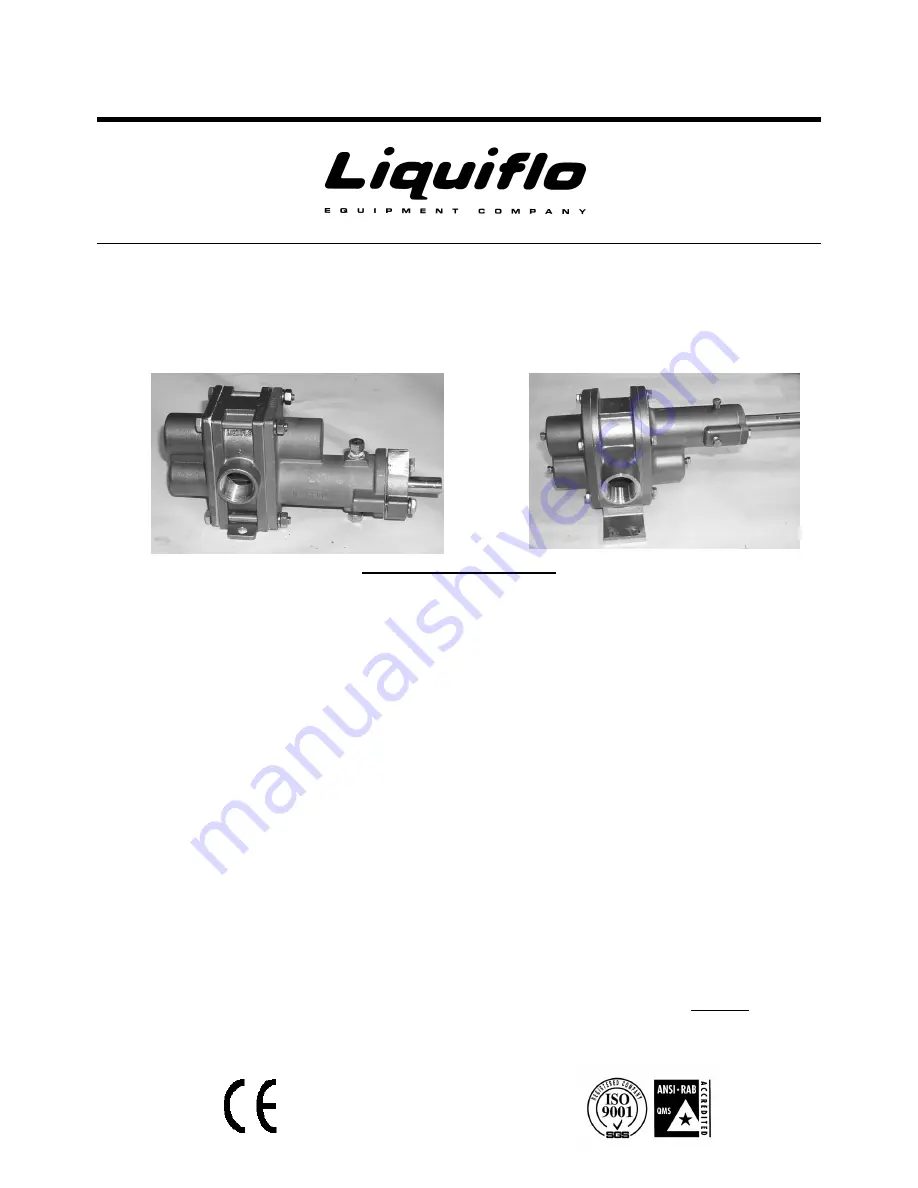
INSTALLATION and MAINTENANCE MANUAL
3 and H-SERIES
ROTOGEAR
A
SEALED PUMPS
TABLE OF CONTENTS
General Instructions
Symbol Explanation
Pump and Motor Installation
Start Up
Special Precautions for various seals
Removal from System
Maintenance and Repair
Pump Disassembly
Section (A)
Packed stuffing box
Section (B)
Lip Seal
Section (C)
Single internal mechanical seal
Section (D)
External mechanical seal
Section (E)
Double mechanical seal
Trouble Shooting
Document No.: 3.20.073
Liquiflo Equipment Co. 443 North Avenue Garwood, NJ 07027 USA Tel 908-518-0666 Fax 908-518-1847