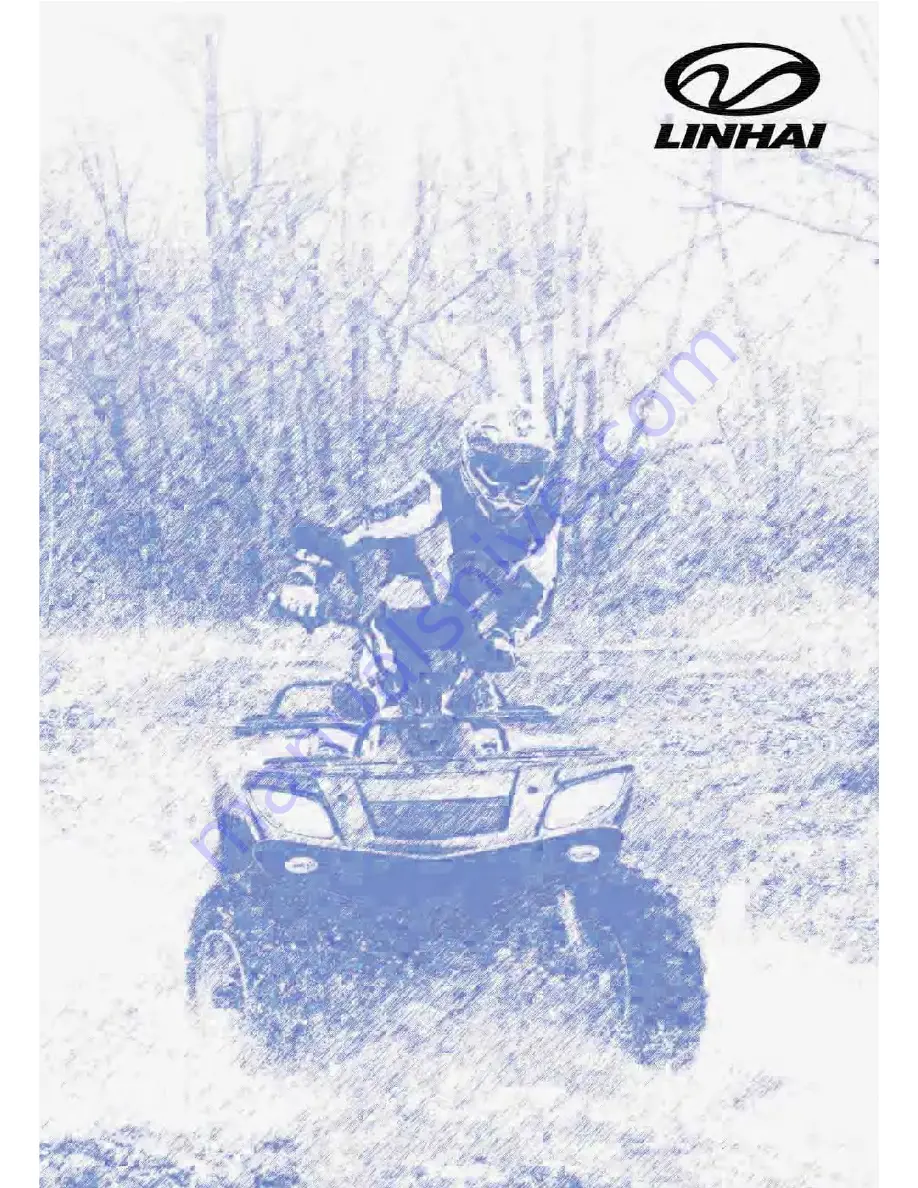
2007 ATV
SERVICE MANUAL
USA 07.0
PN. F010103A01
●
ATV 260/300
Model
:
2004
2005
Special Edition - Anniversary
2x4
4x4
●
B-Type ATV 150/200, 2x4
●
B-Type ATV 260/300, 2x4/ 4x4
●
Youth ATV 50/80
WARNING
The parts of different types/ variants/ versions maybe un-interchangeable, even some parts
have almost same appearance. Always refer to Parts Manual of each ATV model for spare
parts information and service.
※
General Information
※
Maintenance
※
Engine
※
Chassis
※
Final Drive
※
Transmission
※
Brakes
※
Electrical
Summary of Contents for 2005 ATV 260
Page 15: ...CHAPTER 1 GENERALINFORMATION ATV SERVICE MANUAL 07 0 CHAPTER 1 GENERAL PAGE 1 11 NOTES...
Page 37: ...CHAPTER 2 MAINTENANCE ATV SERVICE MANUA 07 0 CHAPTER 2 MAINTENANCE PAGE 2 22 NOTES...
Page 106: ...CHAPTER 3A ENGINE 260 300 cc ATV SERVICE MANUAL07 0 CHAPTER 3 ENGINE PAGE 3A 69 NOTES...
Page 157: ...CHAPTER 3B ENGINE 50cc 80cc ATV SERVICE MANUAL07 0 CHAPTER 3B ENGINE PAGE 3B 51 3 8 Carburetor...
Page 177: ...CHAPTER 3B ENGINE 50cc 80cc ATV SERVICE MANUAL07 0 CHAPTER 3B ENGINE PAGE 3B 71 NOTES...
Page 213: ...CHAPTER 3C ENGINE 100 125 150 200 SERVICE MANUAL07 0 CHAPTER 3C ENGINE PAGE 3C 36 NOTES...
Page 232: ...CHAPTER 4B CHASSIS ATV SERVICE MANUAL07 0 CHAPTER 4 CHASSIS PAGE 4B 11 NOTES...
Page 261: ...CHAPTER 5 FINAL DRIVE ATV SERVICE MANUAL 07 0 CHAPTER 5 FINAL DRIVE 5 29 NOTES...
Page 276: ...CHAPTER 6 TRANSMISSION ATV SERVICE MANUAL 07 0 CHAPTER 6 TRANSMISSION PAGE 6 15 NOTES...
Page 289: ...CHAPTER 7 BRAKES ATV SERVICE MANUAL 07 0 CHAPTER 7 BRAKES PAGE 7 13 NOTES...
Page 297: ...CHAPTER 8 ELECTRICAL ATV SERVICE MANUAL 07 0 CHAPTER 8 ELECTRICAL PAGE 8 8 CIRCUIT DIAGRAM...
Page 331: ......
Page 332: ......
Page 333: ......
Page 334: ......
Page 335: ......
Page 336: ......
Page 337: ......
Page 338: ......
Page 339: ......
Page 340: ...ATV SERVICE MANUAL 07 0 NOTES...
Page 341: ...9B 9 939397 93...